Audi, l'assemblaggio modulare per una produzione più flessibile ed efficiente
Con il sistema flessibile, che rinuncia al nastro trasportatore e al ritmo fisso, si semplifica la gestione delle varianti di prodotto nella produzione. La produttività incrementa del 20% e l'ambiente di lavoro si adatta anche a chi ha disabilità.
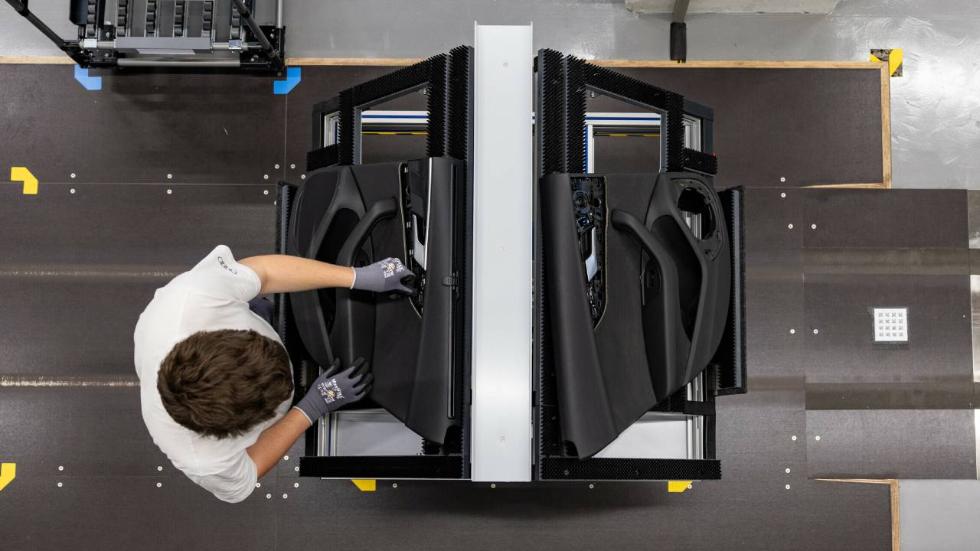
Nell'industria automobilistica il nastro trasportatore è stato al centro della produzione per più di un secolo, ma comincia ora a mostrare i propri limiti, perché i processi e i componenti nei sistemi di assemblaggio sono sempre più variabili e le possibilità di personalizzazione sempre più numerose. La produzione attuale comporta una complessità che è sempre più difficile da gestire in un processo rigido e sequenziale.
Per questo Audi ha introdotto il primo sistema di assemblaggio modulare nell'industria automotive, come nuova forma organizzativa supplementare: i tecnici assemblano i componenti in “isole di produzione” indipendenti dal ritmo del ciclo di assemblaggio, mentre i veicoli a guida automatizzata (AGV) forniscono alle stazioni i materiali necessari secondo il principio goods-to-person.
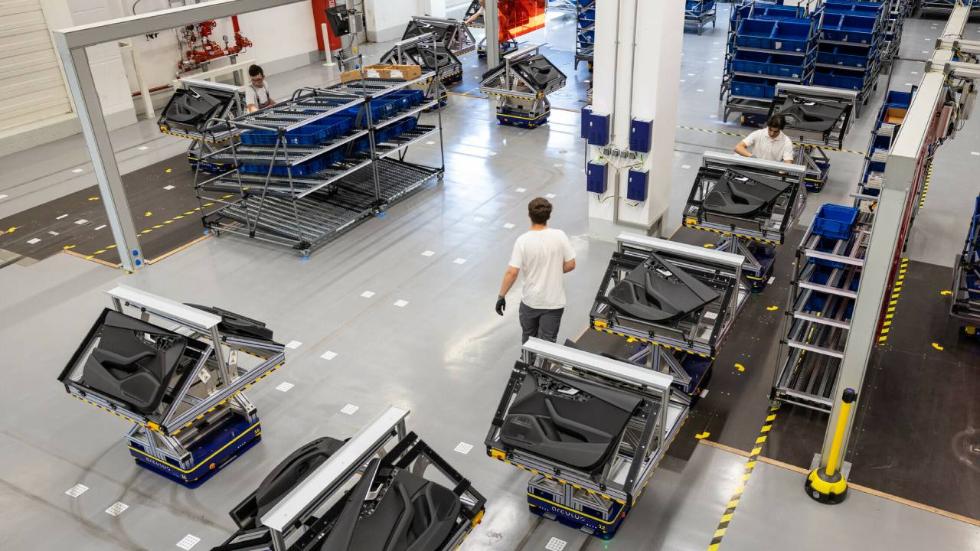
Procedure dinamiche
Il nastro trasportatore basava la sua efficienza su un ciclo di montaggio con un tempo uniforme per ogni prodotto e in ogni stazione, in una sequenza fissa. L'assemblaggio modulare, invece, funziona senza un ritmo di lavoro uniforme. Al posto di un nastro trasportatore rigido ci sono procedure dinamiche, con sequenze variabili di stazioni di assemblaggio e tempi di elaborazione determinati dalle varianti.
