Range and fast charging: how to balance a battery
Range and fast charging times are two key aspects for the battery of any electric car. But the higher the energy density, the longer the time it takes to charge: how to achieve a good balance?
Every electric vehicle has to perform at its best in everyday use, and in this regard a great deal of attention is paid to two aspects: range on the one hand, and the charging performance of the lithium-ion battery on the other. To search for the best possible solutions, Audi develops and checks the cells and other battery components at its test center in Gaimersheim, Bavaria.
The charging status of each cell is indicated by three colors: black, red and gold. During charging, lithium ions are deposited in the graphite anode, and the graphite changes its color according to the charging status. When the cell is discharged, graphite looks black; when partially charged, it turns red; when fully charged, it changes color again to gold. "This allows us to see and assess the charging status", explains Bernhard Rieger, cell expert at the Audi Battery Testing Center in Gaimersheim.
Electrodes in lithium-ion batteries
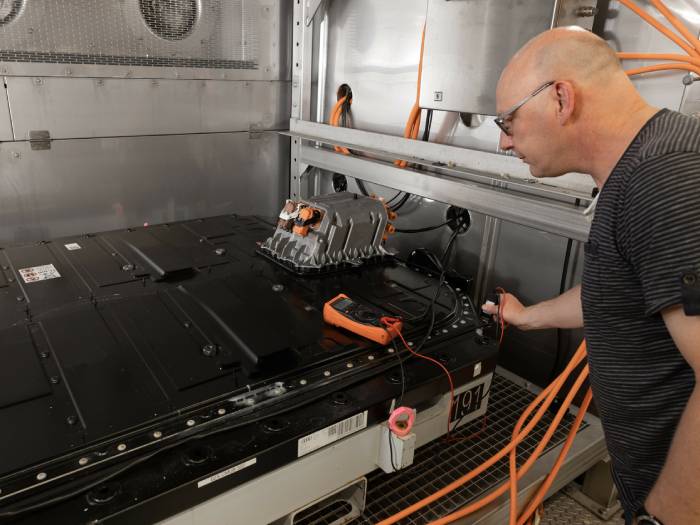
Electrodes do not charge uniformly; the charging rate increases or decreases depending on the number of lithium ions present. This results in a charging status gradient. Under ideal conditions, the entire electrode should have the same color, but this is only possible with extremely thin components that can store a minimal amount of energy.
"When it comes to fast charging lithium-ion cells, the most important aspect is extremely precise current control to avoid overcharging the anode in the golden areas, a situation that would lead to premature aging", Rieger specifies. "The goal is to ensure optimal operation of the lithium-ion cells to achieve the best possible range and charging performance. Once the basic need for range has been met, the focus shifts to charging capacity".
Range and charging speed: the art of compromise
In other words, engineers at the Audi test center in Gaimersheim have conflicting goals, as Rieger further explains: "We have a limited package available to us, into which we have to pack as much energy as possible, but we also want to be able to charge it as fast as possible". The contrast is that the greater the energy density, the longer it takes to charge the cell. The engineers' target, then, is to increase energy density while keeping charging times constant. The starting point is charging capacity.
To date, there are two Audi models setting standards for these specific aspects: Audi e-tron GT and Audi e-tron. The first has a 93 kWh battery that under ideal conditions can be recharged from 5 percent to 80 percent in just 22.5 minutes, with power outputs of up to 270 kW in DC. The latter, launched in 2019, is still considered the benchmark for its charging curve, characterized by a great speed in reaching the peak (150 kW in DC) and remarkable consistency in maintaining it.
