E-mobility, training and sustainability: transforming the Emden plant
The Volkswagen plant in Emden is undergoing the biggest transformation in its history: the conversion to the production of electric cars, supported by an investment of one billion euros. Unconventional methods are being used to train employees.
Climate neutrality as a goal
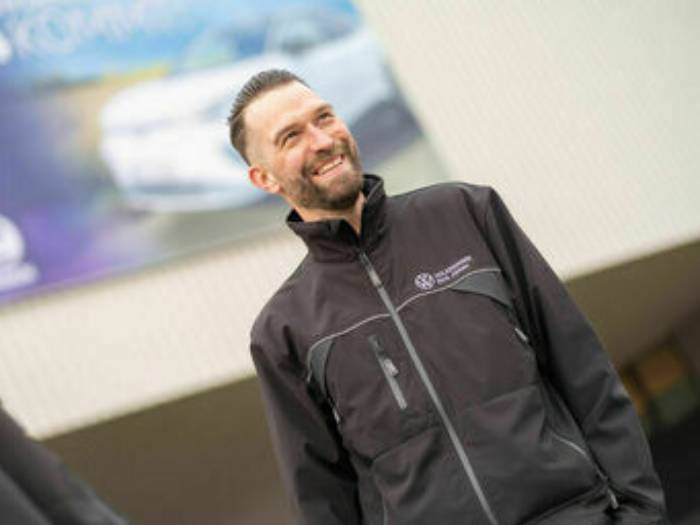
"The transformation and the switch to e-mobility are very important for Emden," explains Dirk Jibben, team spokesman at the Volkswagen Emden plant. Volkswagen is investing one billion euros in the developments and the goal is the environmentally friendly production of sustainable electric cars - an important step for the company on its Way to ZERO, the journey towards climate neutrality.
At the Emden plant, concrete projects have been initiated to achieve this goal, such as the use of ground-level geothermal energy through "energy piles", energy-efficient district heating powered by a biomass plant, the use of energy from renewable sources, photovoltaic panels on the roof and wind turbines in the factory premises. In addition, the "no plastics" initiative is helping to significantly reduce plastic waste in production: over 6 tonnes of plastic waste have been saved since last year.
Emden as a pilot project for electric mobility
The decarbonisation of the production process and supply chain is going hand in hand with the transition to e-mobility. Emden is one of the most modern factories in the automotive industry and a lighthouse project for the development of zero-emission mobility. Starting in the coming months, the Volkswagen ID.4 will be the first electric car to be produced at the plant. Next year the all-electric Aero B, a model with similar size to the Passat, will roll off the production line in saloon and estate versions.
60,000 training days for employees
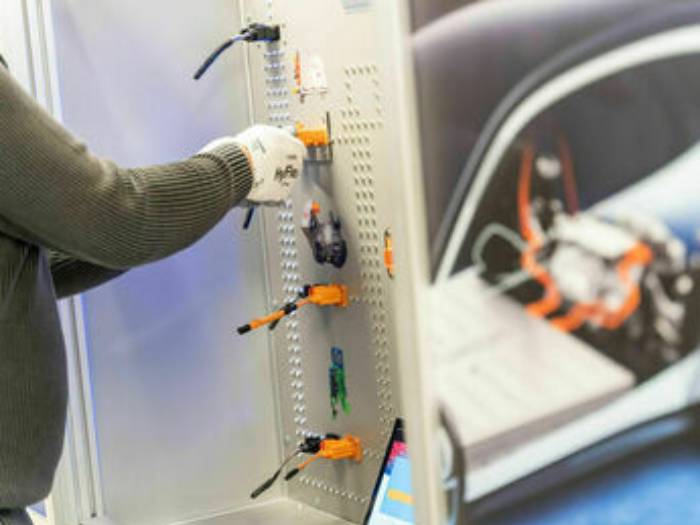
This is the largest workforce transformation process in the plant's history. By the time production starts, employees will have completed more than 60,000 days of training, beginning with increasing their knowledge of electromobility and ending with specific courses on the production of future zero-emission models.
