360factory: Audi plans production for all-electric mobility
All Audi plants will manufacture all- electric vehicles by 2029 and factory costs will be halved by 2033. With its Vorsprung 2030 strategy, the Brand is accelerating its transformation into a provider of sustainable premium mobility.
From 2026 Audi will launch only new all-electric models onto the global market, gradually phasing out production of its combustion vehicles by 2033. A clear vision, the basis of the Vorsprung 2030 strategy, which requires the transformation of all company structures. Audi is investing in its global production network: "Step by step, we are bringing all our plants into the future. We are investing in existing plants to make them as efficient and flexible as newly built and designed production sites," explains Gerd Walker, Audi AG Board Member for Production and Logistics.
According to Walker, this approach exemplifies sustainability, not only in economical, but also ecological and social terms: "The path Audi is taking conserves resources and accelerates our transformation into a provider of sustainable premium mobility services".
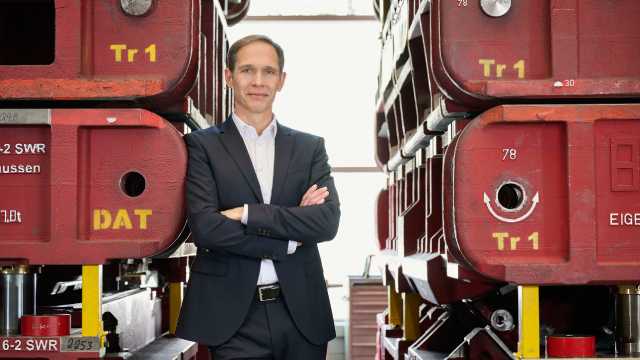
Transforming production
Transforming production means making it flexible and resilient over the long term, ready for the challenges of the future. That's why Audi has developed its global strategy with different perspectives in mind. Walker and his team focused on the expectations of society and stakeholders, the demands of customers and the future needs of employees.
To answer these questions Audi has created 360factory, which is a vision of the future based on an approach that puts sustainability, flexibility, attractiveness and cost-effectiveness on the same level. As all-electric models will be produced in all Audi plants around the world by 2030, Audi's highly skilled workforce will play a key role, and all employees will receive specific training by 2025, with an investment of about 500 million euros.
Böllinger Höfe and Brussels
Already today, the Böllinger Höfe and Brussels sites produce all-electric vehicles; in 2024 the Audi Q6 e-tron will be the first all-electric model to roll off the production line in Ingolstadt. At the same time, production of all-electric cars will also gradually start in Neckarsulm, San Jose Chiapa (Mexico), and Győr (Hungary).
Depending on local needs and conditions, production of the remaining combustion models will be gradually phased out by the beginning of the next decade. New plants will only be built where additional production capacity is needed: Audi and its partner FAW are building a site in Changchun (China) to locally produce models based on the PPE platform. It is expected to be completed by the end of 2024 and will be the first Chinese Audi plant dedicated only to all-electric models.
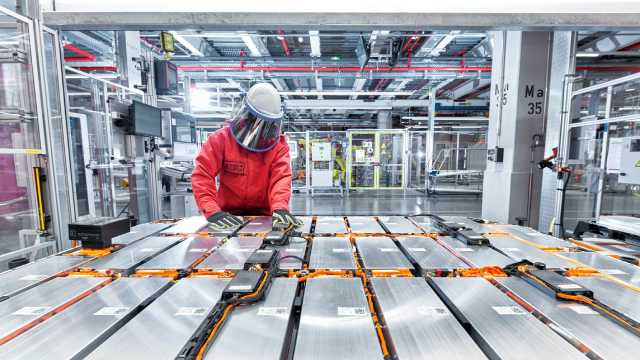
Electrifying plants
The electrification of plants is only one part of Audi's path towards the production of the future. "With the transition to electric mobility we will make major leaps in productivity and optimization," says Walker, who then emphasizes how Audi's production network will have to be highly economical, sustainable, and flexible. Specifically, the Brand's goal is to cut annual factory costs in half by 2033. To achieve this, the complexity of vehicles will be reduced where it does not benefit customers by adopting a simplified production process from the earliest stages.
