Audi tests glass cycle in an innovative pilot project
To recover glass from windshields and windows that cannot be repaired and put it back into production as a recycled material - that is the goal of Audi's one-of-a-kind new pilot project.
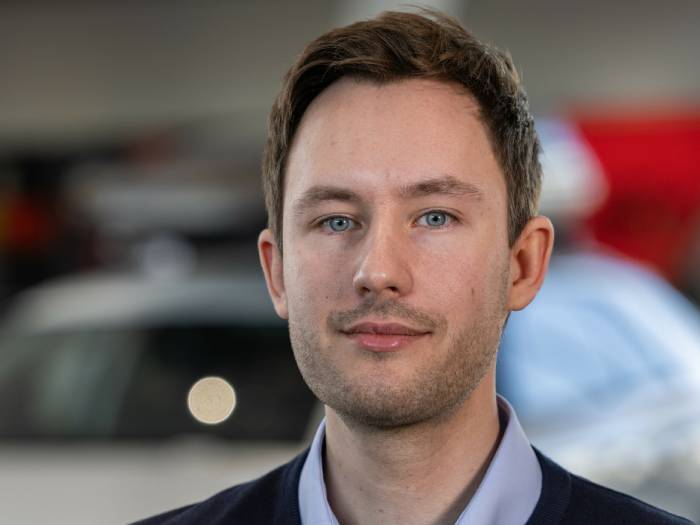
Increasing sustainability requires a holistic approach, covering all stages of production. That's why Audi, together with its partners, has activated a pilot project to create a closed material circuit for damaged car glass. The project will last one year and involves recycling glass from damaged windows and windshields, saving not only raw materials but also water and energy in the production process.
The ultimate goal is to implement this process in the production of the Audi Q4 e-tron. "We intend to increase the proportion of secondary materials in our cars, and according to our research, car glass recycling has a potential" explains Philipp Eder, Project Manager for Circular Economy Procurement Strategy at Audi.
Recycled glass for windows
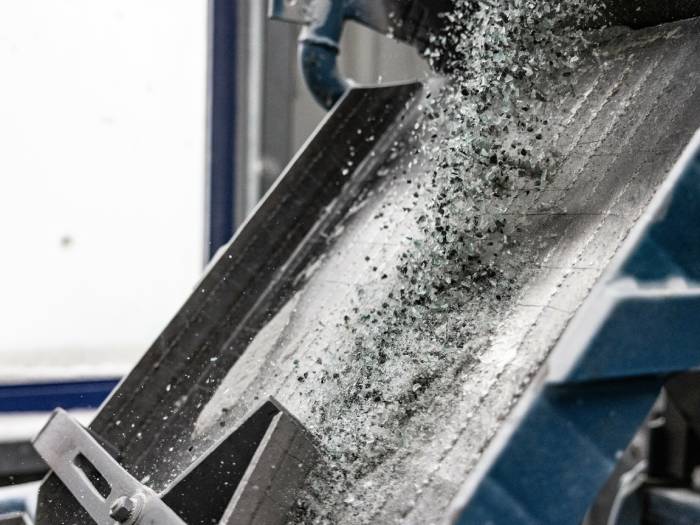
The first stage of the project is to collect the irreparably damaged windows and send them to Reiling, a company specialized in glass recycling, where they are broken into small pieces and processed. In the next step, the fragments are reintroduced into the production of glass sheets. "Until now, recycled material has mostly been turned into beverage bottles", explains Daniel Rottwinkel, Plant Manager at Reiling. This time, the goal is different, which is to restore damaged glass to its original quality, allowing it to be used to make new car windows.
This requires a careful sorting process to separate non-glass materials like the PVB (polyvinyl butyral) plastic layer that is found in the glass, window edgings, metal parts and wires. Magnets, non-ferrous metal separators, extraction units and electro-optical sorting units are used in the elimination process.
