Sustainable right from the start: Audi’s “CO₂ program�
For Audi, sustainability means reducing CO2 emissions throughout a car’s entire life cycle. When it comes to electric cars, the question lies in the manufacturing process rather than in the exhaust pipe. And that’s precisely the starting point for the company and its suppliers.
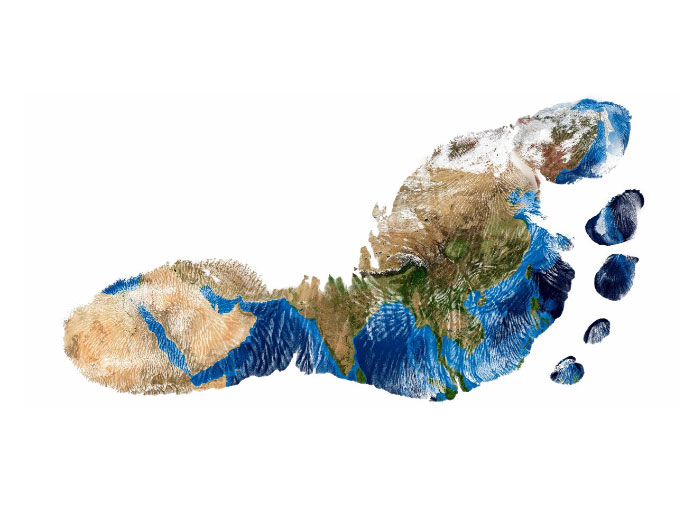
We live beyond our means. The figures from 2019 speak for themselves: July 29 was the day on which we consumed all the natural resources that the Earth theoretically provided us with for the year. Earth Overshoot Day is the benchmark for humanity’s ecological footprint. Every year, it is brought further forward in the calendar. At present, we are consuming the resources of around 1.75 Earths.
According to Global Footprint Network, halving our CO₂ emissions would push back Earth Overshoot Day by 93 days and make a significant contribution to combating climate change. Not only is decarbonising the economy our best possible chance of addressing climate change, but it would also vastly improve the balance between our ecological footprint and the planet’s renewable natural resources.
Consistently electric
Reducing CO2 emissions is therefore the most important action we can take. Recognising its responsibility, the Volkswagen Group was one of the first companies to sign up to the Paris Climate Agreement and set itself the target of becoming carbon neutral by 2050. Audi is also at the start of a major transformation - by 2025, it aims to reduce its carbon footprint by 30 percent. Various measures have already been implemented to drive forward progressive decarbonisation.
Consistent electrification of its vehicle fleet will help the company achieve its targets. But it must make the right adjustments to fully leverage the potential, in particular by cutting emissions during manufacture. The energy revolution also plays a decisive role: using green electricity vastly improves electric cars’ environmental balance over their entire life span.
The circular economy
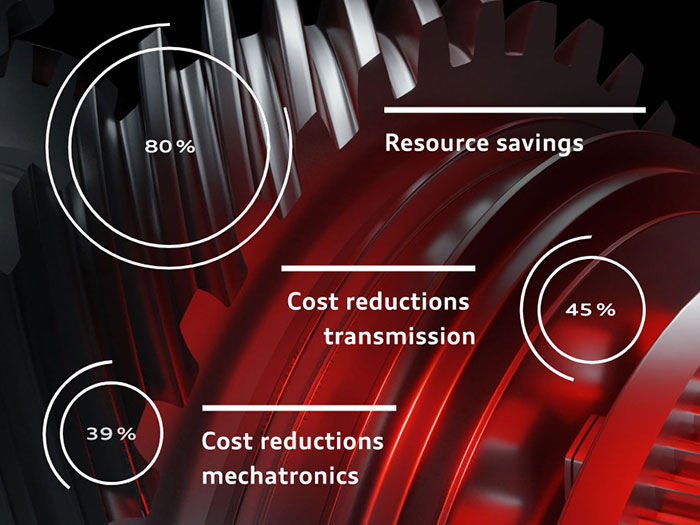
Audi’s goal is an ambitious one - the creation of a circular economy. To achieve its goal, a multi-level approach is necessary, and this is precisely the strategy that Audi and the Volkswagen Group have adopted on the journey towards carbon neutrality. The vision consists of three “commandments”: reduce, reuse, recycle.
Audi’s approach is working. Projects such as the Aluminium Closed Loop, where offcuts are returned to suppliers and recycled, make a significant contribution to decarbonising the company and saving resources. Reuse can also drastically reduce the demand for new raw materials. The aim is to promote the use of secondary materials. Apart from aluminum and steel, materials for the battery offer great potential in particular, and a research project has tested a closed loop for recycling cobalt and nickel.
