Sustainable materials: vegan leather made from coffee
Volkswagen Group Innovation is working on the next generation of ecological materials for vehicle interiors. Among these is an imitation leather made from silverskin, a film which is removed from coffee beans during roasting.
Leather is a standard material for vehicle interiors: from seat covers to steering wheels, arm rests, decorative panels and shift knobs. When designing the all-electric ID. car family, Volkswagen made the decision to use non-animal materials wherever possible; at the same time, the brand is optimising the carbon footprint of every material and component, with the goal of making the cars as sustainable as possible from all points of view. It is a holistic approach, starting with the raw materials and ending with recycling, taking the entire vehicle life cycle into consideration.
Sustainable imitation leather
In the ID. cars, conventional animal leather is not used. An alternative to replace it is imitation leather, which looks and feels like leather, is easy to clean, is hard-wearing and as such is in great demand in many markets, for example the USA and China.
In order to improve the carbon footprint of vehicle interiors, one option is increasing the percentage of organic materials in imitation leather, which is largely made from plastics containing mineral oil, such as polyurethane or PVC. Imitation leather is a multi-layered material that consists of a textile back, filling materials and the actual surface top layer.
Possible developments: the use of coffee
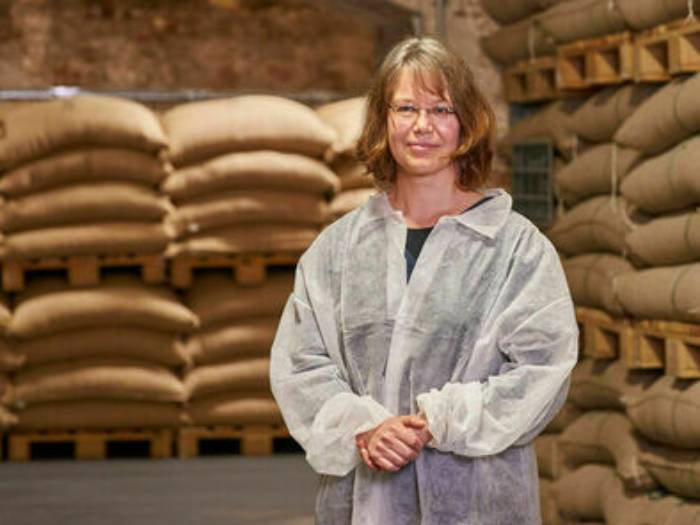
“We’re looking at various materials that will enable us to increase the organic percentage of imitation leather in the short term. The obvious place to start is with the filling materials,” explains Martina Gottschling of Volkswagen Group Innovation, who is currently working on research into sustainable materials.
The most recent idea involves the use of coffee as a raw material for imitation leather. When coffee beans are roasted, what is known as the silverskin, which surrounds the coffee bean to start with, builds up as a by-product. Even in medium-sized roasting plants, multiple sacks full of this film are generated every day; it is usually burned or composted, with a small proportion being turned into fertiliser. As it has a high caffeine content, it is not suitable for animal feed, and it also cannot be used to produce biogas.
The raw material
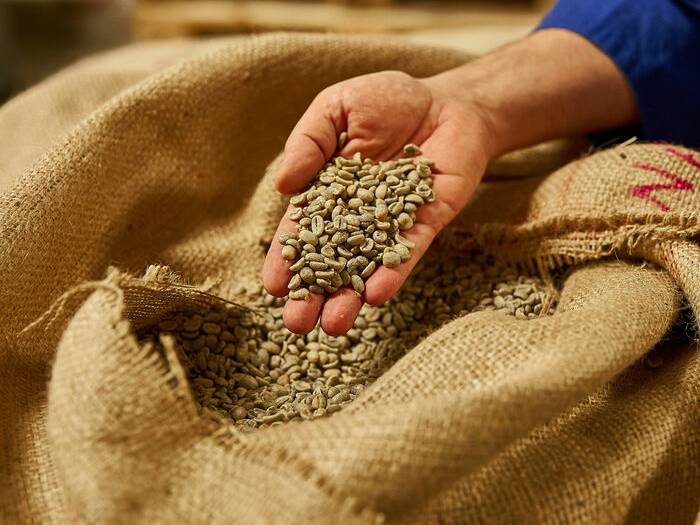
In Volkswagen’s case, the raw material – i.e. the silverskin – is provided by Braunschweig-based coffee roasting house Heimbs; founded in 1880, it has been producing in the northern Ringgebiet district, around 40 kilometres south of Autostadt in Wolfsburg, since 1954. The high-quality green coffee is stored in jute bags below the plant, in a vault with walls several metres thick which fortunately remained intact during the war. There is a slightly acidic, grassy smell in the air; the familiar coffee smell is a result of the roasting process.
Heimbs is the only German roasting house to use the patented aerotherm roasting method, which allows the flavour of the beans to be kept unaltered. Heimbs still roasts its coffee using the original machines from 1954, while other components such as the coolers were added in the late 80s.
Silverskin filler for imitation leather
Silverskin is an excellent option as a filler for imitation leather: “The substance is already dry, in an ideal form for further processing; a wet material would have to be dried first, using a lot of energy,” continues Gottschling. “What’s exciting is that it is a by-product, which currently has no further use.”
Volkswagen is currently testing whether the coffee imitation leather made with silverskin meets the stringent quality criteria that Volkswagen sets, as it needs to withstand heavy strain over many years, and maintain its optical and tactile qualities for the full lifetime of a vehicle. “In the tests so far, the durability of coffee leather seems to be comparable with tried and tested forms of imitation leather,” Gottschling tells, then explaining that the tested samples have a percentage of organic materials exceeding 50%, including the silverskin filler and the textile back, which is made from renewable raw materials.
Large-scale production
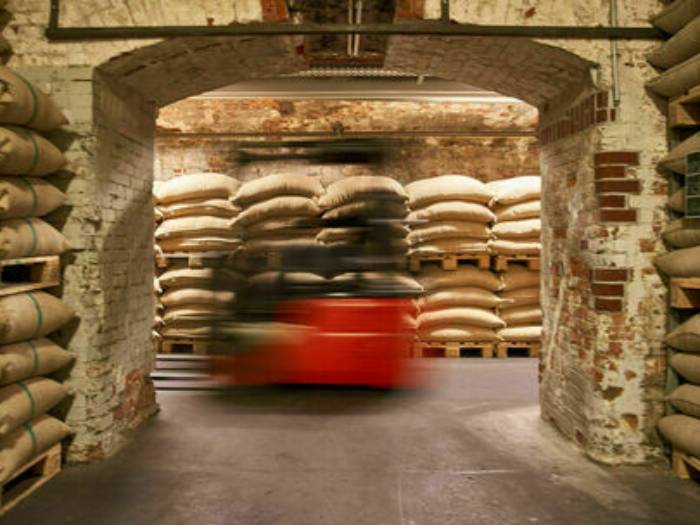
The artificial leather made with silverskin must be made available for use in large-scale production, with varying feel and surface grain. “There is huge potential and it could be one of the next steps in further optimising the ecological footprint of our ID. electric fleet,” Gottschling concludes.
And the supply of the raw material is not a problem, because the volume of silverskin required is not high, without counting on the stocks built up during the pandemic. For this reason, it could be found stretched over prototype car seats and armrests in as little as two years.
Source: Volkswagen - Shaping Mobility Hub
VGI | Responsible UO: VP | Creation date: article date | Class 9.1