Batteries: durability and safety
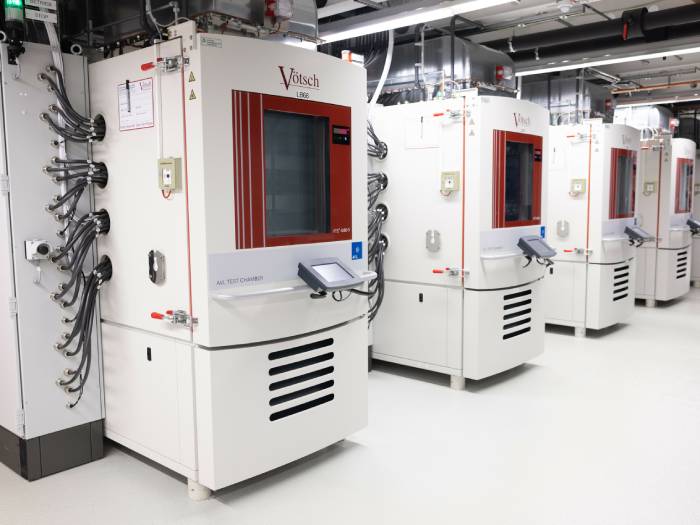
"We work to combine ultra-fast charging times with high levels of efficiency and long service life", says Rieger. At Gaimersheim, the entire battery system is put to the test, including electronics, thermal management system, and high-voltage peripheral components.
"Our systems are designed from day one with fast charging in mind, because it is very difficult to intervene later. Only a perfectly balanced battery pack in which every detail has been attended to from the first stage will achieve the desired charging properties". The battery cells must also meet the highest standards of durability and safety. With this in mind, both the cells and the battery system as a whole undergo numerous tests at the Gaimersheim facility.
The importance of battery testing
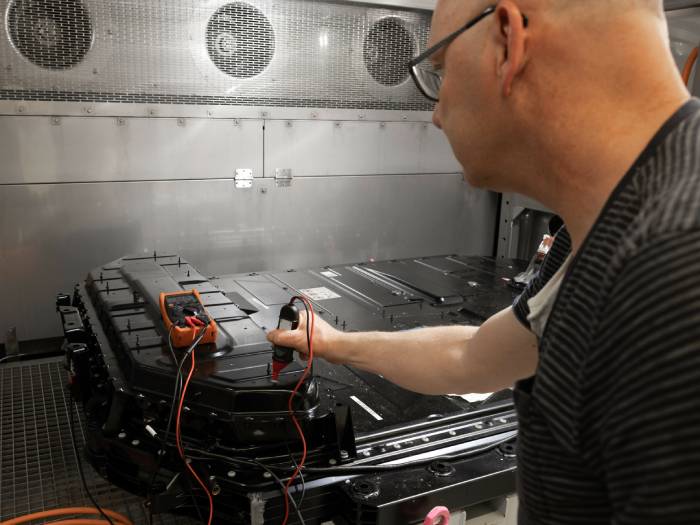
From the earliest stages of development, each electric vehicle goes through a long series of service life and fast charging tests carried out on hundreds of cells. These are tested with different charging profiles inside climate chambers that have temperatures ranging from -30 to 60 °C. "Our tests and checks begin about four years before production starts, to give us time to make readjustments where necessary", Rieger explains.
The cells are also exposed to high temperatures for the space of about a year in order to assess their aging and simulate an overall car life cycle of up to 15 years. Moreover, thanks to Gaimersheim's special test stands, scenarios equivalent to about 300,000 kilometers of driving can be reconstructed in a short time. These are supplemented by crash tests and overcharge tests, but different usage scenarios can also be simulated to optimize the high-volt components’ operating strategy or thermal management.
Optimal battery tuning
The result of all these procedures is the best possible fine-tuning of batteries for Audi cars. The work continues thereafter: the most up-to-date cell test results are sent directly to virtual battery models so that the effects on the vehicle can be observed.
Gaimersheim is also home to a construction facility for prototype batteries, starting from the ground up to pre-series production. "Here we have the necessary equipment to fine-tune the concept and cell operating strategy so that we get ideal properties for Audi's 100% electric cars", Rieger emphasizes.
Source: AUDI AG
VGI | Responsible OU: VP | Creation date: article date | Class 9.1