Batteries for electric mobility: Volkswagen Group's gigafactories
Electric cars require specific components, such as battery cells. The Volkswagen Group has defined a strategy for in-house production that includes the construction of several gigafactories, which are needed to meet the ever-increasing demand for zero-emission cars, starting with the ID family.
5 gigafactories by 2030
The construction of a gigafactory is a major project that requires a great deal of effort and, above all, meticulous planning of all project phases. The Volkswagen Group is working on building five gigafactories by 2030, starting with the one in Salzgitter, Germany.
Despite the complexity of the operation, the German Group is relying on three pillars to keep to the announced schedule: a strong team, made up of the top experts in the battery industry; the right partners for the construction of the buildings and production facilities, and finally a high degree of standardisation for all plants.
“If we plan each plant individually, it would take a too long”, explains Sebastian Wolf, Director of Operations for Battery Cells at the Volkswagen Group and responsible for building the plants. "That's why we have gone for the concept of a standard factory, whilst at the same time remaining highly adaptable and flexible".
The advantages of standardised construction
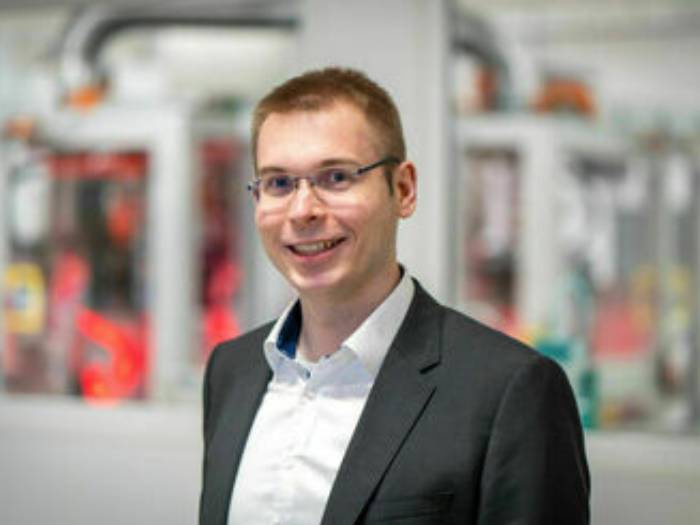
The standard design chosen by the Volkswagen Group for the gigafactories accelerates all phases, starting with the construction of the plants and ending with the equipment of the production lines.
With the exception of the approval stages, which differ from country to country, everything is the same - starting with the Group's unified cell, which will be manufactured in all locations. "An approach that will lead to high economies of scale and which, for customers, will have a positive effect on the price of the vehicle", continues Wolf.
Collaboration on battery cells
In cooperation with Bosch, the Volkswagen Group is looking into founding a European supplier for battery cell factories. This is linked to the opening of several European gigafactories in the next few years, including those of other brands, which will need to be able to rely on solid and competent partners. According to Wolf, "The Volkswagen Group and Bosch have the necessary know-how to set up large-scale, globally networked industrial production".
The Volkswagen Group's plans include cooperation with Umicore, a Belgian company specialising in battery materials technology. The partnership comes from the intention to counteract potential bottlenecks. The aim is to develop extensive production capacity for cathode materials with Umicore, which will also support the Group in the procurement of raw materials and recycling.
Two billion euros for the Salzgitter gigafactory
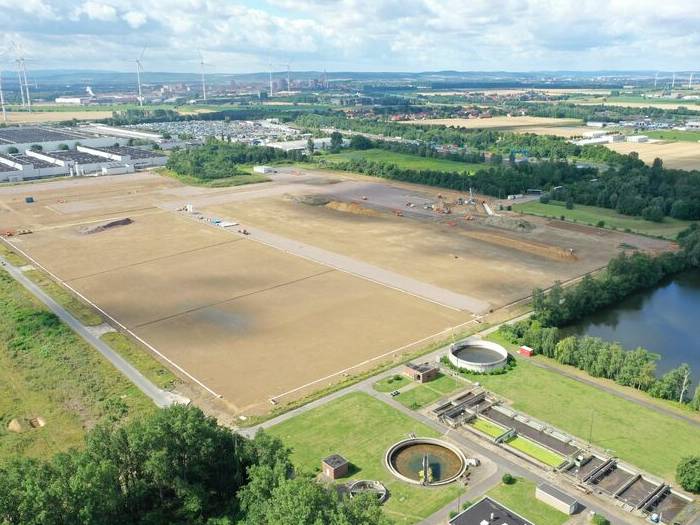
How much does a gigafactory cost? An investment of around EUR 2 billion is planned for setting-up and running the Salzgitter plant. "We are not the sole investors in the creation of the entire value chain in Europe, strong partners are also involved," explains Wolf. "That's why the Volkswagen Group is founding a European corporation to bring all activities together under one organisation: from the processing of raw materials, through the development of the unified cell, to the management of the gigafactories".
