A pilot line for the production of battery cells in Germany
The line is running at the Salzgitter Centre of Excellence, the Volkswagen Group’s facility for battery research.
Batteries are undoubtedly the key component in electric cars. They account for around 40 percent of the added value of e-vehicles - this is why the Volkswagen Group has established a specific R&D centre. Alongside Group Research (the Group’s R&D division), the Centre of Excellence (CoE) plays a key role in the company’s battery strategy and is responsible for the development, procurement and quality assurance of all battery cells used in its vehicles.
In the last few weeks, a pilot line for the production of small batches of battery cells went into operation. The goal is to combine development, testing and production in a single site, in order to optimise processes and resources and be ever-more competitive both on the technical level and in terms of costs.
The pilot line and battery recycling
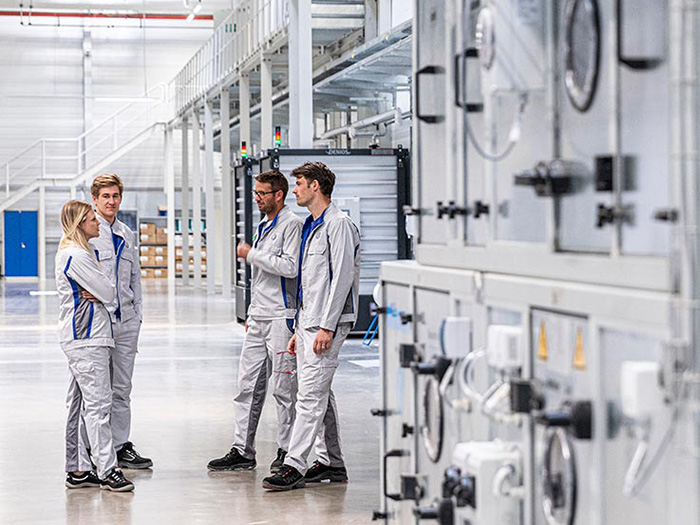
The Centre of Excellence is located in Salzgitter, in a strategic area including other Group sites dedicated to the electric mobility, such as Emden, Hanover and Zwickau – where production of the Volkswagen ID.31 will shortly begin – with significant advantages from a logistics perspective.
Around 300 experts work in the facility, in the fields of electrochemistry and cell research, as well as in traditional areas such as quality management, design and procurement.
The activities on the pilot line aim to define the processes and the expertise necessary for series production of the battery cells, in a relatively short time, and are not aimed at direct production.
In 2020 a pilot battery recycling plant will be built in Salzgitter, with the aim of recycling lithium-ion batteries at low costs, low CO2 emissions and with high reuse of resources. In this way, it will be possible to consider the E-raw materials – nickel, manganese, cobalt, copper, steel and aluminium –both ecologically and economically sustainable.
As early as 2020, it will be possible to recycle 1,200 tonnes of these materials per year with the pilot recycling plant - equivalent of around 3,000 vehicle batteries, with volumes increasing in subsequent years. The topic of recycling will take on ever-greater relevance in around ten years, when there will be a considerable quantity of electric vehicles reaching the end of their life cycle.
Supply chain sustainability
In battery cells production, raw materials are an essential but in some cases critical factor. The Volkswagen Group, which is committed to sustainability and social responsibility, monitors the entire supply chain, starting from the extraction of the minerals, and paying particular attention to working conditions.
Respecting human rights is an essential requirement, and all suppliers must comply with the standards laid out by the Group and monitor the activities of any subcontractors, otherwise they lose their contract. A concrete example is of the supply of cobalt: the company purchases this raw material only from industrial suppliers, at the same time working to constantly reduce the quantity of cobalt used in its batteries.
Manufacturing batteries in Europe
With a view to the future, the Volkswagen Group has approved investments totalling one billion Euros for the construction of a 16 GWh plant dedicated to battery production, with its joint venture partner Northvolt. Currently, batteries for the electric cars are imported from Asia. Europe has a production capacity of just 20 GWh in total, so there is a huge development potential: if electric mobility continues to grow as expected, it will be essential to manufacture the battery cells near the sites where the vehicles are produced.
The choice of the locations for battery production in Europe must take into account factors such as wage costs, taxation, the price – and above all the source – of energy, since the use of renewable energy (particularly in the production phase) is essential to achieving really sustainable electric mobility.
A global investment
The Volkswagen Group has planned huge investments in e-mobility (around 30 billion Euros by 2023), and manufacturing the battery cells internally will be essential in offering the best electric vehicles possible at competitive prices.
Around 70 new models will be introduced by 2028, based on the different electric vehicle platforms developed by the Group, and in particular on the MEB platform, whose characteristics could lead to it becoming the reference standard for the entire sector.
A look at the future of batteries
Lithium-ion batteries are currently the best technology available on the market and will remain so for at least the next ten years. Their energy density has doubled since 2014, and this translates into significantly greater ranges. Also considering the further potential technological developments in this field, the Group has decided to invest in its own production.
The next big jump will probably be the solid-state battery, which will have even greater energy density and thus greater ranges. They will also be lighter, cheaper and will allow shorter charging times. It will still be a few years before they are ready for use in industrial mass production, but the Volkswagen Group is conducting intensive research into this technology, together with its partner QuantumScape.
1 Vehicle not yet available for sale
Source: Volkswagen AG