Supply chain efficiency
The switch to electric mobility shifts the balance in terms of CO₂ production, and means that the most of emissions are generated in the supply chain. Almost a quarter of all CO₂ emissions will be produced at Audi in 2025 from the supply chain and production processes. To combat this, the company initiated a specific programme a year ago that involves cost-cutting measures across all levels of the supply chain.
Together with suppliers, Audi has so far defined 50 measures that help cut emissions right from the start, such as using renewable energy sources, recycling processes, or closing material loops. In this way, 1.2 tons of CO2 per vehicle could be saved in future. In particular, energy-intensive materials such as steel or aluminum offer lots of savings potential.
Remanufacturing components...
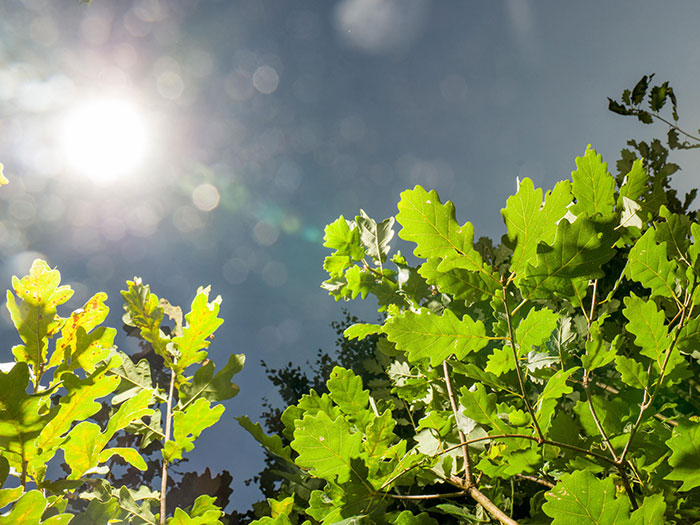
Remanufacturing is another form of reuse - this means the industrial overhaul of used parts to produce parts of original quality. This process and the sale of these parts through the spare parts business generates significant added value. And not just environmentally, but also economically, since it saves money.
On this basis, Audi has launched Exchange 2.0 which is currently being tested on complex parts such as transmissions and will be extended to other spare parts in the future.
...battery recycling...
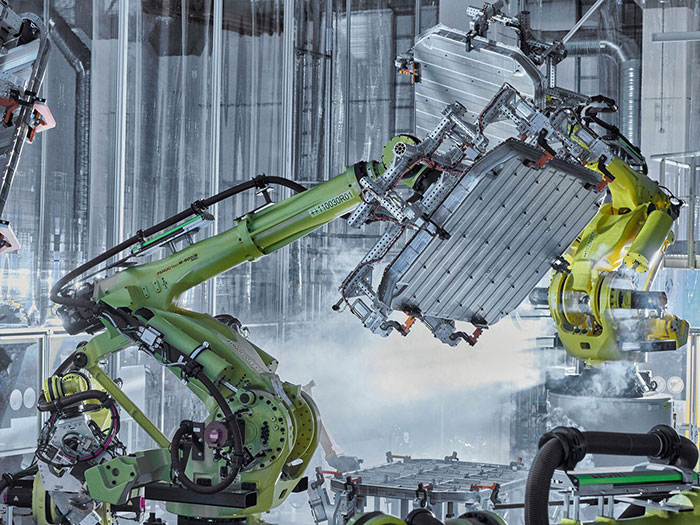
Audi is also taking steps to make the life cycle of these batteries as sustainable as possible and has been an active member of the Global Battery Alliance. The alliance focuses both on the protection of human rights and social standards when extracting raw materials as well as on the creation of solutions for reusing lithium-ion batteries.
Audi is also involved in other joint research projects, for example with the recycling group Umicore, in order to develop a loop for parts of high-voltage batteries that could be reused multiple times.
...a second life
Used batteries also get a “second life” at the main plant in Ingolstadt where they are being used to power fork-lift trucks and towing vehicles.
“Every lithium-ion battery represents high energy consumption and valuable resources that must be used in the best possible way,” says Peter Kössler, Member of the Board of Management for Production and Logistics at AUDI AG.
Using every bit of aluminum
A practical example of Audi’s commitment to preserving environmental resources is aluminum. Audi was the first automaker to use the material for its models. The benefits are obvious: the material doesn’t rust, is easy to machine, and, most importantly, it makes cars light. The downside is that its production requires very large quantities of energy and natural resources. It takes around 15 megawatt hours of power to produce a ton of aluminum. That’s roughly the same as the amount a two-person household consumes in five years.
Audi is conscious of its responsibility and therefore, in 2013, the brand with the Four Rings became a member of the Aluminium Stewardship Initiative (ASI). The ASI has developed a global standard for the handling of aluminum with environmental and social criteria along the value chain. In 2018, Audi received the Performance Standard certificate from the ASI for its responsible use of aluminum for the battery housing on the Audi e-tron.
Source: AUDI AG