The levelling is almost completed in Salzgitter and construction is scheduled to start in the second half of the year. The first factory block is expected to become operational in spring 2025, followed roughly half a year later by the second block and then by the other sites, with the aim of achieving a total production capacity - taking all plants into account - of 240 GWh by 2030 at the latest.
How to decide where to build a gigafactory
If the Salzgitter gigafactory is already a given, the next ones could be built in Spain and Eastern Europe. Several factors must be considered when deciding where to build a gigafactory. In addition to suitable land and local contexts, two aspects are decisive: personnel and energy.
"To get a gigafactory up and running, we need to find enough qualified employees in the surrounding area. Not only chemists, but above all people with production experience. We also need a sufficient amount of energy from renewable sources, such as solar and wind farms", Wolf continues.
Modular Gigafactory
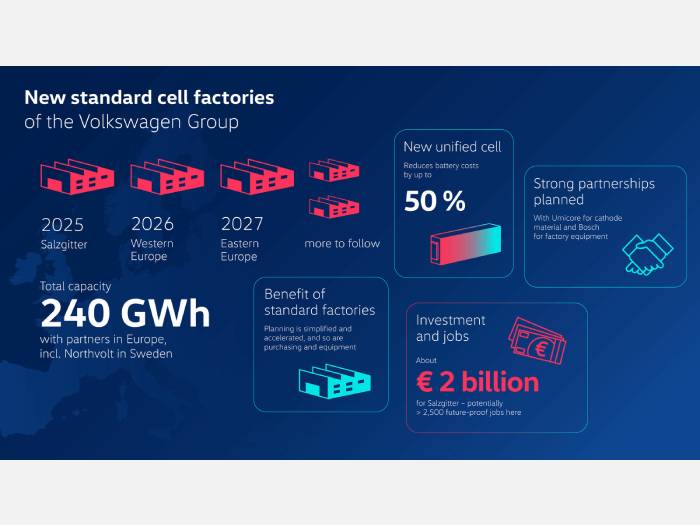
Electric mobility is constantly evolving. That's why the Volkswagen Group's gigafactories will be designed to evolve and meet the future needs of cell production, starting with the production of solid-state batteries and the use of dry coating of electrodes. A number of processes will change and some facilities will be replaced, but each gigafactory is designed to meet the needs of new models.
The partner Northvolt is also building a gigafactory in Skellefteå, Sweden. This plant will use renewable hydropower and supply cells to both Volkswagen Group brands and other manufacturers.
Working in the gigafactory
The production of cells in the Volkswagen Group's gigafactories will generate jobs, starting with more than 2,500 in Salzgitter alone. In total, the six plants will employ a five-figure number of people.
Most of the staff will come from within the Volkswagen Group, responding to the transformation process of the entire Group. "For example, there are many production professionals at the Salzgitter engine plant who could work in the new cell factory after attaining the necessary qualifications. The product may be different, but many of the manufacturing processes do not differ so greatly", Wolf points out.
The key role of gigafactories
Through in-house manufacturing, the Volkswagen Group is aiming for greater battery independence. This will also evolve according to customer demand: the faster e-mobility spreads, the faster the demand for battery cells will grow.
The quality of a battery cell is a central factor in an electric car, the key to charging speed and range. While today Asian manufacturers are leading the way in cell production, this may change in the coming years thanks to the value chain and know-how gathered in Europe. "Today we are chasing the best, but in the next few years we could become the industry leader thanks to the great work done", concludes Wolf.
Source: Volkswagen - Shaping Mobility Hub
VGI | Responsible OU: VP | Creation date: article date | Class 9.1