Il team dell’Audi Production Lab guidato dal Project Manager Wolfgang Kern sta implementando questo metodo a Ingolstadt, nel pre-assemblaggio dei pannelli porta, per poi estenderlo alla produzione in serie. "L'assemblaggio modulare è una delle nostre risposte alle future esigenze di produzione" spiega Gerd Walker, Membro del Consiglio di Amministrazione Audi con responsabilità per Produzione e Logistica.
Cultura dell'innovazione
"Utilizziamo la tecnologia digitale a vantaggio dei nostri collaboratori, ottenendo un assemblaggio più flessibile ed efficiente. Questo progetto è anche un ottimo esempio della nostra cultura dell'innovazione aperta, con cui stiamo sviluppando la produzione in rete in team agili" aggiunge Walker. Gli esperti, osservando i risultati del progetto pilota, confermano sia la fattibilità che il potenziale dell'assemblaggio modulare, creando allo stesso tempo competenze aggiuntive.
Uno dei vantaggi principali di questo sistema è che può coinvolgere persone che a causa delle loro limitazioni fisiche non possono invece lavorare sulla linea produttiva tradizionale: "Possiamo adattare l'ambiente di lavoro alle loro condizioni, cosa che con il nastro trasportatore si può fare solo in misura molto limitata. Nella produzione stiamo utilizzando un'automazione più flessibile per alleggerire il carico di lavoro delle persone" racconta Kern.
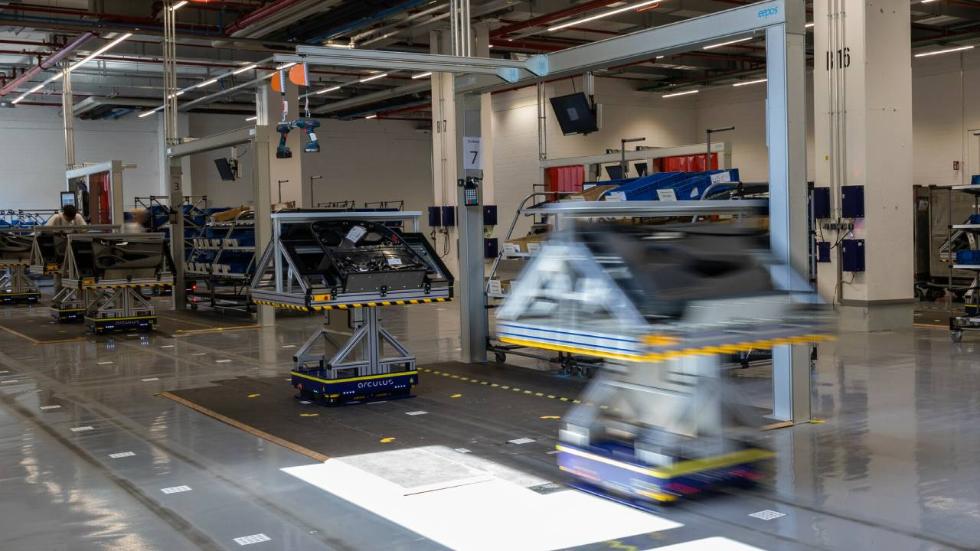
Spazio e tempo
Con questo metodo le attività non seguono più una sequenza uniforme, ma sono strutturate per soddisfare esigenze particolari. I veicoli a guida automatizzata (AGV) portano i pannelli delle porte direttamente nella stazione in cui devono essere assemblati. Se in una stazione vengono montati i vari kit di luci, i passaggi che non prevedono l'illuminazione vengono effettuati altrove e nel frattempo in un'altra stazione un tecnico monta le tendine parasole per le porte posteriori, che sono un optional e che sul nastro trasportatore avrebbe richiesto l'intervento di due o tre tecnici, con un calo dell'efficienza e della qualità. Ma se in una stazione si stanno accumulando troppe lavorazioni, gli AGV consegnano i componenti alla stazione successiva più libera.
