From plastic bottles to car seats: the Audi circular economy
89% of the material used to make seat covers in the new Audi A3 comes from recycled plastic bottles - all thanks to an industrial process that helps promoting a sustainable circular economy.
A car contains around 340 kilograms of plastic, around half of which is already recyclable. One of the foundations Audi bases its innovation on is the use of sustainable materials. “We want to produce a durable seat cover with outstanding quality that passes all of our product tests — and we want to produce it sustainably”, explains Ute Grönheim, who works in the materials development department and is responsible for the seat covers in the new Audi A3; one seat cover is made out of 45 1.5L PET bottles.
From bottles to plastic yarn
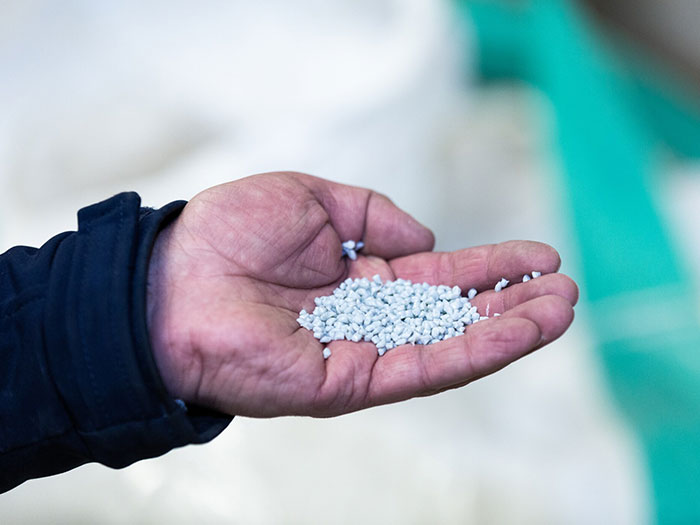
The process begins when used bottles are returned. They are washed before being shredded into little flakes that produce a granulate, which in turn is used to create polyester threads that will later become plastic yarn. “The granulate is essentially the same as that used for other seat covers, except this is made of recycled PET”, explains Grönheim.
Another difference is that the granulate is not as evenly milled and pure as the industrially produced granulate. “That can clog up the nozzles in the yarn production. Besides that, the opacity is irregular, so it is less absorbent and needs more dye”, says Grönheim. This means that recycled polyester threads are more difficult and more expensive to produce.
From plastic yarn to seat covers
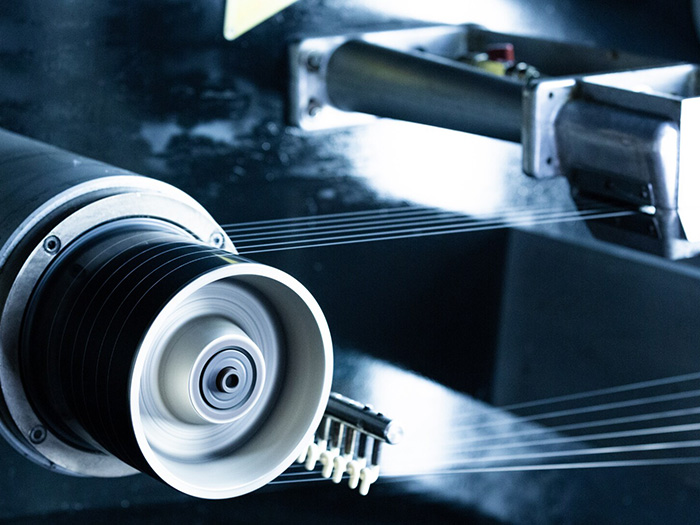
The plastic yarn arrives on spools that weigh around 2 kilograms; it is then processed and made into a fabric for seat covers. At this point, it makes no difference whether the yarn is recycled or artificially created. After it has been woven, the fabric already looks finished: it has a pattern and already feels like a seat cover. However, it is actually far from being the finished article.
