PowerCo develops a revolutionary technology for battery cell production
The new battery cell production process, known as dry coating, will save about 30% energy and 15% floor space in plants, lowering production costs.
With sustainability in mind, reducing energy consumption is a key factor. That is why the Volkswagen Group is planning to introduce a completely new production process in its European and North American gigafactories. The introduction of this innovation is being managed by PowerCo SE - the Volkswagen Group battery company, based in Salzgitter - and the goal is to boost efficiency and sustainability of volume battery cell production.
The new process being industrialized is so-called Dry Coating, which can reduce energy consumption by about 30%, as demonstrated by internal tests already carried out together with partner Koenig & Bauer AG, German printing machine specialist.
Dry Coating
"Technologies like Dry Coating showcase PowerCo's technological prowess. As a Group we have all the necessary know-how and the right experts to take cell production to a new level and offer significant cost advantages to our customers. Our objective is to establish an industrial production of sustainable and affordable batteries" said Thomas Schmall, Volkswagen Group Board Member for Technology and Chairman of the Supervisory Board of PowerCo SE.
PowerCo SE and Koenig & Bauer have signed a Joint Development Agreement aimed at developing a roller press for powder coating electrodes at large industrial scale.
An innovative process
Dry Coating makes it possible to produce electrodes by eliminating the 'wet' coating steps and subsequent drying, both very expensive processes. With the new procedure, both the most energy-intensive part of cell manufacturing and the use of chemical solvents are no longer required.
The new technology is currently being tested in a pilot line in one of PowerCo SE's laboratories in Northern Germany. Koenig & Bauer, on the other hand, as a printing process specialist is developing an industrial powder coating machine. PowerCo SE estimates that the new technology has the potential to reduce energy consumption by 30% and save 15% of floor space within the plant, saving production costs by hundreds of millions of euros per year.
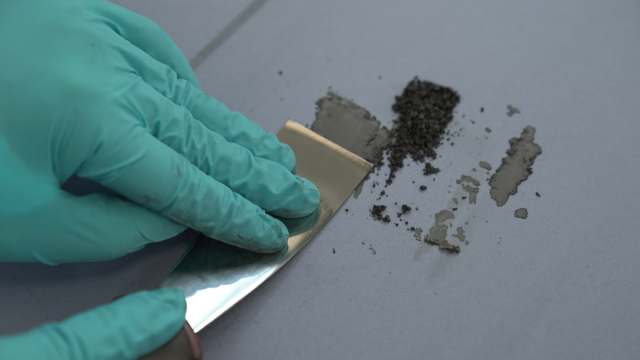
Revolutionizing production
"Dry Coating is a real revolution for production, just what solid-state cells is for product. If scaled successfully, it will give us a unique position on the market and definite competitive advantages", explained Frank Blome, CEO of PowerCo SE.
The electrodes (cathode and anode) are the fundamental components of the cell and define both the battery performance and energy density. In modern industrial electrode production, the battery materials are mixed with additives and liquid solvents until they form a wet slurry, which is then applied as a coating on copper or aluminum foils. This is finally followed by the drying process and calendering, i.e., rolling of the foils.
Recharging and efficiency
The new dry coating process developed by PowerCo SE imitates the printing process in some ways, allowing base powder materials to be applied directly to the foil as it is being rolled (or calendered). This eliminates two out of four steps in the electrode manufacturing process. In addition, the fact that the powder coating is applied to the foil in an extremely fine and uniform, hair-thin layer results in excellent energy density, extending the life cycle and improving the battery's fast-charging capability.
As for space requirements within the plant, each building block of a regular gigafactory with a production capacity of 20 GWh will no longer require four parallel coating and drying lines, which would occupy an area of 7,000 square meters. As a result, the exterior length of the plant can be reduced by about 100 meters.
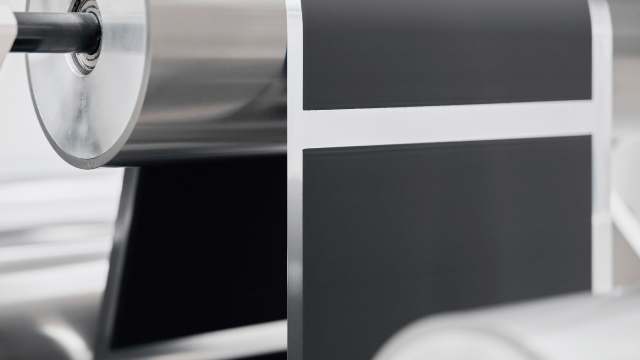
Saving energy
In terms of energy savings, the elimination of drying furnaces and suction systems saves an amount of energy equivalent to the annual consumption of 40,000 private households. Chemical solvents are also eliminated, with further significant energy savings due to the elimination of the recycling process, which takes place in silo-like towers located outside the plants.
The development of the new processing technology together with Koenig & Bauer is set to be completed by 2024, and exclusive rights have already been agreed upon for the period after that, the details of which are confidential and for which separate agreements have been signed. Series production is expected to start in 2026-2027. "Our plants are designed for quick and easy retrofits. In total, we have anticipated about 30 foreseeable innovations in products and production, so we are able to adjust our plants to all relevant new processes as soon as they enter the market", concluded Sebastian Wolf, Chief Operation Officer of PowerCo.
Source: Volkswagen AG
VGI | Responsible OU: VP | Creation date: article date | Class 9.1