Improving ergonomics and efficiency with exoskeletons
Audi is testing the technology to relieve the burden on employees’ muscles and joints in the shoulder area - aiming to make work easier and more efficient, and optimise production.
Many process steps in production involve overhead jobs, with the consequent risks for muscle and joint strain. For this reason, Audi is currently testing exoskeletons – external support structures worn by employees to aid their movements, protecting their joints and muscles - with the aim of enhance ergonomics for the employees, in all its plants.
A comparative study of two separate exoskeletons is currently being conducted. Both are designed specifically to help employees when they are performing overhead tasks. Around 60 technicians will be trialling the exoskeletons tools over a period of several weeks at selected workstations in assembly, the paint shop and tool construction at the Ingolstadt site.
The assembly line
Tasks that involve overhead jobs are unavoidable on an assembly line. Exoskeletons offer valuable support when other measures have been exhausted. As mentioned, Audi is currently performing comprehensive tests on two of these aids – the Paexo from Ottobock and the Skelex 360 from Skelex. The best one will be chosen based on feedback.
“Our employees are our most important asset. We want to enhance their health and workplace conditions, and constantly reduce the strain they are under,” says Peter Kössler, AUDI AG Board of Management Member for Production and Logistics.
Testing on the job
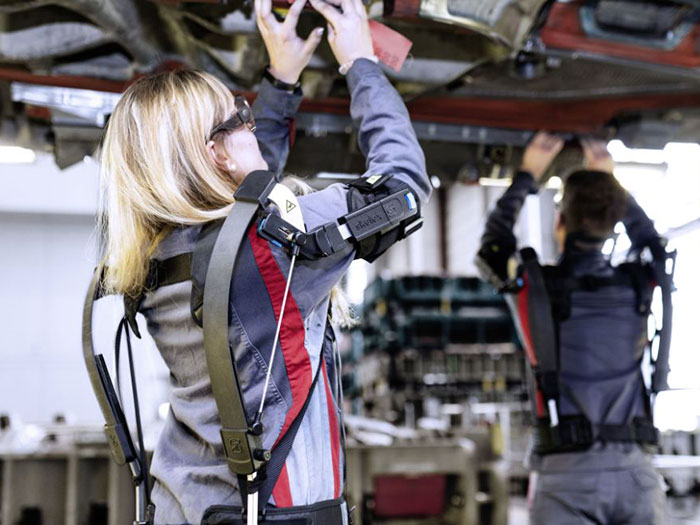
There are many questions about exoskeletons to be answered through practical testing: is freedom of movement restricted? Is the material still pleasant even after it has been worn for some time? How much support do exoskeletons offer employees in performing their tasks?
Concrete answers will come from the practical trials conducted directly on the field. The exoskeletons are being tested in both static and dynamic activities, e.g. installing the brake lines, screwing the underbody panelling into place and applying corrosion and sealing protection.
A special “backpack”
Both exoskeletons used by Audi employees are worn like a backpack on the shoulders and secured in place with a belt around the hips. Arm shells support the arms when the wearer is performing overhead work. These absorb part of the arm’s weight and re-direct it to the hips via support structures. This reduces the burden on the shoulders. This is done purely mechanically, without any motorised drive.
The importance of ergonomics
Exoskeletons are nothing new in Audi production. The company has already trialled them in the past, using different technologies in a number of pilot projects. One such system is a structure created by Laevo that reduces the burden on the person’s back when they are lifting or moving heavy objects. Initial tests were carried out in logistics, the press plant and assembly and yielded promising results.
So it should come as no surprise that the ergonomics experts from the company with four rings see considerable potential for using exoskeletons: “The main focus here is always on ergonomic benefit, wearing comfort and reducing the burden on our employees,” says Ralph Hensel, a specialist in exoskeletons at Audi. The goal is to implement exoskeletons across all of the company’s plants.
Source: Volkswagen AG