The fabric first has to undergo a rigorous process of quality control. The most important stages in this process are carried out by specialists, beginning with a fabric mender who detects any excess thread and tests the fabric by hand to feel for any knots or hard areas. Any small defects are repaired immediately with needle, thread and scissors; the larger ones are marked. Each specialist checks around 200 meters of cloth per hour.
Laminating
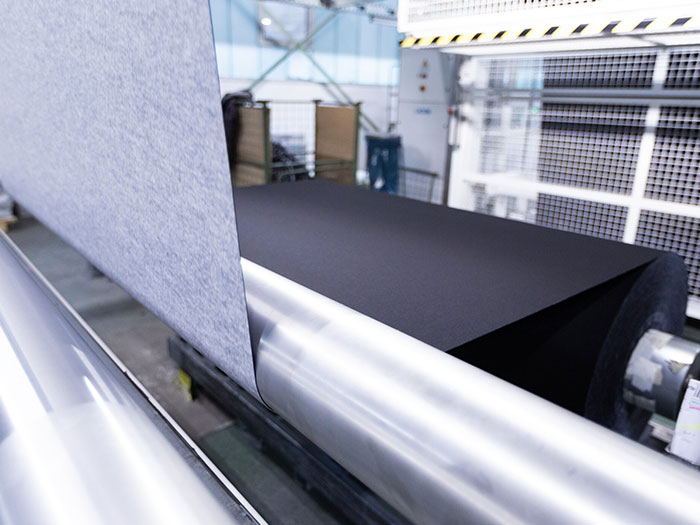
After the quality controls, the fabric is rolled up and cleaned on a 20-meter long washing system at 60 degrees Celsius. The system can manage around 30 meters of fabric per minute. The core holds around 600 meters of cloth, so a washing cycle roughly takes one hour. After it has been washed, the fabric is smoothed and dried. In the next step, a machine glues fleece to the cloth. This process is known as laminating and plays an important role in the seat’s comfort. “Right now we use flame lamination. In this process, an open flame is used to melt a thin layer of foam, which is then glued onto the fabric along with the fleece”, explains Britta Gebhardt, head of design. Taking the fleece into account, the car seat cover consists of up to 89% recycled plastic bottles. The goal for the future is to also use glue that is made of recycled materials, as well as the fleece.
Final checking
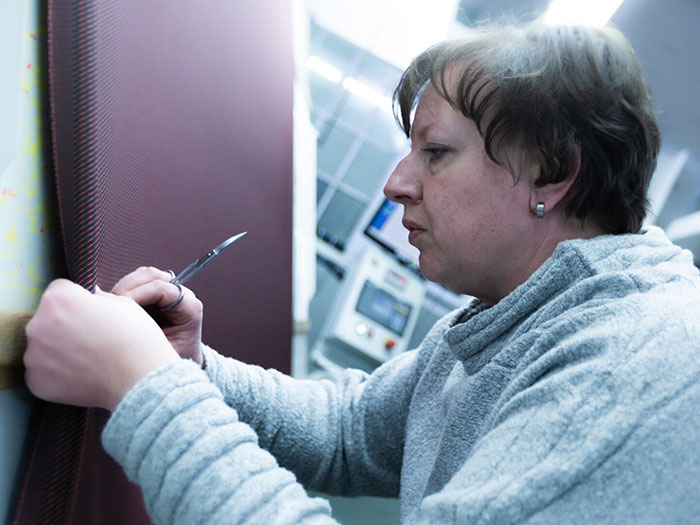
After a final quality inspection and a stress test, the seat covers for the new Audi A3 are sent to another factory. The sewing studio shapes the fabric and the upholstery workshop stretches it over the seats. “We have the chance to make great progress in sustainability over the next few years”, says Grönheim. “We want to produce the seat covers entirely from one type of material — 100 percent recycled PET”.
Source: AUDI AG