E-mobility: 500 new jobs in Ingolstadt for the new Audi Q6 e-tron
The path to e-mobility includes the creation of new jobs, in parallel with the training and upgrading of employees already working at Audi, who in this way can obtain new qualifications and reinvent themselves.
The new Audi Q6 e-tron, which will be based on the Premium Platform Electric (PPE platform), represents a turning point for the Four Rings brand. With the arrival of this new model, the transformation journey continues, a process that also involves employees, who are preparing and training for the new era of electric mobility.
"The 500 new jobs related to the production of the new Q6 e-tron show how the transition to electric mobility is also an opportunity in terms of employment", said Xavier Ros, Chief Human Resources Officer at Audi, explaining how the company is also considering hiring employees who already have temporary jobs in Ingolstadt.
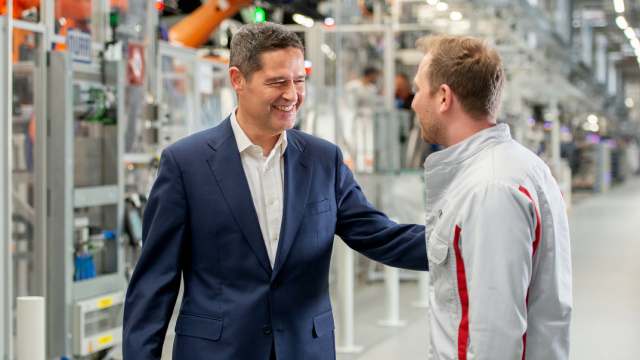
Training for all
In the transition to electric mobility, it is crucial for Audi not only to create new jobs, but also to transform and upgrade the existing workforce. "The transition to electric mobility is made possible by our employees, who continue to gain qualifications and reinvent themselves professionally", Ros added. To this end, Audi offers many training opportunities for its employees, with the aim of preparing and enabling them for new tasks.
Over the past 18 months, around 8,300 employees in the production, technical development and sales departments at the Ingolstadt headquarters have gained new qualifications in preparation for the launch of the Q6 e-tron. Added to these are the 2,000 colleagues at the Győr plant who have been trained for the production of the Q6 e-tron's electric drivetrain. Overall, just in 2022 Audi has invested about 150 million euros in the development and training of its employees.
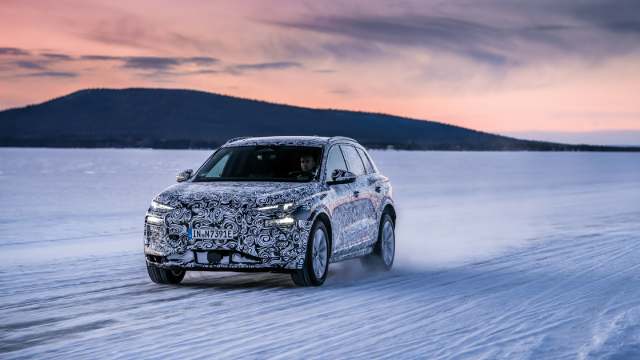
Ingolstadt's record
With the start of Q6 e-tron production, Ingolstadt will be the first German Audi site to assemble batteries in-house. "We are structurally shaping the transition to electric mobility: battery assembly has already created 300 attractive and future-proof jobs at the Ingolstadt site. At the same time we are building valuable know-how that will be useful for the production of 100% electric vehicles at all our sites. With electrification we are completely realigning our worldwide production network, and battery assembly in Ingolstadt is part of this process," explained Gerd Walker, Chief Production Officer at Audi.
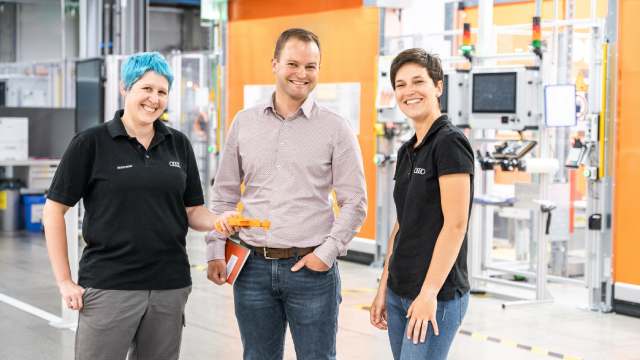
Vorsprung 2030
Audi's transformation is driven by the company's Vorsprung 2030 strategy, which calls for the gradual phase out of combustion engines before the 2035 limit set by European institutions. As a result, all Audi production sites are reorganizing and preparing for electric car production; by the end of this decade, every Audi plant worldwide will produce at least one 100% electric model.
The 360factory strategy also includes ambitious goals for plant transformation, which Audi Production is addressing with a holistic approach across five strategic domains: optimized production processes, digitization to increase efficiency, sustainable and resilient supply chains, flexible production networks, and clear sustainability goals.
New job opportunities
"We are creating new job opportunities at all of our locations as we are tackling the transformation together with the employees within our production network," Ros resumed, going on telling how the next step is to build an in-house battery module production facility in Ingolstadt for the next generation of electric models.
On the road to the new mobility, Audi is currently looking for new specialized engineering or electrical employees with proven professional experience and software experts for technical development.
Source: AUDI AG
VGI | Responsible OU: VP | Creation date: article date | Class 9.1