At the same time Audi will continue to increase the digitization of production, for example by implementing systems that use local servers to replace expensive industrial PCs, such as Edge Cloud 4 Production, optimizing and rationalizing IT efforts.
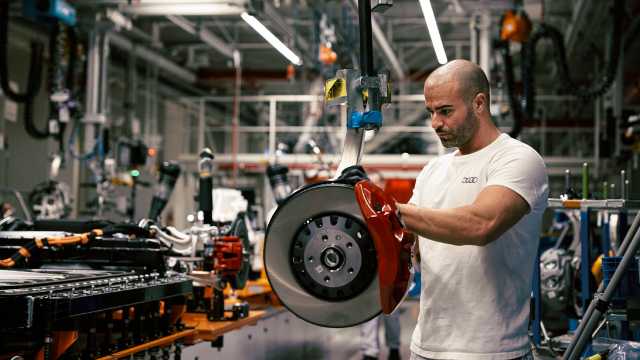
Modular assembly
At the purely production level, in the near future Audi will rely on modular assembly, a solution based on ‘production islands’ that are independent of cycle and line schedules and can adapt to the variability of products and demand. In addition, production planning will make use of 3D scanning and quality control through artificial intelligence and machine learning.
Process flexibility, on the other hand, is needed to respond promptly to changes in customer demand and production programs. "Both products and production will have to bring maximum benefit to our customers," summarizes Walker. New Audi Q6 e-tron will initially be produced in Ingolstadt on the same line as the Audi A4 and Audi A5; all-electric models will then gradually replace the combustion cars on the line.
Mission:Zero
Since 2019 Audi has been pursuing its Mission:Zero environmental program, with the goal of reducing the Brand's ecological footprint, in which production and logistics play an important role. The target is to make all production plants carbon neutral by 2025; both Győr and the Böllinger Höfe have already received this certification. The program also includes efficient use of resources and water, along with protection and conservation of biodiversity.
Audi intends to halve water consumption in production facilities by 2035, taking a cue from Neckarsulm, where a closed water cycle involving the municipal wastewater treatment plant has already been implemented with a pilot project and reduces freshwater demand by more than 70%.
Closed cycles
By 2030, Audi also aims to cut its environmental impact in primary energy consumption, power plant emissions, CO2 equivalents and air pollutants in half, compared to 2018. The target also covers local water risk and wastewater and waste volumes.
To get there, Audi will focus on in-house generation of renewable energy and the use of innovative technologies to create more circular value chains in which resources are used in closed cycles. The Audi 360factory program will also enable the company to strengthen its attractiveness as an employer, both internally and externally.
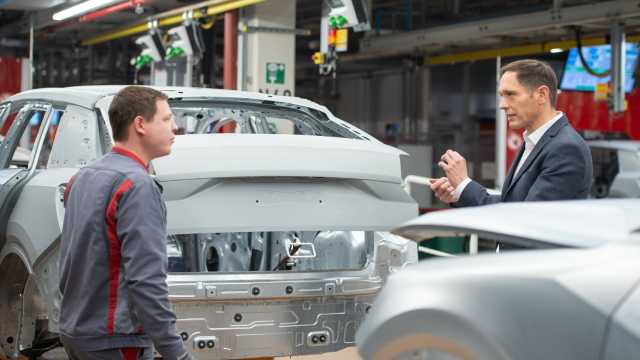
Flexible working
In this regard, Audi has implemented some innovations to make working hours more flexible, even in areas that are tied to specific shifts; at the same time, the working environment and break rooms become more comfortable.
The Audi Production division does not see itself purely as a vehicle manufacturer, but also as a developer of process technologies. "We want to be the best employer, for our employees already onboard and for those who will come. The transformation into the 360factory will require the very best minds, even in disciplines not usually associated with production, such as electronics and software development," Walker further explains.
Audi 360factory
The Ingolstadt plant will be the first to follow all the principles of the Audi 360factory program and will serve as a blueprint for the transformation of all other plants around the world. "We still have a long way to go, but the direction and the steps to get there are clear", Walker concludes.
Source: AUDI AG
VGI | Responsible OU: VP | Creation date: article date | Class 9.1