Mechatronics technicians and more: the new professionals of e-mobility
The electric revolution is underway - it needs new cross-sectoral skills and lot of enthusiasm. The Volkswagen Group set specific courses for thousands of employees.
Revolutionising mobility and make the electric cars available to all does not mean only designing technologically advanced vehicles, manufacturing them emission-free and “fuelling” them with electricity from renewable sources.
Entering a new era of mobility also requires trained technicians capable of dealing with the latest production challenges and making the best use of digital tools. This is why the Zwickau plant, where the Volkswagen ID.3 will start to roll off the production lines this autumn, is currently in the middle of a massive training program involving 3,000 employees.
Enthusiasm and expertise
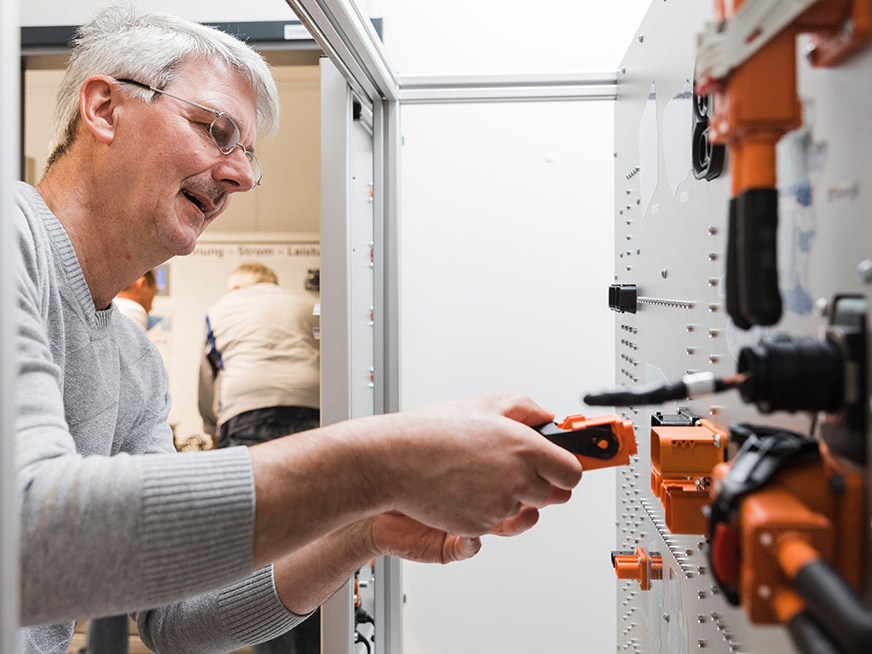
“We don’t just want to provide information and training, we also want to instil enthusiasm”, says Daniel Stolka from the Volkswagen Lean Academy, which developed the program together with the Volkswagen Training Institute and the Zwickau training centre.
That explains why all courses always begin in the three “E-motion rooms” where participants explore the history of electric mobility, from the 19th century to the present day. They then move through the various training stations, where as well as watching videos on battery production and fast charging, and taking quizzes on workplace safety, they will familiarise themselves with the new MEB platform (Modular Electric Toolkit). The new platform will be the foundation for Volkswagen’s next generation of electric vehicles, featuring ranges suitable for everyday use, spacious interiors and affordable prices.
Mechatronics technicians
Nearly 300 kilometres southwards, at the Audi Training Centre in Ingolstadt, the future mechatronics technicians are formed. The “blackboard” they are learning on is an electronic panel with various cables, boxes and connections: a measurement lab where they learn to manage electricity.
Over the past two years, everyone at Audi’s sites in Ingolstadt and Neckarsulm has passed through the small measurement lab. Or at least everyone starting an apprenticeship as an automotive mechatronics technician. “This job description is changing faster than you can imagine”, says instructor Rupert Kaindl. Good mechatronics technicians will need not just a passion for working on machines, but also an understanding of electrical engineering. “You can’t see or touch electricity, so mechatronics technicians increasingly need to think in the abstract. In the future, mechatronics technicians will have to be electricians as well. That is exactly what we want our training to prepare them for” explains Kaindl.
