Sustainability: Volkswagen’s commitment on raw materials
One of the biggest challenges that the Volkswagen Group is dealing with on its way to becoming the leading global supplier of electric vehicles is ensuring sustainable supply chains for battery raw materials. It is a matter that involves human rights, environmental protection and opportunities for developing countries.
While the European Union is planning to introduce strict regulations for supply chains, the Volkswagen Group has been developing sustainable relationships with all its suppliers for some time. Indeed, since 2019, all those in a direct business relationship with the company are required to undergo a sustainability rating procedure, which places criteria such as environmental and social standards on an equal footing with costs and quality.
“Direct suppliers are just the tip of the iceberg; the road to transparent supply chains is long and arduous. We are making good progress, but are not yet there,” explains Daniel Göhler, Head of Sustainability Strategy at Volkswagen Procurement. “When we are talking about battery raw materials such as cobalt, nickel, graphite and lithium, they can pass through long supply chains with as many as nine tiers. It is then difficult to keep track of which companies are involved and how the work is being performed locally.”
Transparency and sustainability
Since 2020, the Volkswagen Group has required full transparency all the way to the mine for battery raw materials. It is a continually expanding approach, which has now led to the introduction of a standardised raw material management system that not only covers the battery raw materials, but also minerals such as tantalum as well as other raw materials such as copper and leather.
This management system provides a solid basis for bringing transparency to the Group’s widespread supplier network of more than 65,000 business partner locations. “But requiring a company like Volkswagen to be aware of the conditions in which cobalt or lithium are mined is not enough. Companies also need to help improve living conditions in mining regions. A sustainable business cannot be built on child poverty or environmental pollution,” states Georg Kell, spokesman for the Volkswagen Group’s independent Sustainability Council.
Acting locally
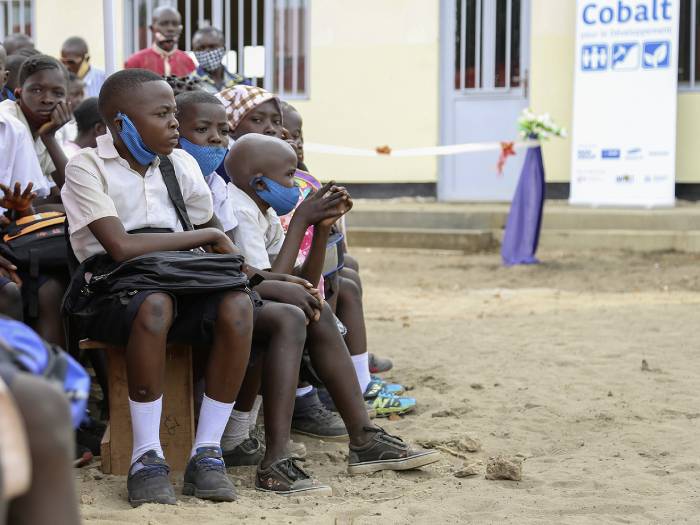
“The Cobalt for Development initiative in the Democratic Republic of the Congo, which the Group is participating in, is an excellent example, as it serves to inform miners about health and safety risks and to develop sustainable practices for mining cobalt,” Kell adds. This project also supports training opportunities and alternative means of earning a living, measures which are directly supported by the Sustainability Council. “The size of the Volkswagen Group makes it both capable and duty-bound to help in countries such as the DRC.”
According to Göhler, projects of this type must be planned on the ground, as was the case in the Congo, using a formula which could be replicated in Chile, where large quantities of lithium are being mined for batteries. “Last year, we went with a small team to the Atacama Desert on a fact-finding mission and to talk with the local Atacameños. The situation there is not easy. The next step will be to to build trust, to organise talks with different partners there and to find solutions to protect people’s livelihoods, especially those of the indigenous people,” Göhler concludes.
