Reusing raw materials: ŠKODA’s commitment to the circular economy
ŠKODA is working systematically to develop a circular economy, and is constantly looking for innovative ways to put valuable raw materials back into the production process.
At ŠKODA, the circular economy follows four key principles: minimising the impact on the environment, reducing the resources used and the loss of these resources, while maximising their circulation.
An interdisciplinary team, coordinated by the Ecology and Occupational Protection department, has the mission of seeking out new opportunities and methods for the implementation of these principles. “We are introducing measures that make sense both in terms of environmental protection and efficient use of resources and in financial terms,” says Lenka Bočková, head of the unit.
Maintenance of hydraulic machines
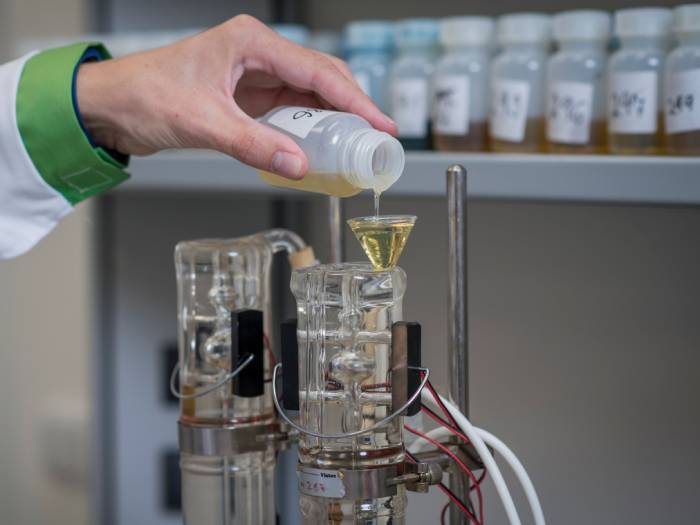
The circular economy has found an application in the maintenance of hydraulic machines, for example, for which the condition of the lubricants is constantly monitored in real time. The oils themselves are analysed by the Central Technical Service in the FabLab, ŠKODA’s innovation laboratory. The result of this is that the lubricants’ life spans have been extended and the frequency of machine breakdowns has been reduced.
Last year alone, for example, they filtered more than 100,000 litres of oil, with savings of around 200,000 Euros on lubricant costs, without taking into account the greater reliability of the production line, which has needed fewer spare parts and has had less downtime.
Working together with suppliers
ŠKODA is involving the entire supply chain in discussions around the issue of the circular economy. For this reason, the company has kick-started a series of meetings, always focused on a specific topic: the first two have dealt with specific materials – glass and rubber – and have led to a number of pilot projects.
Some of the projects which stand out include training for the dealer network with regard to the circular management of end-of-life car glass and its reuse in the glass industry, and increasing the use of shards of primary glass in the production of new car windows and windscreens.
Recycled plastic
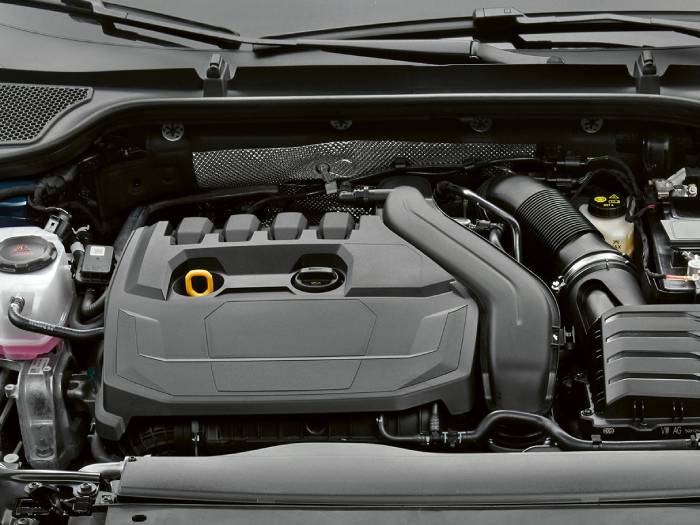
ŠKODA vehicles contain numerous plastic parts made from recycled plastics taken from end-of-life vehicles or sub-standard parts of dashboards, bumpers etc. that are generated during production.
Certain parts are made with 100% recycled materials, while others combine them with virgin materials. In some models, the exterior covers for the chassis, the wheel arches and the water drainage channel under the windscreen are made from recycled plastic: these components are manufactured using recycled materials taken from the battery covers of used vehicles. But recycled plastic, in this case from bottles, is also found in the mats and carpets, in the boot liner and in various other details.