A flexible syllabus
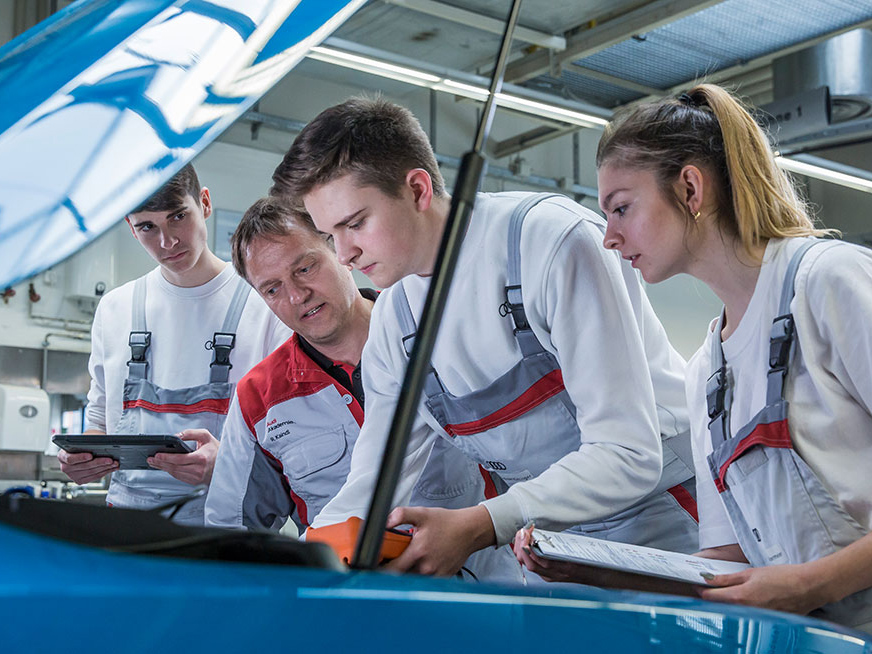
Audi’s e-mobility training program can be defined as a “hybrid learning concept”, as it combines digital and analogue methods, as well as theory and practice. The apprentices often learn at their own pace on their tablets – and then engage in teamwork: “At first I thought some people’s minds might wander during the partner exercises” says Kaindl. “But I was wrong. The tandem work is especially valuable and well received by the apprentices”.
Tests and assessments are carried out at regular intervals, to foster both feedback and a sense of accomplishment for the participants. As individually oriented as the learning process is, the goal of the program is always the same: to train technicians able to work on electric cars, take them out of commission and put them back together again.
High voltage
To date, more than 300 apprentices have gone through Audi’s high-voltage training. “Many departments – including quality assurance, production and technical development – need people who can work on electric vehicles”, says Kaindl. The apprentices therefore have good job prospects. And many elements of their high-voltage education have long since been incorporated into further training programs for experienced mechatronics technicians.
Virtual reality
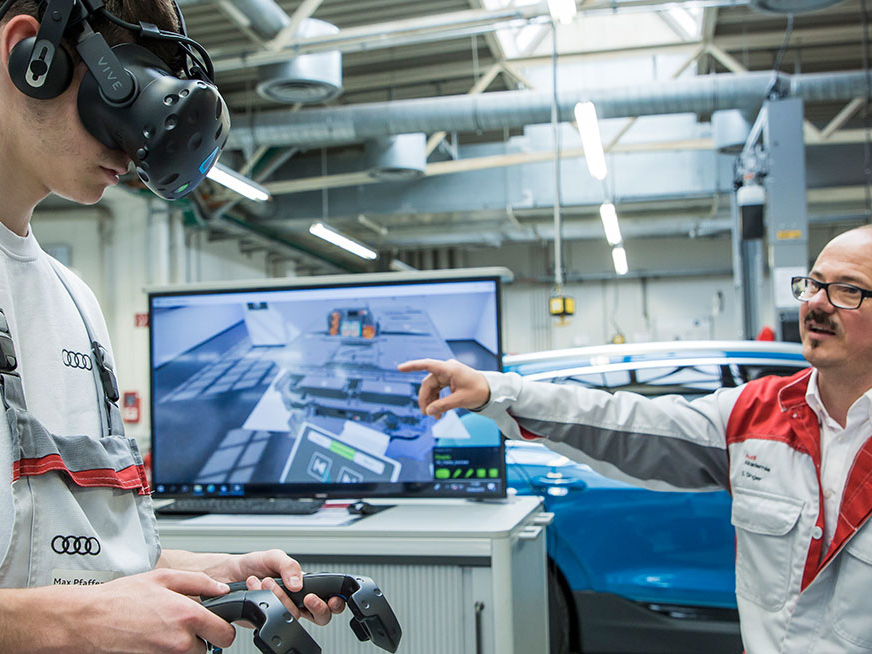
Virtual reality is an integral part of the training both at Zwickau and the Audi Training Centre in Ingolstadt. It allows students to manipulate a charging device or an air-conditioning compressor in virtual space, right from the get go.
It takes just a few minutes to gain the confidence to identify the key components, and then answer the instructor’s questions in real time. At the end of the exercise, the participants are rewarded with a shower of digital confetti.
After this phase, they move on to real life, with exercises on a panel which replicates the electrical connections of a real car. In all this, safety is obviously the most important aspect to take into account, given the voltages in play. Finally, the students move onto practice on real vehicles to show off what they have actually learned.
Source: Volkswagen AG