5 experts, one shared mission: environmental sustainability
As part of the Volkswagen Group's journey to achieve its goal of becoming carbon neutral, many of the 660,000 employees worldwide contribute to sustainable management and fight global warming on a daily basis. Here are five stories of people working every day to protect the climate.
Zsolt Zentai works at the AUDI Győr site in Hungary, which is carbon neutral mainly through solar energy. Zentai supervises the planning for the factory infrastructure and building technology: “We take every opportunity to save energy. We only install LED lights now and reclaim heat from the ventilation systems, and the energy we use mostly comes from renewable sources”.
Geothermal energy
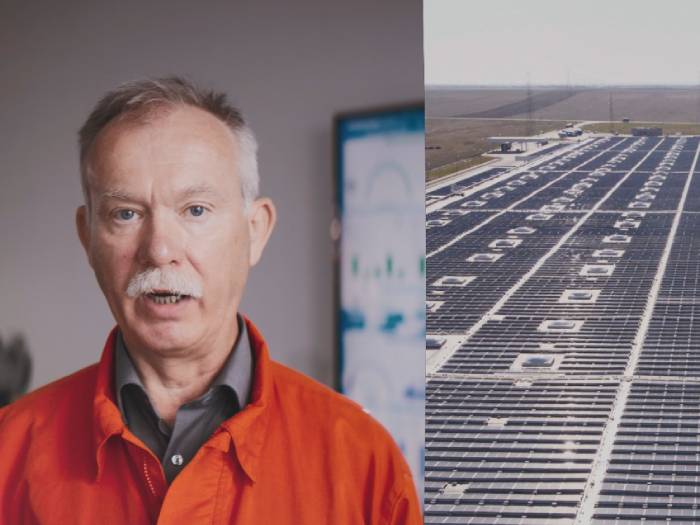
Zentai has not only been the driving force behind the installation of the Company's photovoltaic system, a rooftop solar park about the size of 22 football pitches, but together with his team introduced the use of geothermal energy: in 2015, a Hungarian specialist company drilled two production wells and two back-pressure wells of about 2,500 metres in depth near the plant. This is because close to Győr, deep underground, there is a source of thermal water with a temperature of around 100 degrees.
Thanks to this solution, geothermal energy not only covers 80% of the Audi plant's heating needs, through a heat exchanger system, but also supplies heat to part of the city of Győr. "Our geothermal system works with a closed underground water circulation system, so we don't pollute natural resources," Zentai further explains.
Zentai also pays attention to sustainability in his private life: when something at home breaks, he only gets rid of it if it cannot be repaired. “Perhaps it has something to do with an American Indian saying that sometimes springs to mind: we don't inherit the earth from our ancestors, we borrow it from our children”.
The Transparent Factory
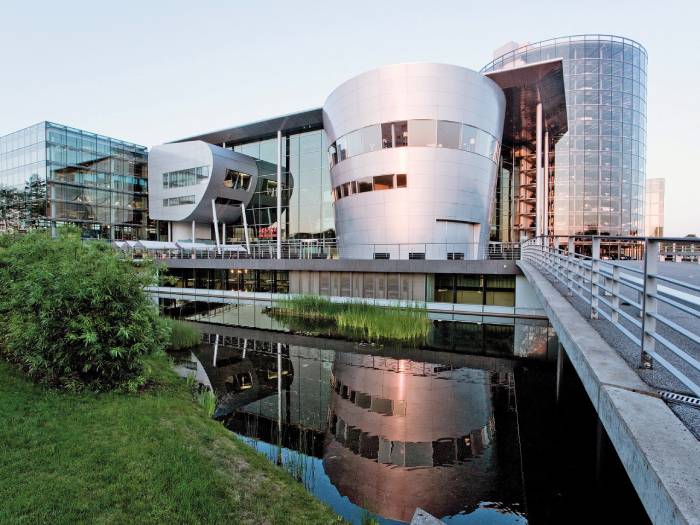
Petra Larin, on the other hand, works in the Transparent Factory in Dresden, which overlooks the Botanical Garden. “This proximity is already a good reason to make sustainability a priority”, she explains. The Dresden plant is one of the facilities where the Volkswagen ID.3 is produced and was one of the first factories in the Volkswagen Group to become carbon neutral. The Transparent Factory saves 3,600 tons of CO₂ per year just by using natural electricity from hydroelectric power. Since the plant was converted to e-mobility, all electric cars are recharged with energy generated by the facility's solar panels.
