Ridurre le emissioni e risparmiare risorse: i progetti del Carbon Fund
Il Carbon Fund del Gruppo Volkswagen è stato istituito solo dieci mesi fa, ma ha già sostenuto molti progetti di successo nel 2019. Il totale delle emissioni di CO₂ risparmiate ha raggiunto le 170.000 tonnellate e l’iniziativa proseguirà anche nel 2020.
Ideare e attivare progetti interni per la riduzione delle emissioni di CO2: questo è l’obiettivo con il quale è nato agli inizi del 2019 il Carbon Fund del Gruppo Volkswagen. Grazie ai 25 milioni di Euro dedicati e al lavoro congiunto di tutti i brand, i risultati in termini di impatto ambientale sono già evidenti.
Come funziona il Carbon Fund
Ogni brand del Gruppo può accedere al fondo, a patto che presenti un progetto per ridurre le emissioni di CO₂, migliorare l'efficienza energetica ed evitare sprechi di risorse in generale. L'intento è anche quello di accelerare l'innovazione, puntare su nuovi modelli di business, promuovere la collaborazione tra reparti e sostenere progetti validi, ad alto impatto. Il requisito fondamentale affinché il progetto venga approvato? Dev’essere trasferibile e replicabile in diverse sedi e impianti.
Durante il primo anno di attività, la commissione del Carbon Fund ha approvato 94 progetti: per il 2020 ne sono già stati individuati oltre 100, e la selezione proseguirà mese dopo mese. Il fondo è parte integrante della strategia di decarbonizzazione del Gruppo Volkswagen.
Ecco alcuni esempi dei progetti implementati nel 2019 grazie al Carbon Fund.
“Illuminazione a LED”
In nove stabilimenti del Gruppo sono state introdotte 33 misure, che hanno portato alla sostituzione dei vecchi impianti di illuminazione con LED a basso consumo. Ciò consente una riduzione della CO₂ di 116.000 tonnellate all'anno.
“Sistemi di raffreddamento”
Nell'impianto di Kassel i sistemi di refrigerazione sono stati sostituiti - o sono in corso di sostituzione - con i cosiddetti sistemi a circuito separato. Fino a oggi ne sono stati installati oltre 150: vengono utilizzati per raffreddare macchinari e mandrini e riducono in modo consistente il consumo di energia.
L’immissione di calore nella rete di raffreddamento si è ridotta del 23%, mentre i servizi e gli intervalli di manutenzione sono più lunghi e meno costosi. Nel prossimo futuro, tutti i nuovi impianti saranno dotati di sistemi di questo tipo fin dalla loro costruzione. Nel 2019 sono stati aggiornati 13 stabilimenti, con un taglio delle emissioni di CO2 pari a 1.350 tonnellate all'anno.
“Varie infrastrutture”
Questo progetto prevede l'utilizzo di pompe ad alta efficienza energetica, la ristrutturazione dei tetti e l'installazione di un nuovo sistema di raffreddamento per cabinet. Il progetto è stato avviato all'inizio dello scorso mese di luglio e si è concluso il 31 dicembre, traducendosi in una riduzione totale di 2.000 tonnellate di CO₂ all'anno.
“Verniciatura e asciugatura”
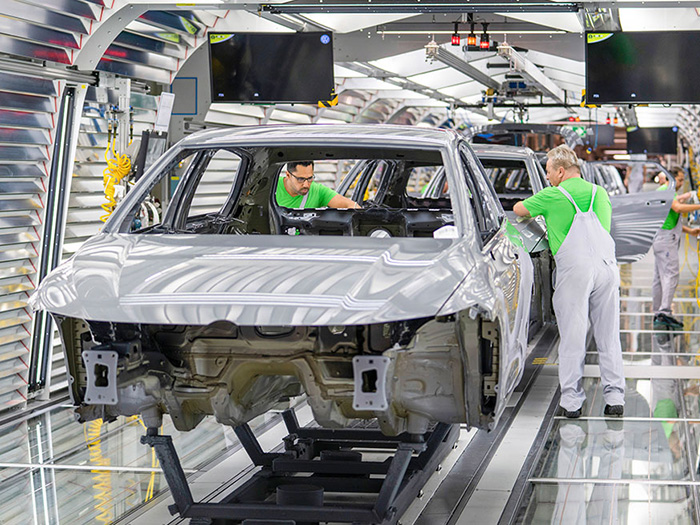
Nello stabilimento di Hannover, Volkswagen ha installato un sistema di controllo del flusso volumetrico legato al carico. Una nuova tecnologia che dopo la prima fase di sperimentazione potrà essere esportata in altre sedi nei prossimi anni e che è in grado di abbattere la CO₂ emessa di 1.200 tonnellate ogni anno, riducendo allo stesso tempo i costi.
Nell’ambito di questo progetto sono state attivate diverse misure che consentono di tagliare 1.800 tonnellate di CO₂ in un anno. La riduzione delle emissioni totale, per questo progetto, è pari a 3.000 tonnellate all’anno.
“Processi di lavaggio”
Gli impianti di lavaggio industriali sono stati ottimizzati in molte sedi del Gruppo Volkswagen: in totale circa trenta sistemi sono stati tecnicamente aggiornati con i cosiddetti convertitori di frequenza.
Parametri operativi come la pressione, il volume del flusso d'acqua, la temperatura e i tempi di stand-by, sono stati ricalibrati. Il progetto è iniziato lo scorso 1 luglio ed è terminato il 31 dicembre, con un taglio della CO₂ emessa di 2.900 tonnellate all'anno.
“Altri processi produttivi”
Una moderna tecnologia di regolazione della temperatura è stata installata su tre macchine per la pressofusione dei metalli. Durante il processo è importante riscaldare e raffreddare le giuste aree della matrice nel momento corretto: per questo negli stampi ci sono fino a 40 circuiti di raffreddamento e riscaldamento.
Grazie a sensori di flusso e temperatura, il sistema di controllo riesce a distribuire il flusso di calore in modo intelligente, con un notevole risparmio di energia, grazie anche al recupero del calore interno. Questo progetto è stato implementato nella seconda metà del 2019, e ha consentito un abbattimento delle emissioni di CO₂ pari a 2.500 tonnellate all'anno.
Fonte: Volkswagen AG