Efficient batteries and MEB: key elements for e-mobility
Batteries are at the heart of electric cars and, together with the MEB platform, they play an important role in boosting the spread of electric mobility. Frank Blome, who heads the Battery Cell business unit at Volkswagen Group Components, tells us why.
Batteries are the key element in zero emission vehicles – their capacity and efficiency determine an electric car’s features. The aim of reaching the highest battery efficiency levels is precisely what prompted Volkswagen Group to develop a modular platform specifically for electric vehicles. Models from different brands and segments will be built on the MEB (from the German Modulare E-Antriebs-Baukasten).
The design process began with the battery, with the vehicle structure developed around it. This means there is much more space for the energy storage device, and it is better utilised, than previously. The result? In the case of the Volkswagen ID.31, a range of between 330 and 550 kilometres at affordable prices. Thanks to the MEB’s modular design, it is possible to configure cars with batteries of different capacities and varying sizes to give customers the opportunity to choose the most suitable model for them, according to their driving habits.
The MEB platform
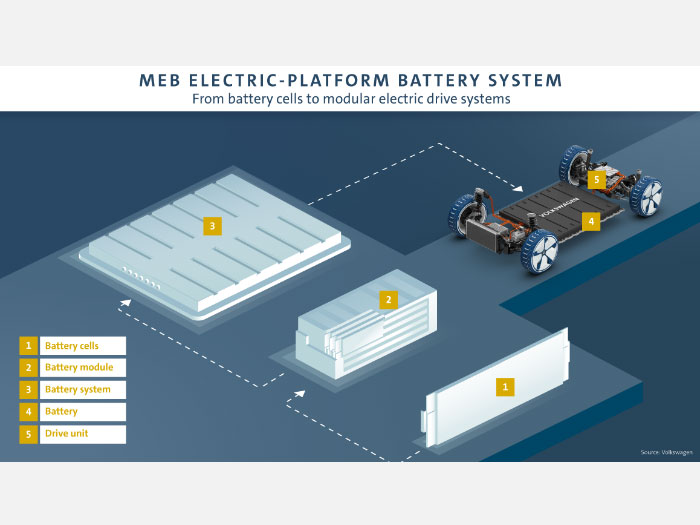
Its versatility is undoubtedly one of the strengths of the MEB platform: its architecture means a different number of storage modules – each of which contains a certain amount of cells – can be housed in the same underbody of the vehicle. This standardisation makes it possible to produce battery systems very efficiently and flexibly. The batteries’ life cycle should match that of the car in which they are installed. Volkswagen guarantees a minimum battery capacity of 70% over eight years, or 160,000 kilometres.
However, just like smartphones, user behaviour can also influence the battery’s durability. In this regard, there are two factors that can help extend the battery’s service life. Firstly, normal charging, which is ‘gentler’ than quick charging, and secondly, charging the battery to only 80% instead of 100%, which in most everyday situations is quite sufficient.
The life cycle of batteries
“Volkswagen assumes full responsibility for the entire life cycle, from the raw materials that batteries are made from, to their production and recycling. Batteries are not hazardous waste, but a valuable source of raw materials,” explains Frank Blome, head of the Battery Cell business unit at Volkswagen Group Components.
The aim is to achieve the highest possible level of recycling and reuse of valuable E-raw-materials such as nickel, manganese, cobalt as well as copper, steel and aluminium – all in an ecologically and economically sustainable manner. At the end of its life cycle, the battery is tested and reused in new products such as quick charging stations, or else recycled.
Raw materials
“We are working on a recycling concept to return raw materials to the manufacturing process chain. A pilot recycling plant is currently being built at the Salzgitter site, where recycling processes are being validated and scaled up,” adds Blome.
The pilot recycling plant is initially designed for up to 1,200 tons of batteries per year, corresponding to around 3,000 electric vehicles. However, larger quantities of battery returns are not expected until 2030.
Next steps
Volkswagen Group is working on a whole series of further improvements to batteries in terms of cost, range, and charging times. The aim is to significantly reduce charging times and increase the energy content of cells by using silicon anodes. The next big leap is likely to be achieved with solid-state batteries. Together with partner QuantumScape, the Group is working intensively to bring them to market maturity.
Another project to mention is the joint venture with Northvolt to begin producing lithium-ion batteries directly in a dedicated factory with an annual capacity of 16 gigawatt hours, which could see a further increase to 24 gigawatt hours. The Centre of Excellence, a key facility for battery technology within Volkswagen Group, is already operating in Salzgitter with around 300 experts developing innovative production processes.
1 vehicle not yet for sale
Source: Volkswagen AG