Artificial intelligence
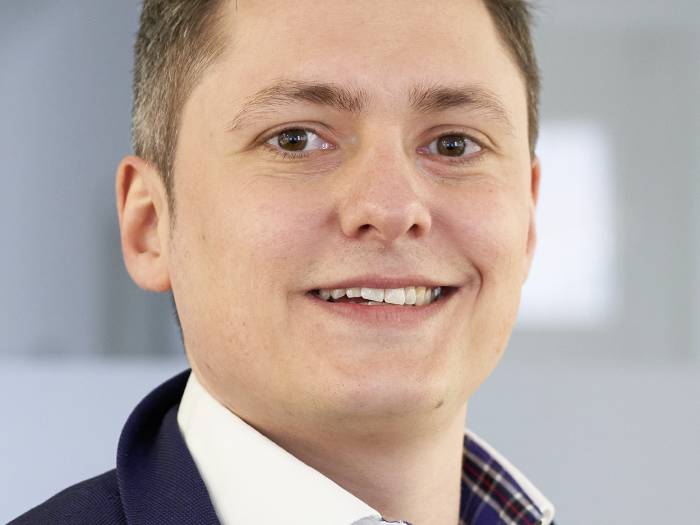
The Volkswagen Group categorically rejects child labour, and therefore insists on checks being performed within transparent supply chains: “This is precisely what we are working on with our direct suppliers, but we also conduct checks on our sub-suppliers using an independent service provider to track cobalt supply chains,” Göhler further explains. The Volkswagen Group is developing social and environmental standards for mines, which include occupational health and safety and a minimum workers’ age that mines must verify via access controls. Progress will be regularly reported on to give outsiders a picture of what is happening.
Further support in the transparency checks may also come from Big Data. “Artificial intelligence can be used, for example, to evaluate online postings in a specific language and receive daily status reports on impending violations of human rights and environmental standards. In other words, it can help establish effective early warning systems but is no substitute for taking real action on the ground,” Kell explains. More specifically, AI can help to filter out and prioritise the mass of information and provide specific priorities, comparing our analyses with information from our suppliers.
Supporting suppliers
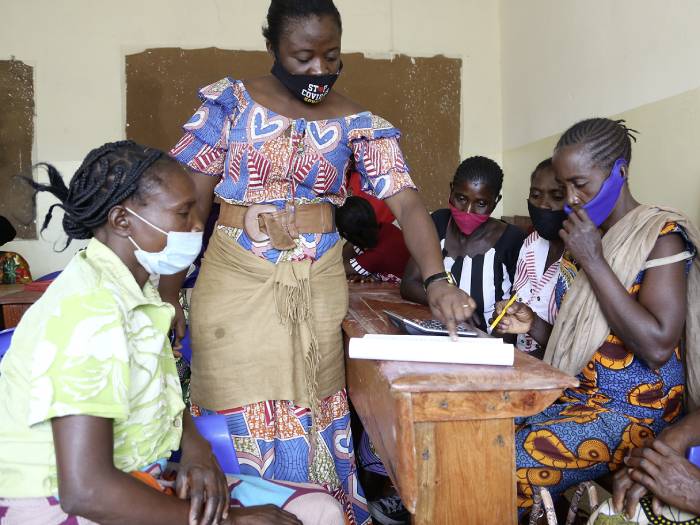
In 2020, the Volkswagen Group terminated seventeen contracts for sustainability violations and barred these suppliers from securing new contracts. Such sanctions are our most powerful weapon – but are a last resort; the Group’s goal is to improve conditions at suppliers without resorting to such extreme measures.
The best way to achieve the goal is to define clear timelines and responsibilities, because “Terminating a contract is the easy option – but doesn’t make things better. Extreme cases need to be sanctioned, but it is far more effective to address the problems with the suppliers. This applies to human rights, working conditions and environmental protection,” Kell explains, continuing to clarify how contracts need to be drawn up in such a way that it is in the companies’ own interest to make improvements in their operations so that social and environmental progress become mutually reinforcing.
The importance of recycling
“Mining has never been a clean business, we have to be realistic about this. But I still expect the Volkswagen Group to have ambitious goals: all supply chains must be transparent in five, ten years at the latest,” Kell concludes. It is also important to establish a circular economy: by recycling a lot of raw materials such as lithium, nickel or cobalt at the end of the battery’s life, this will drastically reduce the need for new raw materials. For this reason, Volkswagen has invested in its own battery recycling pilot plant in Salzgitter, where it will be possible to recycle up to 95% of the battery materials.
Managing raw materials
In January, the Volkswagen Group officially launched a new raw materials management system that will establish uniform sustainability standards for the mining and processing of sixteen particularly risky materials: lithium, cobalt, nickel and graphite, in addition to tin, tungsten, tantalum and gold, as well as aluminium, copper, leather, mica, platinum, steel, natural rubber and rare-earth elements. The goal is for increased transparency along the supply chains through the use of certified audits and the use of blockchain technology.
Pilot projects are also being planned to improve local living conditions in the mining regions. Group brands are taking responsibility for the supply chains of various raw materials and developing binding rules.
Source: Volkswagen AG