Audi tests physical recycling for mixed plastic materials
Closed material cycles are a key part of the value chain in the automotive industry. That's why Audi is testing different processes for recycling plastics from end-of-life vehicles, including innovative physical recycling for mixed materials.
Sustainability is a top priority for Audi, which is why the Ingolstadt-based company is increasingly creating closed cycles for materials that enable efficient use of resources while increasing recycling rates.
The research involves partners from industry and science, including the Fraunhofer Institute, with which Audi is testing an innovative method to recycle plastics and make them usable for mass production. In addition, for the second year in a row the German company promoted Audi Environmental Week during which, through networking, exchange and interdisciplinary cooperation, all employees focused on recycling and developing new ideas to increase sustainability.
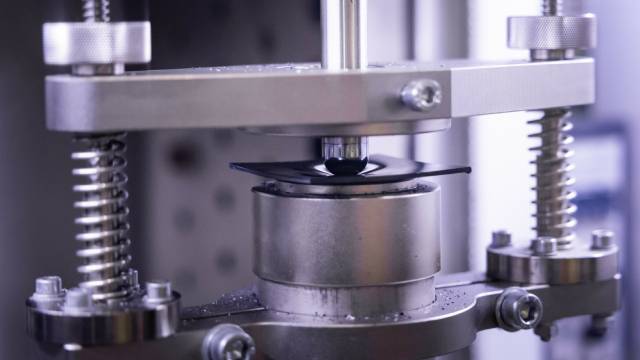
The benefits of closed cycles
Audi wants to make closed material cycles an integral part of the value chain in the automotive industry and is launching pilot reprocessing projects for a growing number of materials and components. The objective is to gain experience with as many processing techniques as possible and apply them in handling particular materials.
Closed material cycles have many advantages: on the one hand they limit the demand for raw materials, both renewable and nonrenewable, and on the other hand materials based on material cycles have a more favorable energy footprint. The energy requirements are also crucial when it comes to recycling, and only ecologically sustainable processes pass the pilot phase of projects. The ultimate goal of recycling processes is to increase the overall sustainability of the company.
Different types of plastics
In this specific case, not all types of plastic can be sorted and recycled in the same way and with the same results, which is precisely why Audi is experimenting with different technologies: mechanical, chemical and even physical recycling. Audi is working to identify and use as many types of alternative materials as possible, while identifying optimal processing and recycling techniques in order to create closed loops.
"Our focus is on getting as many plastic contents as possible out of the car at the end of its life, in order to be able to recycle them again", explains Mike Herbig, who works in Audi's polymer team. Today, a car contains more than 200 kilograms of various plastics and plastic composites: for example bumpers, radiator grills, various interior parts and the climate control system. The mixed plastics that are recovered are first mechanically crushed and separated from other materials, then can be processed into plastic granules ready for reuse.
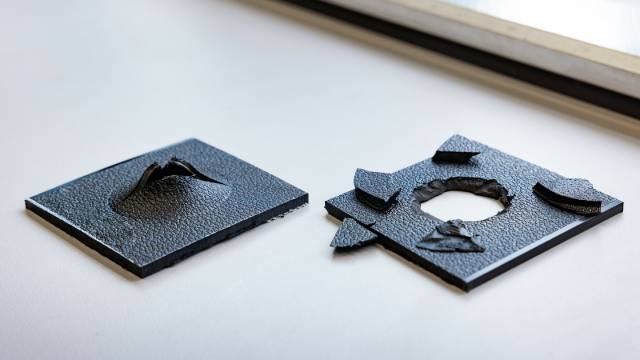
Quality without compromise
Plastics must meet high quality requirements, and the criteria do not change if the materials are recycled. The most important are crash safety, heat resistance, weather resistance, and resistance to fluids, including oils and solvents. Then there is dimensional stability and feel, appearance and smell throughout the car's service life. All this without forgetting environmental requirements: "We use a recycled material only if the resulting components also meet the requirements, that is, if their quality remains the same over their entire useful life", Herbig adds.
The limitations of mechanical recycling of plastics are evident with composites, where plastics are mixed with adhesives, coatings and fillers such as glass fibers. In addition, with each additional step of mechanical processing, the quality of the plastic progressively decreases. As a result, plastics that are recycled in this way are no longer suitable for use in vehicle construction, especially not for safety-related components.