Technical Development specialists are also experimenting with the use of fibres extracted from unused parts of coconuts, flax, beets and coffee grounds as a filler for plastics. The overriding objective in all this is to conserve natural resources and make use of waste material.
Saving water and energy
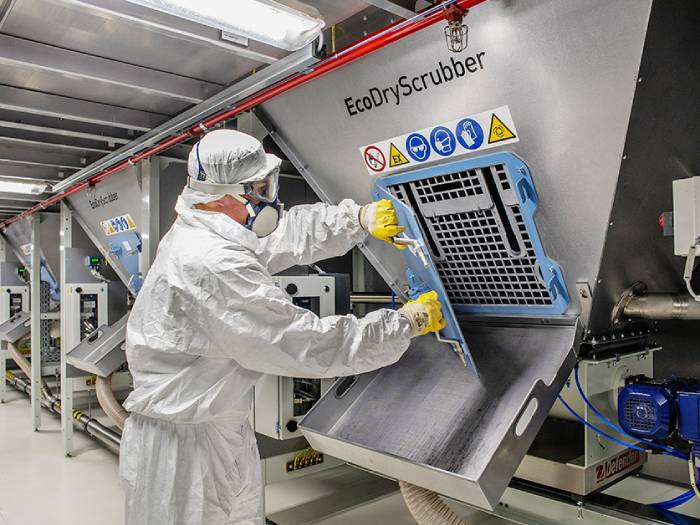
Ground limestone, which absorbs residual paint particles by means of a process known as dry separation, has proved particularly useful in the paint shop. “No water is used in this method: air containing ground limestone circulates in the system, capturing paint and varnish particles. At the same time, only 20% “fresh” air is supplied, allowing for energy savings of 80% in cleaning the air required for the paint shop’s operation," explains Veronika Nýdrová, from Paint Shop Process Planning. What’s more, once the ground limestone is saturated with paint, it is used again in another process called flue gas desulphurisation in the ŠKO-ENERGO heating plant.
The circular economy for used oils
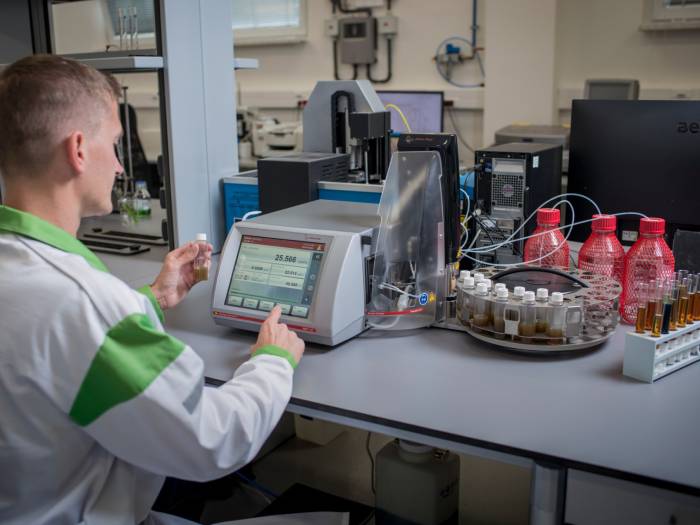
Another example of a circular economy project is co-operation between the Technical Development department and the recycling company Praktik or granulate manufacturers. The goal is to develop useful materials from used bumpers, or to come up with ideas for reusing engine oil or brake fluid.
“We are also currently working on chemical recycling, which can use a thermal process to turn old plastic into virgin-quality material,” says Lukáš Zuzánek from the Corrosion, Weather Resilience and Material Development department. There are many concrete examples of the application of circular economy principles at ŠKODA, from increasing the proportion of recycled materials and reusing packaging in logistics, to innovative technical solutions in manufacturing.
ŠKODA Green Week
ŠKODA has been setting out its strategy, objectives and position on sustainability and decarbonisation to its employees as part of GreenWeek, an event in which a whole working week is devoted to talks and workshops on issues that underpin the company’s entire future and strategy. The event, for which the main topic this year is circular economy, was held online, allowing all employees to participate, and is tied in with the Volkswagen Group’s goTOzero week.
Source: ŠKODA
VGI | Responsible OU: VP | Creation date: article date | Class 9.1