Zwickau, a journey into the factory of the future
How a plant with over 100 years of history is being transformed to produce the Volkswagen ID.3, with a net zero carbon footprint.
Innovative cars deserve an innovative factory. This is why Volkswagen is converting its Zwickau plant from the production of cars with internal combustion engines into the largest and most efficient electric car factory in Europe.
It is the first complete conversion to electric mobility of a major automotive plant in the world: car production began in Zwickau over 100 years ago, and has involved a succession of iconic brands such as Horch, Audi, DKW and Trabant over the years. In the future, it will manufacture over 330,000 electric cars every year, more than in any other of the Group’s plants. Production of the compact Volkswagen ID.3, the first vehicle based on the innovative modular electric toolkit (MEB), will begin in late 2019. Other MEB plants are being built in Europe, China and North America.
A more intelligent, efficient and flexible factory
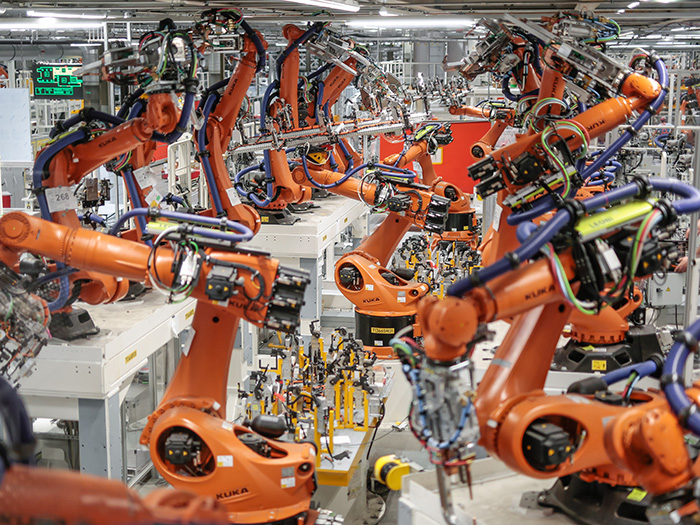
The Volkswagen ID.3 marks the beginning of a new era in production too. It will be more intelligent, efficient and flexible. In the future, six different models from three different brands will be rolling off the production lines at Zwickau: an unheard of level of flexibility. Volkswagen is also focusing on green, eco-compatible production. The ID.3s produced in Zwickau will have a net zero CO2 footprint.
Production of the ID.3, scheduled for late 2019, requires the modernisation or replacement of the bodywork, painting and assembly departments, as well as various infrastructure. The entire transport technology must also be prepared for the greater weight of electric cars.
The second production line will be converted in 2020 in the same manner. The Zwickau plant’s maximum production capacity, set to be reached in 2021, will increase by 10%, from the current 1,350 to 1,500 vehicles per day. It is estimated that the conversion will involve the processing of 9,000 metric tonnes of steel, with 50,000 square metres of industrial building to be fitted out anew.
Carbon neutral production
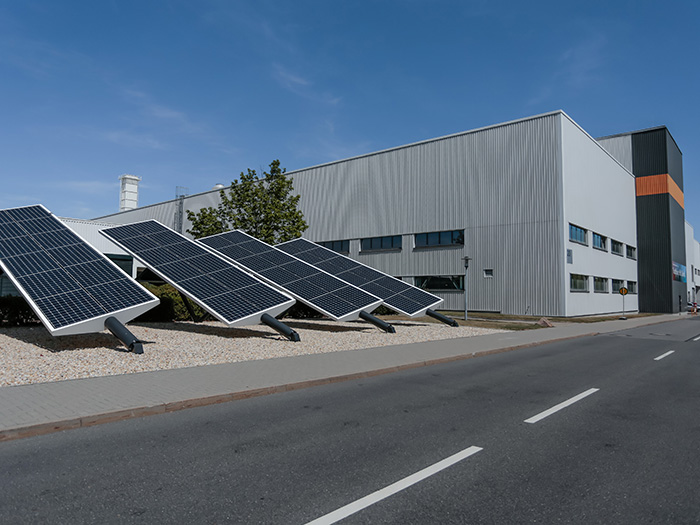
Electric vehicles offer a significant contribution to climate protection only if powered and manufactured with energy from renewable sources. In Zwickau’s conversion for the ID.3, Volkswagen has set itself the goal of delivering its customers vehicles produced with a net zero footprint in terms of CO2 emissions.
The plant has already been using green electricity produced by the hydroelectric plants of Austrian energy company Verbund since 2017. With the ID.3, the remaining emissions, deriving from high-efficiency internal heat and electricity generator, will be offset through climate protection projects certified according to officially recognised standards.
Humans and robots, together
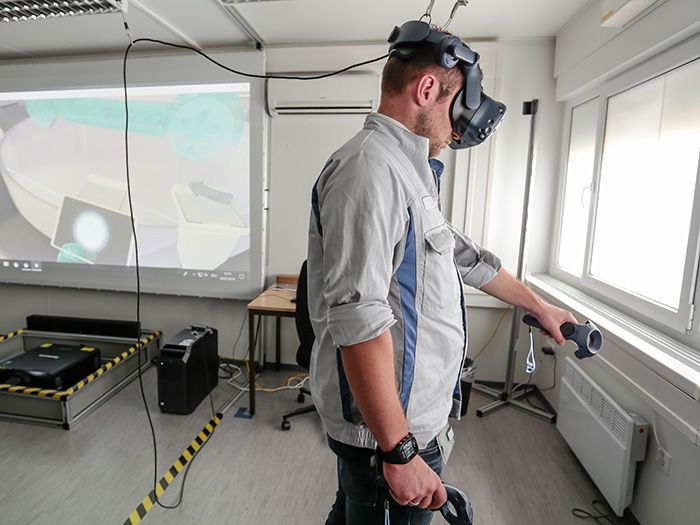
Zwickau’s conversion to electric mobility will progressively elevate its automation and efficiency to new and extremely modern standards, without any impact on employment levels. The goal is to create the factory of the future, an intelligent, ecocompatible production site which is fully connected and networked. At Zwickau, Volkswagen will be systematically introducing cutting-edge industry 4.0 robots, and expanding human-robot cooperation.
In the completely converted factory, production will be entrusted to a total of around 1,700 robots. The dashboard will, in the future, be installed in a completely automatic way, for instance. As well as shorter process times, automation also offers benefits for workers. Thanks to human-robot collaboration, workers will no longer be required to perform the most physically demanding and ergonomically unfavourable tasks.
Driverless transport systems (FTS) are another key technology for the factory of the future. They transport the necessary components to the line along predefined routes in a completely independent manner, thus revolutionising the factory’s workflow. At Zwickau, Volkswagen will be implementing this technology on an impressive scale: to date, over 500 FTS have been programmed.