Chemical and physical recycling of plastics
To overcome the problems of mechanical recycling, Audi also uses a chemical recycling method developed with the Karlsruhe Institute of Technology (KIT) and a number of industry partners: mixed plastic waste is processed into pyrolysis oil, which can replace crude oil as a raw material to produce high-quality plastics. In this case, the components are just as valuable and safe as when they are made from virgin material.
In parallel, Audi is also conducting another pilot project together with the Fraunhofer Institute for Process Engineering and Packaging IVV to investigate the possibilities of the physically recycling automotive plastics waste and its reuse in vehicles. This method makes it possible to deal with plastics with much higher levels of contamination, i.e., those generated primarily by incomplete pre-sorting of end-of-life vehicles.
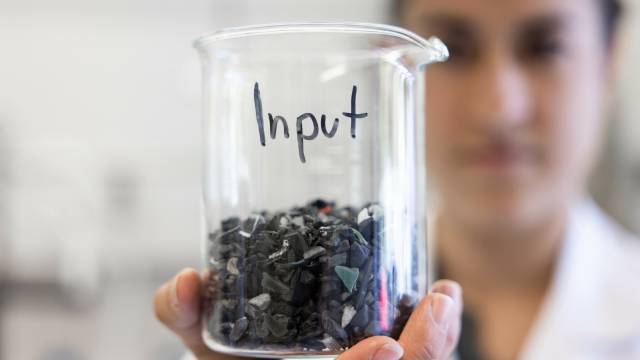
Solvents and granules
With physical recycling, the plastic is not transformed into a different subproduct, but dissolved with solvents, so there are no chemical degradation reactions and the polymer chains remain undamaged. "The solvents used are absolutely harmless substances, and solids that could interfere with the final result are separated," explains Martin Schlummer of the Fraunhofer Institute.
Substances such as flame retardants can be dissolved and separated from the plastic material, after which the solvents used evaporate and are fed back into the cycle. After drying, a very pure plastic granulate is obtained, that has the same qualities as the primary material. The ultimate goal is to produce increasing quantities of this granulate to test its technical feasibility and economic sustainability. The plastic recycled by this method will be processed into secondary parts, such as the seat height adjuster: a small component, but one with high standards in terms of strength and durability.
From the past to the future
In the future, Audi plans to integrate the various recycling technologies to recover as much plastic as possible from end-of-life vehicles and reuse it in new ones. In an Audi Q4 e-tron, for example, there are already as many as 27 components made with recycled materials, including large proportions of the headlight mounts, wheel arch liners, fender covers, floor trim, and wheel spoilers; all parts that have to meet particularly high demands in terms of mechanical properties.
There is also a lot of recycled plastic inside the Audi Q4 e-tron, in this case used for the insulation and damping materials, but also in many of the visible surfaces, such as the floor covering and parts of the luggage compartment trim. The sport seat upholstery on the S-line versions is made of artificial leather combined with Dinamica microfiber, which has the look and feel of suede, but is made of 45 percent polyester fibers derived from recycled PET bottles.
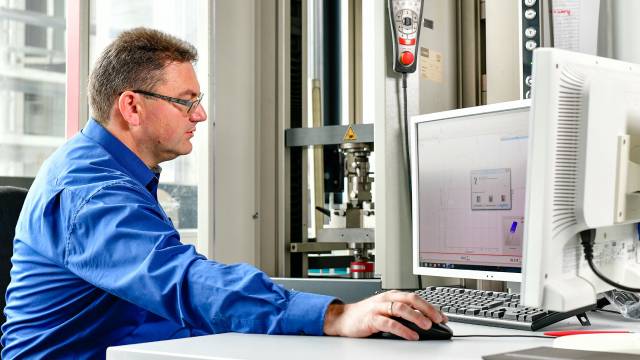
Audi Environmental Week
Audi hosted Environmental Week for the second time: an interactive format that promotes the transfer of knowledge and is intended to encourage people to challenge their own behavior. Audi Environmental Week featured more than 50 presentations made by employees for employees, panel discussions with experts on environmental protection, recycling, CO2 emissions reduction, nutrition and water conservation, as well as playful challenges and activities.
Source: AUDI AG
VGI | Responsible OU: VP | Creation date: article date | Class 9.1