E-mobility, formazione e sostenibilità : come cambia l’impianto di Emden
Lo stabilimento Volkswagen di Emden sta affrontando la più grande trasformazione della propria storia: la conversione alla produzione di auto elettriche, supportata da un investimento pari a un miliardo di Euro. Per la formazione dei collaboratori si usano anche metodi non convenzionali.
Obiettivo neutralità climatica
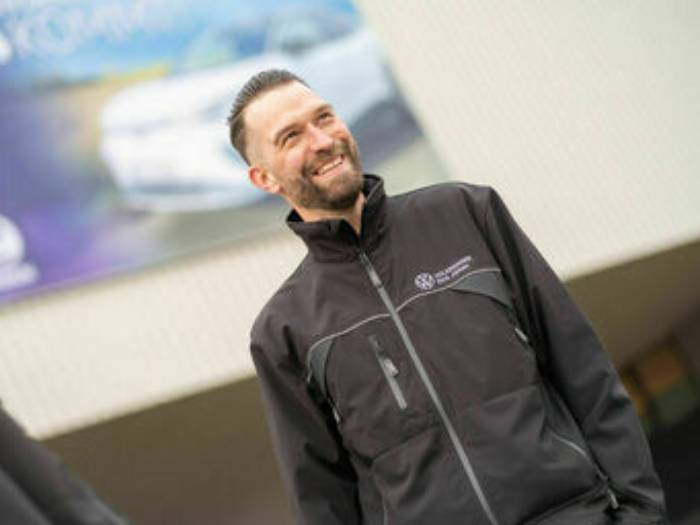
"La trasformazione e il passaggio alla mobilità elettrica sono molto importanti per Emden" spiega Dirk Jibben, portavoce del Team presso lo stabilimento Volkswagen di Emden. Volkswagen sta investendo un miliardo di Euro negli sviluppi e l'obiettivo è la produzione ecologica di auto elettriche sostenibili: un passo importante per l'azienda nel suo Way to ZERO, il percorso verso la neutralità climatica.
Nell’impianto di Emden sono stati avviati progetti concreti per raggiungere questo obiettivo, come l'utilizzo dell'energia geotermica a livello del suolo attraverso "pile di energia", il riscaldamento a risparmio energetico alimentato dal teleriscaldamento di una centrale a biomasse, l'uso di energia da fonti rinnovabili, pannelli fotovoltaici sul tetto e turbine eoliche nei locali della fabbrica. Inoltre l'iniziativa "no plastics" sta contribuendo a ridurre significativamente i rifiuti di plastica nella produzione: dallo scorso anno se ne sono risparmiati oltre 6 tonnellate.
Emden come progetto pilota per la mobilità elettrica
La decarbonizzazione del processo produttivo e della filiera sta andando di pari passo con il passaggio all’e-mobility. Emden è uno degli stabilimenti più moderni del settore automobilistico e un progetto faro per lo sviluppo della mobilità a zero emissioni. A partire dai prossimi mesi, la Volkswagen ID.4 sarà la prima auto elettrica prodotta nello stabilimento. L’anno prossimo sarà la volta della Aero B, un modello con dimensioni simili alla Passat, che uscirà dalla linea di produzione con motorizzazione 100% elettrica nelle versioni berlina e station wagon.
60.000 giornate di formazione per i collaboratori
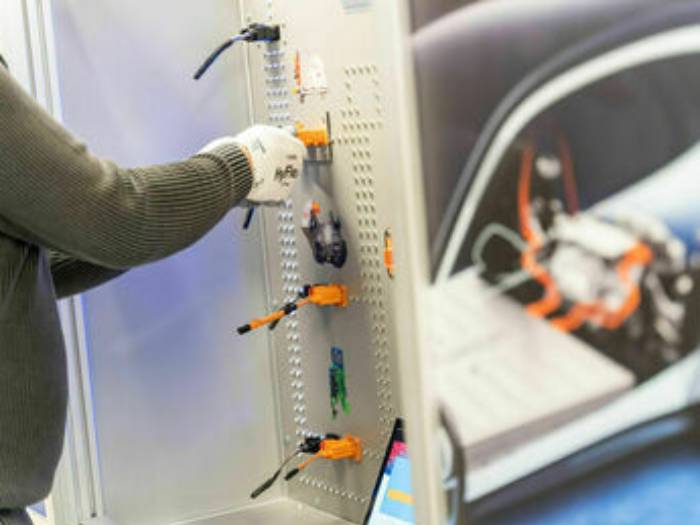
Quello in corso è il più grande processo di trasformazione della forza lavoro nella storia dello stabilimento. Prima dell’avvio della produzione i collaboratori avranno completato oltre 60.000 giornate di formazione, partendo dall’incremento delle conoscenze sull’elettromobilità e arrivando a corsi specifici sulla produzione dei futuri modelli a zero emissioni.
