How an electric car is made: from batteries to final checks
ŠKODA has started the production of battery packs for the MEB platform at its Mladá Boleslav plant. But how do they become part of electric cars? Here all the processes and checks they must pass before they hit the road.
At the ŠKODA plant in Mladá Boleslav, the production of batteries that power the 100% electric ŠKODAs based on the MEB platform, namely the ENYAQ iV and ENYAQ COUPÉ iV, has begun.
The battery pack is produced in three different versions, which differ in the number of modules (8, 9 or 12) and thus in their total capacity. Batteries assembled at the Czech plant are used not only in ŠKODA electric SUVs, but also for other Volkswagen Group cars.
The right charge for electric mobility
"The battery passes all the necessary tests on the production line and then is charged to 14 kWh, which is 20-25% of the total capacity", explains David Bolcek, MEB battery assembly specialist. This level of charge is what is needed to go through all the necessary steps in the production process, including start up and the first test drive.
The battery leaves the production line already with all the necessary connectors to hook it up to the car. It is also already equipped with the underbody protection, which is a very strong metal plate that covers the lower part of the battery and is then connected to the vehicle chassis.
How is an electric car made?
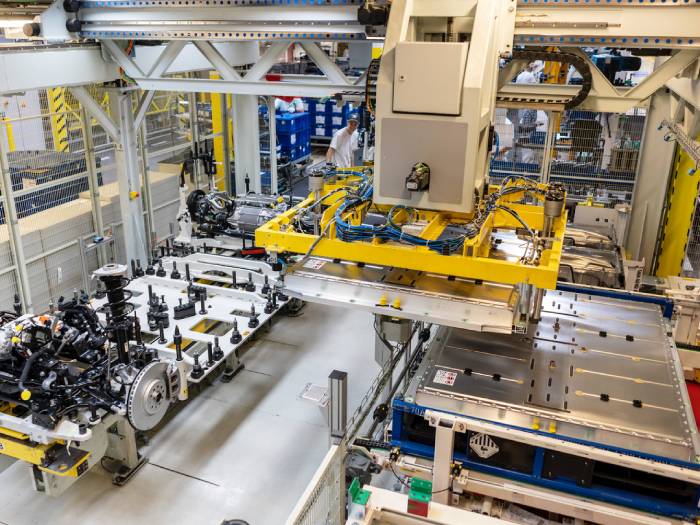
But what is the process that allows a 500 kg battery - that's the weight of the 12-module version - to become the heart of an electric car? When it arrives on the production line of a ŠKODA, it is taken over by a robot which places it on the chassis frame, then it proceeds down the line for subsequent assembly work.
At this stage, the connection of the battery with the other components takes place: "At first we connect the main cable, which connects the front and rear modules of the vehicle. Inside it are the brake lines, the communication harnesses of the vehicle's various systems, the cooling lines of the high-voltage components, and the orange high-voltage harnesses as well. We connect everything to form a functional unit", says Josef Mulka, battery specialist in ŠKODA's production management department.
The "wedding" between chassis and body
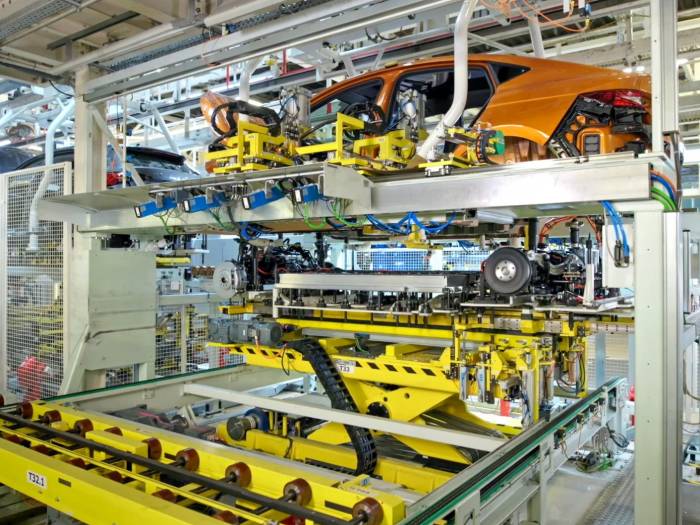
In the next step, the battery and some other components are connected to a socket so that later they can be charged.
At the end of this procedure, the chassis is finished and ready for the "wedding," a term used to refer to the connection between chassis and body. The battery is secured with 16 or 24 bolts--depending on the number of modules and, therefore, the size--around the perimeter, plus 4 more in the middle. The "marriage" is conducted entirely by a robot, which also bolts the front and rear axles to the body.
Safety checks on electric batteries
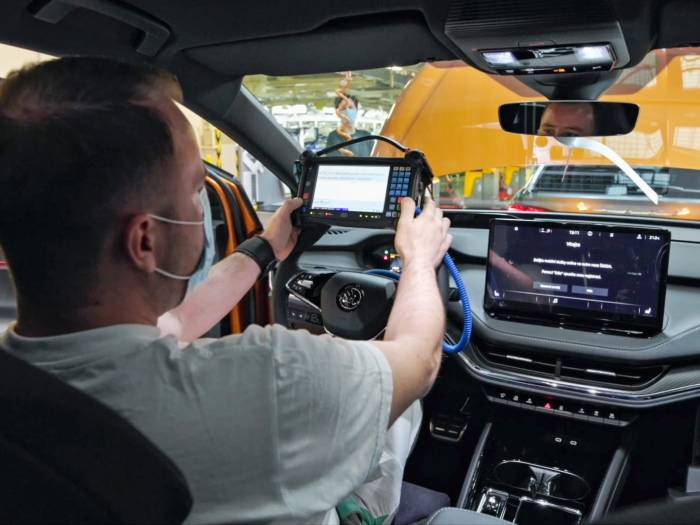
"Next we check the wiring of all components, at different stations on the production line", says Mulka. Then the car is turned on: "A technician uses an industrial computer, known as an MFT, to load software onto the vehicle's control units, including the battery. The computer verifies that the vehicle contains the right battery with the correct parameters, while the battery control software is loaded during its production", Mulka concludes.
When all important connections and parameters have also passed the next checks, the electric car can be started: first the service connector is turned on, then the battery ones. In this way the high-voltage grid is physically connected to the battery for the first time, the car starts and drives away for the final quality check - after which it is ready to be delivered to the customer.
Source: ŠKODA
VGI | Responsible OU: VP | Creation date: article date | Class 9.1