Audi: cutting-edge tests for the battery thermal management system
An effective thermal management is crucial for the ‘wellbeing’ of the battery in electric cars. At the Audi Development and Test Center in Gaimersheim, Bavaria, the most demanding climatic conditions are recreated to achieve maximum energy efficiency.
The high-voltage battery is the most important component of any electric car and to provide an adequate performance even under the most extreme conditions it must be warmed or cooled so that it always operates in the optimal temperature range. That's why the Audi e-tron has a thermal management system that prevents performance drops due to extreme heat or cold. However, in everyday operation, small temperature variations generally have little effect on system performance.
Complex circuits for thermal management
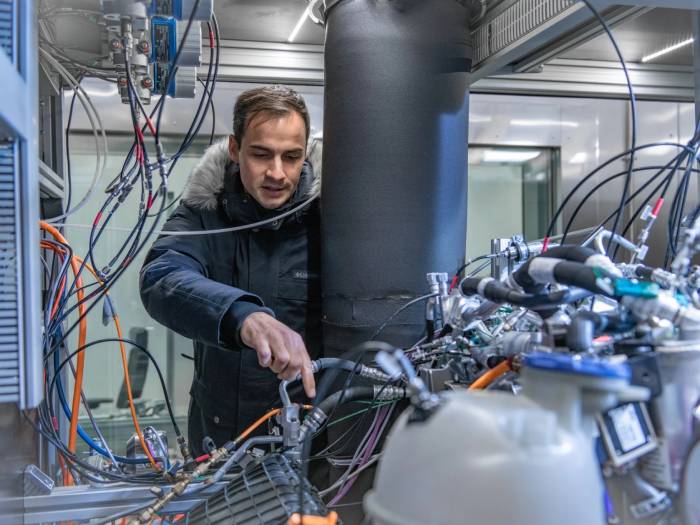
The thermal management in the Audi e-tron uses several coolant and refrigerant circuits. They are activated as required to cool or heat the interior, the powertrain or the battery. There are more than 200 interconnection options to achieve the desired temperature control.
Defining these options through real-life vehicle testing is time-consuming and expensive. The testing bay in Gaimersheim (near Ingolstadt, Bavaria), which is unique within the Volkswagen Group, was developed precisely for this purpose and allows these scenarios to be simulated at a very early stage of vehicle development.
Software simulations
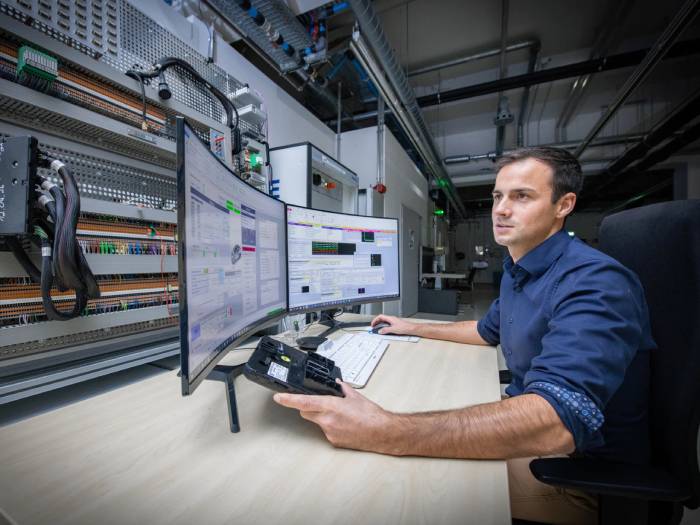
This testing bay has been operational since 2020 and can realistically simulate virtually all driving conditions, significantly simplifying the tuning of electric vehicles. It can recreate a wide variety of test scenarios that thermal management must cope with in order to validate its functions. Typically, the work involves testing possible future configurations based on around 120 project variants with an average of 100 test cases each. This requires the computing power of at least a dozen high-performance computers to verify the correct operation of the software in real time.
Semi-virtual car
All these tests are carried out with a car that could be described as semi-virtual, since everything that is important for thermal management, such as the control unit, the coolant and refrigerant circuits or the air inlets of the air conditioning system, are used in their correct position in a so-called 'test trolley'. In other words, the real assembled parts replace the real vehicle, after which the necessary outside temperature, humidity level and air flow are created. All these conditions are established from real routes, for example using data collected during a trip through Death Valley or at the Nürburgring.
Extreme heat: Death Valley
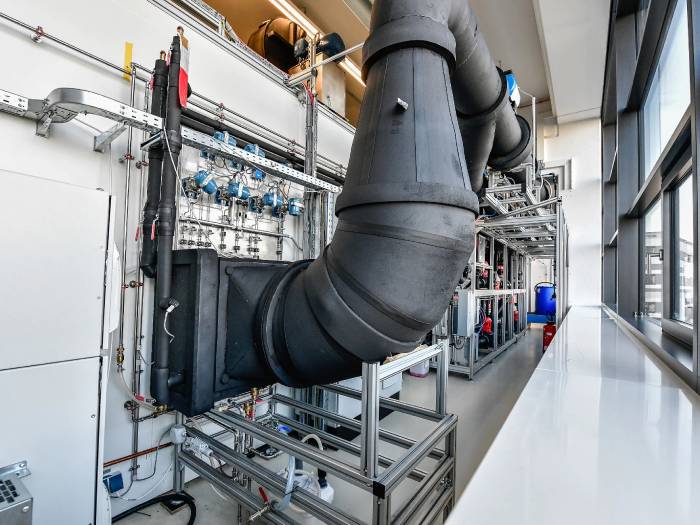
Death Valley is an area with very special conditions, with outside temperatures of up to 50 °C and very dry air. But the test bench also allows other values to be simulated, such as gradient, curve radii, average cornering speed, acceleration and braking. For example, the Audi e-tron can be tested while virtually driving a trailer, travelling at 60 km/h, using the airflow for cooling and overcoming gradients of up to 9%. During this simulation, the temperature variation in the vehicle is calculated and analyses are made of the operation of the different circuits: from the coolant to the air conditioning, not forgetting the control unit software.
Ice cold: the Alps
The procedure for simulating cold situations is the same. The Grossglockner High Alpine Road in Austria is a good example: here snow reaches 10 metres and sub-zero temperatures are the norm; the test conditions on the Bernina Pass in Switzerland are more dynamic. In total, more than 50 different tours are taken into consideration, with the addition of extraordinary situations, such as an outside temperature of -20 °C during a fast lap of the Nürburgring. After all the relevant preparations have been made, the tests start and proceed autonomously day and night - even seven days a week, if necessary.
Of course, classic road tests will also continue to be carried out, but thanks to these technologies, vehicles can be put to the test at a very early stage of development. And even once the vehicle has been built, it continues to be tested in the testing bay, as this is where measurements can be carried out more easily and quickly.
Source: AUDI AG
VGI | Responsible OU: VP | Creation date: article date | Class 9.1