Electric cars: Volkswagen batteries put through more than 5,000 safety tests
Every battery system developed undergoes more than 5,000 tests before it is approved for use in a production vehicle. The responsibility for this lies with the Battery Development Center in Brunswick – guaranteeing the highest safety standards at all times.
Safety is the priority for every Volkswagen model, and that naturally applies to electric vehicles too – which is why the Group subjects its e-car batteries to a series of comprehensive and rigorous safety tests and checks before they hit the road. “At the Battery Development Center in Brunswick, we test almost every conceivable case that could affect the battery system during a car’s operating life – from accidents to extreme temperatures.
The safety of drivers is the most important thing for us,” explains Dr. Michal Bruna, Head of Electronics Development and Testing at the Battery Development Center of Volkswagen Group Components. That is why every variant of the battery, including the software, has to prove its safety in more than 5,000 individual tests.
Extreme tests
Life cycle tests are an important part of the test procedures. The batteries are subjected to stresses in mechanical shocks such as those caused by curbs, stone chippings or railroad crossings. Over a two-week vibration test, the complete life cycle of a vehicle is simulated.
Other tests reproduce thermal shock immersion, which can occur when driving through could water. The battery systems are also tested under different climatic conditions with the test rigs, where temperature and humidity can be adjusted and charging and discharging cycles simulated. At the end of each test, the battery system is disassembled and experts examine its condition.
Salzgitter and Wolfsburg
Brunswick is not the only facility that tests Volkswagen Group batteries: other sites specialise in monitoring different aspects. The Center of Excellence in Salzgitter, for example, tests the quality of the lithium-ion battery cells; and Technical Development in Wolfsburg tests the cell modules.
“This is how we ensure, for example, that each battery can actually achieve the maximum range,” continues Bruna. The software and control units are tested automatically for functionality, safety, reliability and smooth interaction via special “hardware-in-the-loop” test benches (this technology simulates the electric and electronic systems that the units being tested will be used for). And in battery production too, the functionality and safety of each battery is checked before it is delivered to the plant where vehicles are assembled.
The safety of electronics
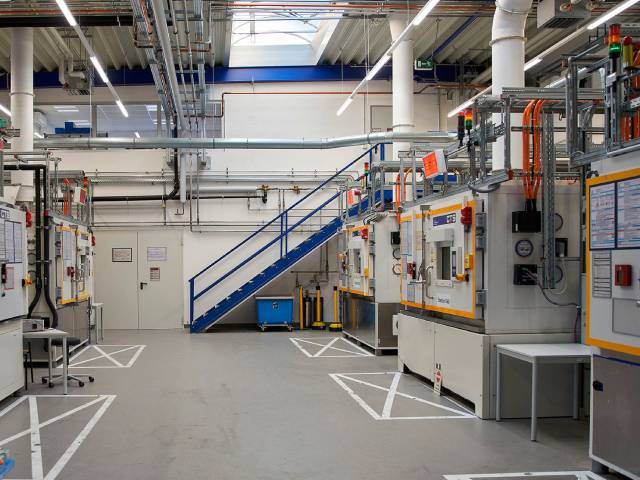
The highest safety standards that exist in the automotive industry apply to battery electronics. This means that a safety-relevant fault may occur only after 100 million operating hours at the earliest.
In the event of a vehicle accident, the electronics shut down the battery system so that the car cannot become electrically live and – even in this exceptional situation – the driver and passengers remain safe.
Protecting the battery
“The battery is located between the axles of the cars and is thus already well protected by the vehicle architecture. In the event of an exceptionally severe crash, the battery system can still be damaged, of course – but no safety problems should arise,” says Bruna. If the airbag deploys, the battery system is automatically disabled. It can only be started after specific checks in a workshop. Passenger safety always comes first.
Source: Volkswagen Newsroom