Un centro all’avanguardia per la produzione dei prototipi ŠKODA
Nonostante l'evoluzione delle tecnologie digitali e virtuali, i test tradizionali rimangono fondamentali nello sviluppo di un'auto. Per questo ŠKODA ha creato una nuova struttura dedicata alla produzione di veicoli di prova e prototipi all'interno del quartier generale di Mladá Boleslav.
Nel percorso che porta alla realizzazione di una nuova auto, la produzione di prototipi e di veicoli dedicati ai test, i cosiddetti muletti, è fondamentale. Per questo il reparto Sviluppo Tecnico di ŠKODA ha attivato un nuovo centro specializzato, dedicato proprio alla produzione di questi veicoli speciali.
La nuova struttura si trova all'interno dello stabilimento di Mladá Boleslav e utilizza tecnologie all'avanguardia, come stazioni robotiche e realtà virtuale, per tutto il processo di produzione.
Sviluppo e produzione
"L'utilizzo di muletti e prototipi ci permette di verificare molti parametri tecnici nella fase iniziale di sviluppo e di modificarli secondo le necessità, molto prima di arrivare alla produzione di serie" spiega Johannes Neft, Membro del Consiglio di Amministrazione ŠKODA per lo Sviluppo Tecnico.
Grazie alle risorse del nuovo centro, si potranno costruire in un’unica struttura fino a 300 veicoli di test e 120 prototipi ogni anno: "Qui abbiamo creato le condizioni ideali per sviluppare auto con la massima qualità, definendo la strada per il futuro del nostro marchio" conclude Neft.
L'importanza dei test
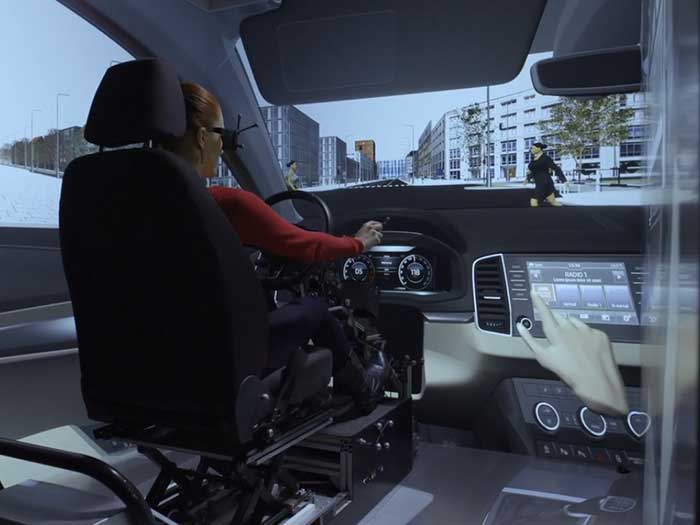
Anche se le simulazioni digitali e i modelli in scala sono sempre più importanti nella fasi di sviluppo, i test tradizionali restano essenziali, per monitorare non solo i singoli componenti, ma anche il veicolo nel suo insieme.
Inoltre, visto che le architetture elettroniche delle auto diventano sempre più complesse e potenti, è necessario porre una grande attenzione ai test funzionali che riguardano i sistemi elettrici, elettronici e di assistenza, senza dimenticare la comunicazione tra i tanti computer di bordo. Nel nuovo centro test, per esempio, sono già stati prodotti alcuni veicoli di prova del nuovo SUV ENYAQ iV 100% elettrico.
Una struttura all'avanguardia
“La nostra nuova struttura si sviluppa su tre piani e ospita il magazzino dei componenti, la carrozzeria, l'assemblaggio finale e l’area verniciatura. Tutti i reparti sono vicini, mentre l'alto tasso di automazione permette di avere processi agili e un'alta capacità di produrre prototipi e veicoli per i test" aggiunge David Vaněk, Responsabile della Produzione di Modelli e Prototipi. Nel nuovo centro ci sono 168 postazioni di lavoro in uffici open-space e 13 sale riunioni. Il complesso in totale misura 14.000 m² e la gran parte è utilizzata per la produzione dei veicoli.
Tre piani di efficienza
Al piano terra c'è il magazzino ricambi, direttamente collegato con un piazzale coperto dove i camion possono scaricare il materiale. Al secondo piano vengono costruite le carrozzerie, al terzo si eseguono l'assemblaggio finale e la verniciatura. Per trasportare componenti e veicoli da un piano all'altro c'è un montacarichi. Grazie alla presenza di due stazioni robotizzate, nel reparto carrozzeria l'automazione è cresciuta dal 15% al 45% ciò significa che la capacità di produzione è raddoppiata, passando da 5 a 10 carrozzerie a settimana, utilizzando il 20% di spazio in meno.
Nel nuovo centro si utilizzano tecnologie all'avanguardia per contenere il peso dei veicoli; un’innovativa stazione all’interno del reparto carrozzeria è dedicata alla sperimentazione di tecniche di giunzione evolute come la clinciatura, la rivettatura, il fissaggio flow-drill, la saldatura laser e i materiali compositi.
Realtà virtuale e controllo qualità
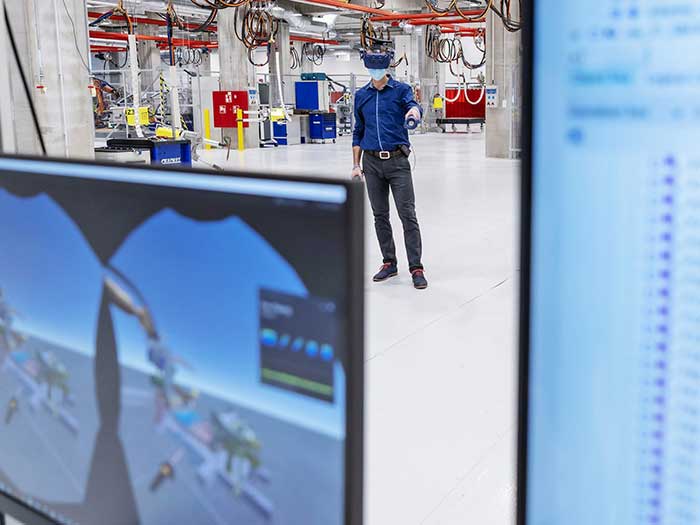
L'utilizzo della realtà virtuale permette di preconfigurare e personalizzare le postazioni di lavoro e, nella logistica, di utilizzare sistemi IT all'avanguardia. Nel processo produttivo è integrato anche il controllo qualità, che viene eseguito parallelamente alle rispettive fasi di produzione; tra le varie stazioni di controllo ce n'è una dotata di un banco prova che può simulare velocità fino a 300 km/h.
Il nuovo centro è allo stato dell'arte anche dal punto di vista ecologico: la riduzione delle distanze tra i reparti permette di risparmiare 1.800 litri di carburante ogni anno, riducendo le emissioni di CO2 di circa 5 tonnellate all'anno. Anche la totale integrazione del magazzino nell’area dedicata alla produzione di veicoli si traduce in ulteriori risparmi, riducendo i costi logistici di oltre 150.000 Euro all'anno.
Fonte: ŠKODA