But sustainability also involves small contributions, such as flowering meadows, insect hotels and support for bird nesting. All these activities take place at the Transparent Factory, which since its foundation 20 years ago has always been a production site integrated as seamlessly as possible with the city centre. There are no fences or barriers, but plenty of vegetation and a façade that allows you to look inside.
Botanical garden
The outdoor area is characterised by flowers, ponds and hundreds of trees. “We collaborate with the botanical garden, to be symbiotic, and they help us select the most suitable plants”, Larin says.
In Petra Larin's home garden there are vegetables and wild flowers, but also deadwood that provides a habitat for insects, amphibians and reptiles. And when she's not out and about on her bike, she's driving a hybrid car: “Everyone can do their bit to help achieve the climate targets. We must ensure that the next generation has an environment worth living in”.
No waste in catering
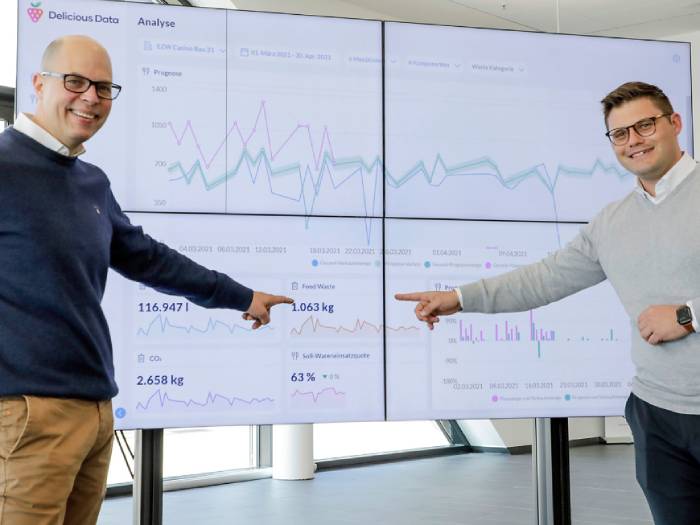
For a year now, Porsche has been using artificial intelligence to better plan the work of all 16 canteens in Germany, reducing food waste and potable water consumption. In detail, the artificial intelligence uses a deep learning algorithm to recommend the menu and portions that the catering in Weissach, Hemmingen and Rutesheim should offer. “The system takes into account various influencing factors, for example previous sales volumes, calendar data and meteorological data”, explains Patrick Gehe, Project Manager for Digitisation and New Technologies in the Human Resources department.
“With this planning process we can significantly reduce waste due to overproduction. Considering the 3.6 million meals served each year, the impact is huge”, adds Ulf Schnoor, Head of Catering in Weissach. Artificial intelligence also helps to offer a healthy and well-balanced menu.
Ever more powerful batteries

At Volkswagen Group Components' Salzgitter Centre of Excellence, chemist Tim Dagger is working on the development of ever more powerful batteries, as they are the key component of every electric car. Together with his colleagues, Dagger is improving the chemistry of lithium-ion cells.
“We are trying to develop a high-performance supercell that is inexpensive and produced in a sustainable way”, says Dagger, whose experience is particularly valuable given the transformation of the automotive industry and the conversion of entire plants to electric mobility. A process that requires engineers specialised in battery technology.
Carbon footprint
Dagger has been working with lithium-ion since 2012. “It's great to see how this technology is helping electric cars break into the mass market” says Dagger, pointing out that several scientific studies show that electric vehicles have the best carbon footprint compared to other drive technologies.
“Climate change is one of the biggest challenges of our time and slowing down global warming is a common responsibility”, adds the chemist. The Volkswagen Group is taking a holistic approach to this: decarbonising the entire company, recycling batteries and offering electricity from sustainable sources are concrete examples. “This is all about being future-oriented and sustainable, and I'm proud to be able to do my part”.
Source: Volkswagen AG
VGI | Responsible OU: VP | Creation date: article date | Class 9.1