Purity and homogeneity of materials
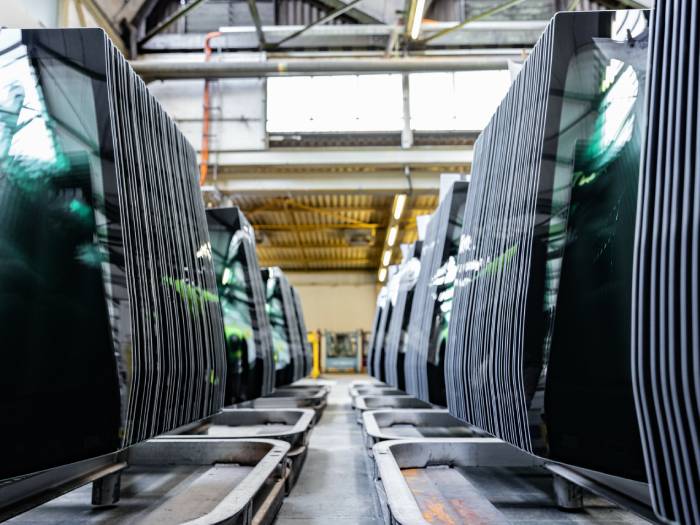
After all waste elements have been removed at Reiling, the material - which must be as pure and homogeneous as possible - is sent to another specialized company, Saint-Gobain Glass, which processes it into plate glass at its plant in Herzogenrath, Germany. Starting with these plates, which are rectangular and measure about 3 x 6 meters (10 x 20 feet), windows and windshields are then made.
At this stage, the recycled glass is mixed 30-50% with other components that do not come from automotive sources, such as quartz sand, sodium carbonate and chalk. "This pilot project is an important step toward sustainable production, allowing us to save resources and energy", adds Markus Obdenbusch, Production Manager at the Saint-Gobain plant in Herzogenrath.
Recycling to reduce carbon dioxide
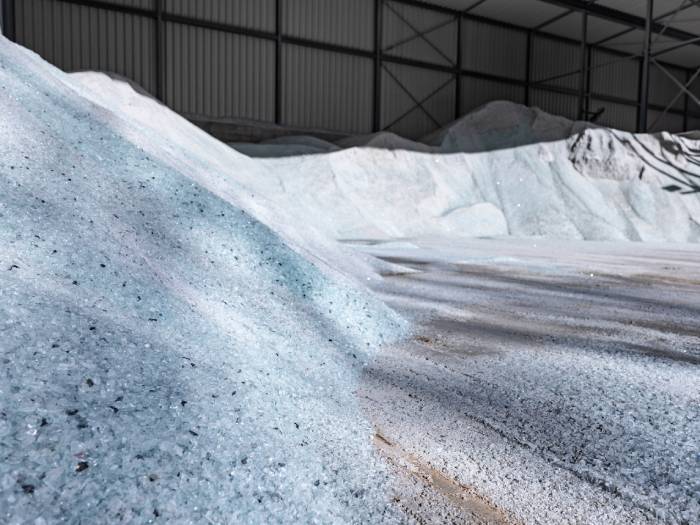
"We’re just starting to look at glass as a recyclate material in these applications, so we anticipate that there will be more potential for improvement", Obdenbusch concludes. At the Herzogenrath plant, in addition to the quantities related to the Audi pilot project, an additional 30,000 tons of shards will be processed over the next three years, resulting in significant savings in energy and CO2 emissions. Translated into numbers, it means cutting up to 75 tons of CO₂ per workday, in addition to the significant reduction in water consumption.
Closed cycles for raw materials
The pilot project will run for one year, a period of time needed to verify the quality of materials, stability of supplies and process costs. If glass recycling proves to be a beneficial process, windows produced in this way will be integrated into the production of the Audi Q4 e-tron.
With this pilot project, Audi once again proves how its partner companies are also working to incorporate raw materials into closed, intelligent cycles. The ultimate goal is to use secondary materials wherever that is technically possible and economically sensible, to optimize the value chain and conserve resources.
Source: AUDI AG
VGI | Responsible OU: VP | Creation date: article date | Class 9.1