Per rendere possibile tutto questo sono state allestite diverse stazioni di formazione, oltre a una linea di produzione fissa dove è possibile imparare i nuovi gesti necessari per costruire un’auto elettrica. In particolare, la gestione delle parti e dei componenti dell'azionamento elettrico è una novità per gli addetti alla produzione: "L'intero cablaggio è diverso, ma questo è ciò che caratterizza un'auto elettrica" afferma Stephanie Lorenz, vice supervisore, mentre illustra i nuovi processi.
Per rendere più efficace la formazione, sono state predisposte pareti con connettori di diverso colore, su cui il formatore usa molti gesti per spiegare le differenze tra i vari componenti: prende la spina giusta e la inserisce nel connettore, facendo così illuminare tre luci verdi che confermato la correttezza dell’operazione. La formazione però non si occupa esclusivamente dei componenti specifici e del loro utilizzo, ma anche di tutte le attività correlate.
Addio alle sale conferenza
La formazione nell’impianto tedesco comporta anche attività divertenti, come quelle organizzate nelle “escape room”. Una squadra deve lavorare insieme e scoprire indizi, risolvere enigmi e completare compiti per raggiungere un obiettivo entro un tempo prestabilito. A Emden ci sono tre stanze che trattano argomenti diversi. I partecipanti imparano molto sull'elettrificazione, così come sul modello e sulla storia della Volkswagen.
"L'escape room nel centro di formazione è divertente" afferma Lorenz. "Prima bisogna orientarsi, ma è così che si impara ancora di più sulla storia dell'azienda: come è iniziata e si è sviluppata, il modello con cui abbiamo cominciato e dove siamo oggi". Dirk Jibben è stato immediatamente colpito da questa proposta fuori dagli schemi. “Sono stato una delle prime persone a provare l'escape room. Nessuno mi aveva anticipato nulla e quando sono entrato sono rimasto a bocca aperta. È stato davvero bello".
L’importanza del gioco di squadra
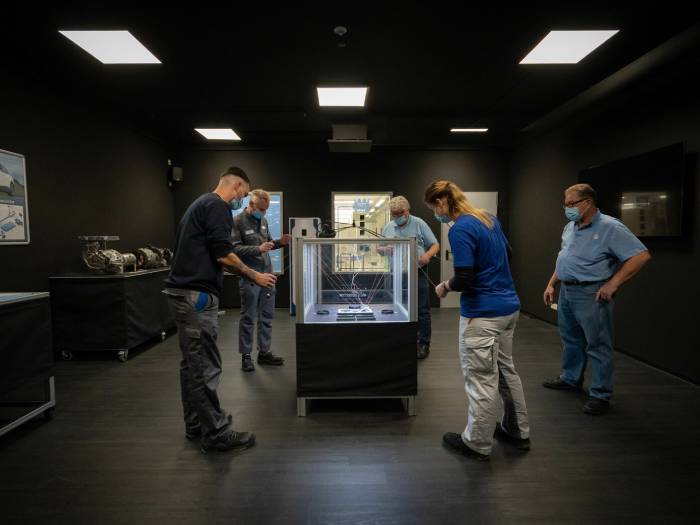
Il team building è l'aspetto fondamentale: quattro persone si allineano ai lati opposti di una scatola di plexiglass. Usando dei fili, tengono e bilanciano un magnete che, come una squadra, devono usare per mettere insieme sette pezzi di un puzzle. Pazienza, coordinamento e collaborazione sono all'ordine del giorno qui. Jibben prende il comando e dà consigli su chi deve tirare o lasciare. Dopo un breve momento di familiarizzazione, il team inizia a lavorare all'unisono e risolve con successo il compito. "Usare l'escape room per dimostrare che è necessario lavorare insieme come una squadra per avanzare con successo è un'idea davvero interessante" commenta Jibben.
Il programma formativo, ovviamente, non si limita all'escape room. Una parte è dedicata alla conversione dello stabilimento, partita nel novembre 2018 e con i primi progetti già completati. La nuova area di assemblaggio, in costruzione da ottobre 2020, è centrale per la futura produzione di auto elettriche: ha le dimensioni di otto campi da calcio ed è dotata di un efficiente impianto di illuminazione a LED che emula la luce naturale. Grazie alla moderna tecnologia di trasporto, alle postazioni di lavoro ergonomiche e ai processi di produzione completamente automatizzati, la sala di montaggio è l'esempio di una produzione automobilistica visionaria e sostenibile.
Stretta collaborazione con l’impianto di Zwickau
“Veniamo dal mondo dei motori a combustione e non abbiamo ancora esperienza nella produzione di auto elettriche; in questo stabilimento abbiamo prodotto modelli ibridi. Ecco perché l'interazione con Zwickau era e rimane incredibilmente importante" sottolinea Jibben. Il trasferimento di know-how dall’impianto di Zwickau, gli strumenti di formazione creativa e il processo di apprendimento nella linea di produzione sono “l’ossatura di base” per la trasformazione a Emden.
Fonte: Volkswagen - Shaping Mobility Hub
VGI | U.O. Responsabile: VP | Data di creazione: data dell’articolo | Classe 9.1