SEAT Prototype Development Centre: synergies for innovation
In the heart of SEAT’s Martorell production plant, the Prototype Development Centre (PDC) embodies a concept aimed at innovation within development processes.
The Prototype Development Centre opened in 2007, bringing together the Prototypes department and the Pilot Processes Engineering Workshop under a single roof – and the Centre serves as the link between Research and Development (R&D) and Production at SEAT.
The Centre, which covers 19,000 square metres of the Martorell factory, brings together activities that relate to the initial stages of design and development of new virtual and physical models, together with issues of feasibility, productivity, problem analysis and a proactive, pre-emptive approach to problem-solving in production processes.
Synergies and shared resources
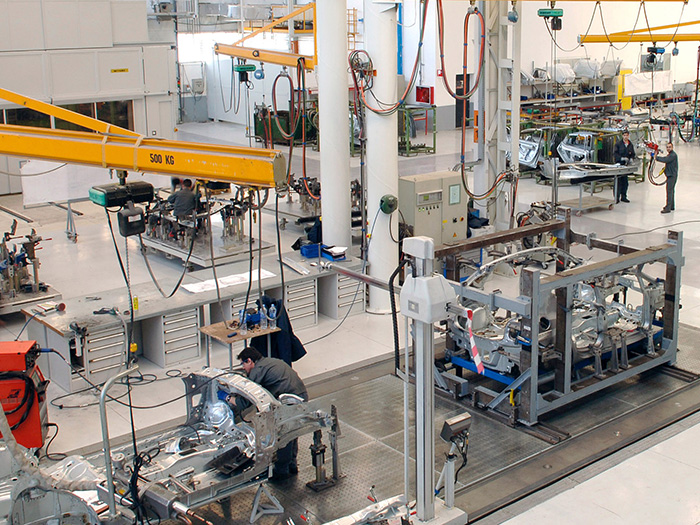
One of SEAT’s flagship projects, the Prototype Development Centre uses shared resources and harnesses the resulting synergies between both departments in order to shorten development time as well as improve communication regarding new models between R&D and Production.
The Centre’s areas of expertise in project management, virtual reality, DKM models, presses, bodywork, painting, logistics and special vehicle assembly are managed by close to 300 highly qualified professionals.
The aim is to achieve greater efficiency in the processes of building new virtual and physical prototypes, thus shortening time between new launches, while improving quality. Sharing organisation and space means seamless cooperation, coupled with a consistent flow of information during development and industrialisation stages.
Development stages
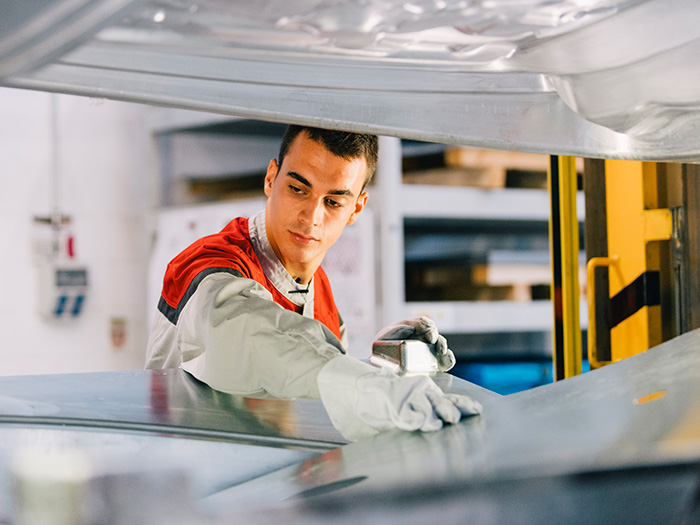
Within the PDC, confidentiality is always guaranteed – it is absolutely normal to put a new prototype through the assembly line so as to analyse model feasibility during the early stages of development.
Each area of the PDC works on specific activities, including data control model creation, prototypes and pre-production vehicle development, analysis and improvement of production, digitalisation of manufacturing processes and virtual ergonomy.
The PDC brings together personnel from very diverse company areas, which adds additional value by encouraging the exchange of opinions and suggestions from a range of different backgrounds – a valuable tool for the continuous development of skills and innovative solutions.
Virtual ergonomy
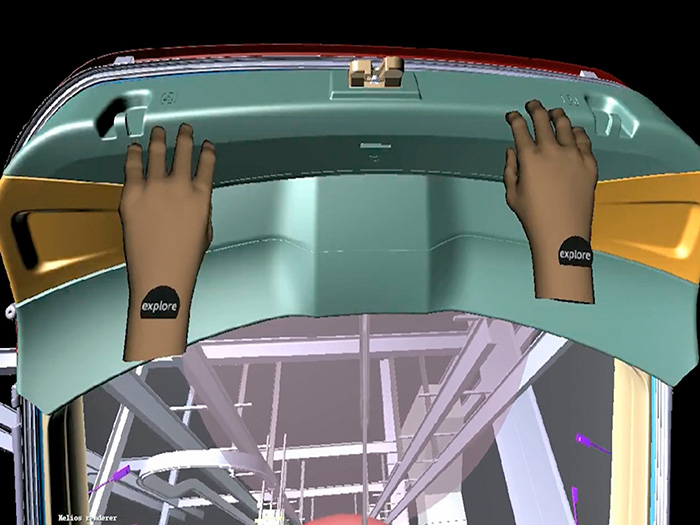
One of the tools used by the Centre is the ‘Applied Virtual Ergonomy’, an application from the MAVE project (Spanish initials for ‘Ergonomic Virtual Analysis Mock-up’), used to simulate assembly operations without the need for physical vehicles or assembly lines. By doing so, operator fatigue during routine tasks can be determined and, where necessary, solutions can be implemented.
Additive manufacturing and virtual reality
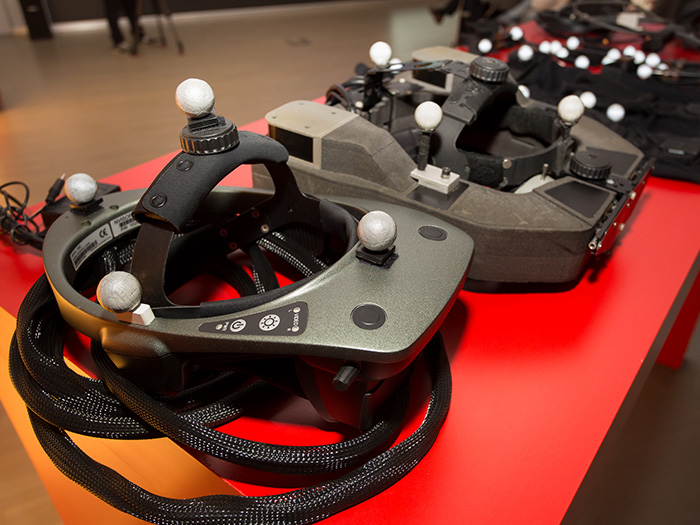
One example of the PDC’s commitment to innovation is additive manufacturing, which was introduced some years ago. This is a production method whereby layer upon layer of material is very precisely deposited one on top of another. Implementing this technology reduces intermediate processes and enables parts to be made up to 75% faster.
And finally, virtual reality also plays a key role in the Centre’s activities – this is another technology that brings clear benefits in terms of time and cost savings.
Source: SEAT S.A.