To make this possible, several training stations have been set up, as well as a stationary production line where it is possible to learn the new movements needed to build an electric car. In particular, the handling of the parts and components of the electric drive is new for the production staff: "The whole wiring is different, but that is what makes an electric car", says Stephanie Lorenz, deputy supervisor, as she explains the new processes.
To make the training more effective, walls with differently coloured connectors have been set up, on which the trainer uses many gestures to explain the differences between the various components: she takes the right plug and inserts it into the connector, causing three green lights to illuminate to confirm that the operation is correct. However, training does not only cover the specific components and their use, but also all related activities.
Goodbye conference rooms
Training in the German facility also involves fun activities, such as those organised in 'escape rooms'. A team has to work together and discover clues, solve puzzles and complete tasks in order to achieve a goal within a given time. In Emden there are three rooms covering different topics. Participants learn a lot about electrification, as well as about the model and the history of Volkswagen.
"The escape room in the training centre is fun", says Lorenz. "First you have to get your bearings, but that's how you learn even more about the history of the company: how it all started and developed, the model we started with and where we are today". Dirk Jibben was immediately impressed by this non-conventional solution. "I was one of the first people to try the escape room. No one had told me anything in advance and when I walked in I was amazed. It was really cool".
The importance of teamwork
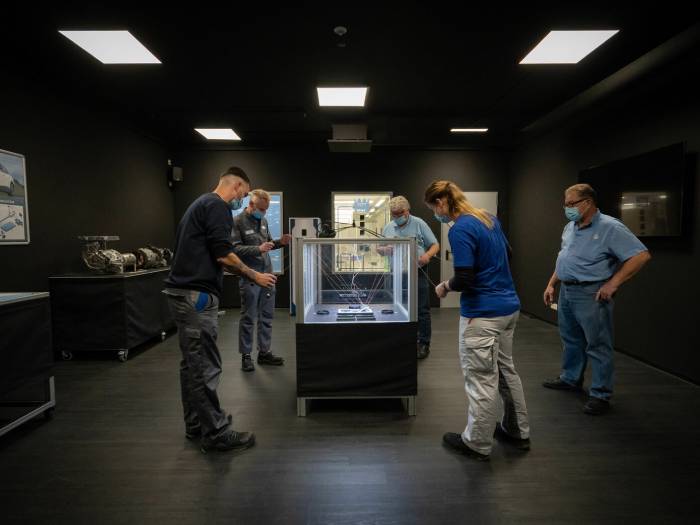
Team building is the key aspect: four people line up on opposite sides of a plexiglass box. Using wires, they hold and balance a magnet which, as a team, they must use to put together seven pieces of a puzzle. Patience, coordination and collaboration are the order of the day here. Jibben takes the lead and gives advice on who to pull or let go. After a brief moment of familiarisation, the team starts working in unison and successfully solves the task. "Using the escape room to demonstrate that you need to work together as a team to advance successfully is a really cool idea", comments Jibben.
The training programme, of course, is not limited to the escape room. One part is dedicated to the plant conversion, which started in November 2018 with the first projects have already been completed. The new assembly hall, which has been under construction since October 2020, is central to the future production of electric cars: it is the size of eight football pitches and is equipped with an efficient LED lighting system that emulates natural light. Thanks to modern transport technology, ergonomic workstations and fully automated production processes, the assembly hall is an example of visionary and sustainable automotive production.
Close cooperation with the Zwickau plant
"We come from the world of combustion engines and do not yet have expertise in the production of electric cars; in this plant we have produced hybrid models. That's why the interaction with Zwickau was and remains incredibly important," Jibben emphasises. The transfer of know-how from the Zwickau plant, the creative training facilities and the learning process in the production line are 'the basic framework' for the transformation in Emden.
Source: Volkswagen - Shaping Mobility Hub
VGI | Responsible OU: VP | Creation date: article date | Class 9.1