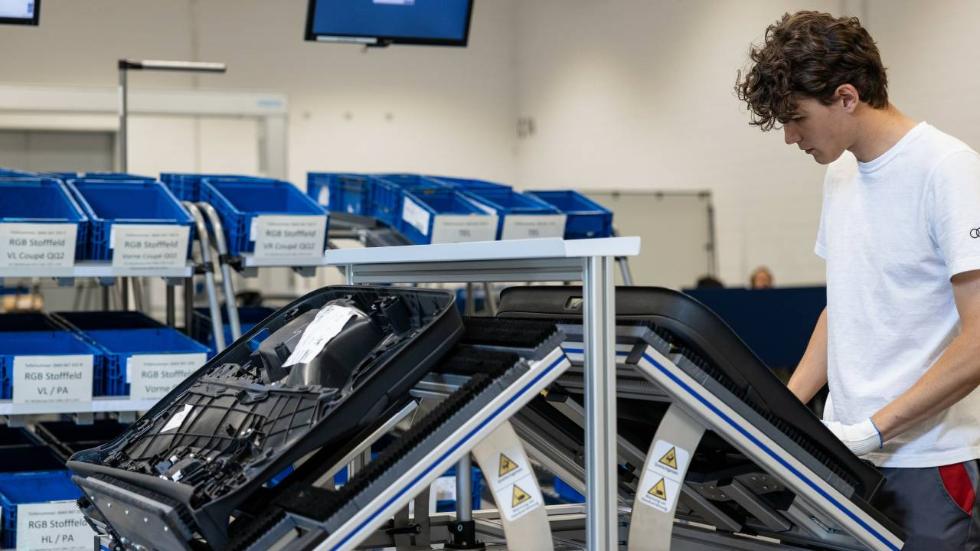
Goods-to-person
La configurazione degli spazi di lavoro viene verificata e adattata ciclicamente. "Rispetto al modo in cui le cose sono organizzate oggi, avere la flessibilità come logica di base è un progresso essenziale" riprende Kern. A differenza di un nastro trasportatore, le singole stazioni e il sistema di produzione modulare non sono progettati per una domanda stabile, ma assicurano la massima efficienza nelle situazioni variabili, per cui la soluzione migliore è il principio goods-to-person. Così gli AGV consegnano ai tecnici i cablaggi necessari per i pannelli porta, mentre le altre parti uguali tornano nella postazione di stand-by, perché di solito serve una versione diversa del componente per il pannello della porta successiva.
Questo metodo di utilizzo degli AGV rende superflua la separazione a monte, perché i veicoli sono localizzati al centimetro tramite una rete radio e guidati da un computer centrale. Inoltre, se necessario, si può integrare l'ispezione con una telecamera. In questo modo le irregolarità possono essere gestite più rapidamente e facilmente rispetto a un nastro trasportatore, evitando lavoro aggiuntivo imprevisto. “Stiamo mettendo insieme l'alto grado di divisione del lavoro del nastro trasportatore con un occhio olistico verso il lavoro agile e le nuove possibilità offerte dai sistemi di produzione cyber-fisici" spiega Kern.
Produttività in aumento
Questo progetto sta producendo informazioni preziose e permettendo agli ingegneri di derivare altre applicazioni. “Ridurre i tempi di produzione con un orientamento alla creazione del valore e all'autogestione ci permette di aumentare la produttività del 20%” riprende Kern. Il passo successivo sarà integrare l'assemblaggio modulare su una scala più ampia nel pre-assemblaggio, perché è proprio in questa fase che si trova la massima variabilità, insieme a dinamiche che possono essere gestite in modo più efficiente. "Scollegare le stazioni consente di riprogrammare le cose senza troppi sforzi" conclude Kern. Grazie all'hardware flessibile e ai veicoli a guida automatizzata impiegati per il trasporto dei componenti, spesso basta regolare solo il software, visto che le stazioni possono essere adattate ai prodotti e alle richieste più facilmente rispetto a un nastro trasportatore.
Fonte: AUDI AG
VGI | Responsible OU: VP | Creation date: article date | Class 9.1