Volkswagen ID.3: carbon neutral e-mobility becomes reality
The ID.31 marks the beginning of a new era for the Volkswagen Group - also in the field of sustainability.
The Volkswagen ID.3 is the Group’s first carbon neutral certified vehicle - in other words the global impact of its CO₂ emissions is equal to zero. This has been made possible through a comprehensive sustainable strategy.
The Volkswagen Group is aware of its responsibility to the environment and society, and has committed itself to a programme of decarbonisation with the aim of reaching balance sheet CO₂ neutrality by 2050. One way of meeting the target is electrifying the brands’ vehicle fleets. And the ID.3 is Volkswagen’s first model to follow this strategy.
Three fundamental principles
The Group is pursuing three fundamental principles in order to achieve the best possible carbon neutral balance sheet. First: reduce CO2 effectively and sustainably. Second: convert the energy supply to renewable energies. Third: compensate for unavoidable emissions through climate protection projects.
The life cycle
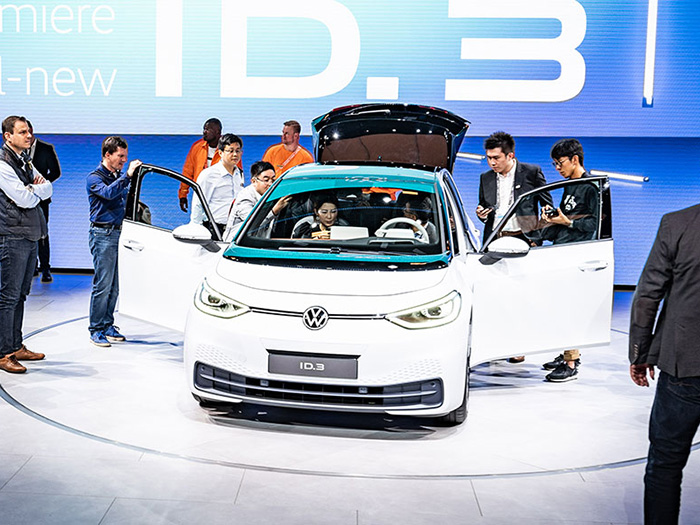
To ensure that sustainability really makes sense, carbon neutrality must apply over the entire life cycle of a vehicle. Experts refer to this as the Life Cycle Assessment (LCA), a standardised analysis using ISO guidelines, of the environmental impact of a car’s production and entire life span. It divides this into four sections. First, the supply chain; second, production, where processes that generate high levels of CO₂ are defined as “hot spots”; third, the use phase; and fourth, recycling, which takes place at the end of a vehicle’s life span.
Sustainable mobility is complex and, to achieve it, holistic thinking is imperative. With the ID.3, the manufacture of the battery system causes over 40% of CO₂ emissions during the production phase. The ID.3 battery is a component that Volkswagen does not manufacture itself. Therefore, the Volkswagen experts examine the supply chain, in particular the production of components and the extraction of the raw materials.
Battery production
The production of batteries is energy intensive. This is why the production of an electric car produces significantly more CO₂ than a vehicle with a classic petrol or diesel engine – on average 1.5 times more. In other words, electric cars have a disadvantage in their CO₂ balance right from the outset and consistent climate protection must therefore start early.
If, for example, green electricity is used to manufacture the batteries, the environmental impact drops significantly. The battery cells for ID.3, for example, are supplied by LG Chem, which manufactures the cells in Poland using only certified green electricity. CO2 emissions from this phase are thus reduced to almost zero.
Steel and electric motors
Steel production and the manufacture of electric motors are also focal points for CO₂. In the case of steel, complex processes could lead to emissions savings of 70% within a few years. In the case of the electric motor, Volkswagen uses recycled aluminium for the housing in which the batteries are placed. The savings potential of this and other measures that reduce CO₂ emissions is up to 50%.
Of course, CO₂ is also produced in the production of components, body construction, the paint shop and part assembly. The ID.3 is manufactured at Volkswagen’s ultra-modern Zwickau plant. The plant is increasing its capacity to be able to produce 330,000 purely electric cars a year from 2021.
Zwickau - a cutting edge plant

The plant in Zwickau has a history of sustainability. As of mid-2019, it had already reduced CO2 emissions by a total of 66% compared with 2010, partly due to the use of green electricity from hydropower, wind and solar sources. It produces the rest of its energy in its own thermal power station. It is powered by natural gas, which covers 70% of the entire plant’s heat requirements.
CO₂ emissions were also reduced during the construction of new buildings and restructuring work on existing buildings, in accordance with the latest energy saving directives.
Emission compensation
CO₂ emissions that cannot be avoided in production are compensated by climate protection projects. Volkswagen Group is initially concentrating on forest protection and reforestation in the tropics. The projects are certified to the highest international standards: the Verified Carbon Standard (VCS), the Climate Community and Biodiversity Standard (CCB) and Gold Standard.
With the first project, the “Katingan Mataya Forest Protection Project” in Borneo, the company is offsetting the currently unavoidable CO₂ emissions generated by ID.3 before it is delivered to customers. This, then, is how the ID.3 will be balance-sheet CO₂-neutral. However, in order to maintain this, the battery must be consistently charged with renewable electricity. Sustainability also means durability - ID.3 batteries will be guaranteed for eight years or 160,000 kilometres.
Charging with green electricity and recycling
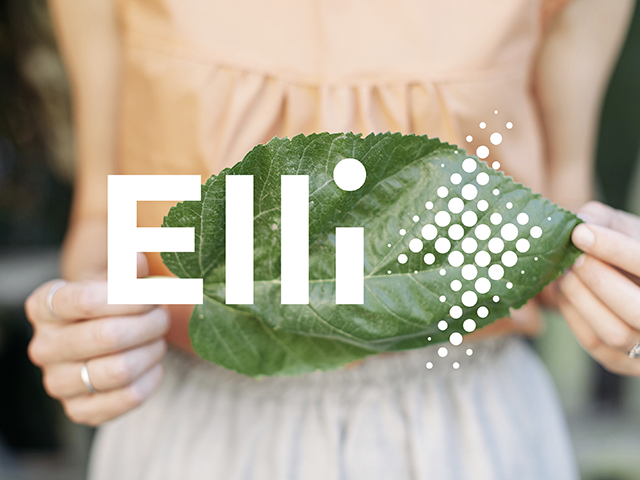
The Volkswagen Group subsidiary Elli, which specialises in supplying green energy, will support ID.3 owners by installing a recharging point at home or at their workplace. On the road, drivers can use the ultra-fast Ionity charging infrastructure. By 2020, Ionity will have built 400 charging stations along Europe’s main traffic arteries, offering renewable electricity.
At the end of the vehicle’s life cycle there is recycling. Volkswagen Group is also committed to this field through the LithoRec research project, launched in 2009. The aim is to further reduce the carbon footprint of battery production through the use of recovered raw materials. To this end, a pilot recycling plant for lithium-ion batteries is currently being built at Volkswagen’s Salzgitter plant. Volkswagen is also working on ways of reusing vehicle batteries in stationary applications that do not require the same performance levels in terms of temperature stability and energy transfer as a car. This will also ultimately improve the vehicle’s CO2 balance.
1 The vehicle is not yet offered for sale
Source: Volkswagen AG