Reduce, convert and compensate: the strategy towards the carbon neutrality
Volkswagen Group is pursuing the goal of becoming balance sheet CO₂-neutral by 2050, in all of its activities. Here is what the Group is already doing to reduce its carbon footprint.
Climate protection is one of the greatest global challenges facing mankind. At the 2015 World Climate Conference in Paris, 197 countries committed themselves to limiting global warming to well below two degrees compared with the pre-industrial age – and thus to continuously reducing emissions of the greenhouse gas carbon dioxide (CO₂), which is mainly responsible for the rise in temperatures.
The Volkswagen Group is committed to the Paris Agreement and has developed a decarbonisation program for this purpose, which is currently being implemented. By 2025, the company aims to reduce the carbon footprint of cars and light-commercial vehicles across the entire value chain by 30 percent compared to 2015 – and by 2050 to make the entire Group’s balance sheet CO₂ neutral. The goal: A green zero.
Three-level hierarchy
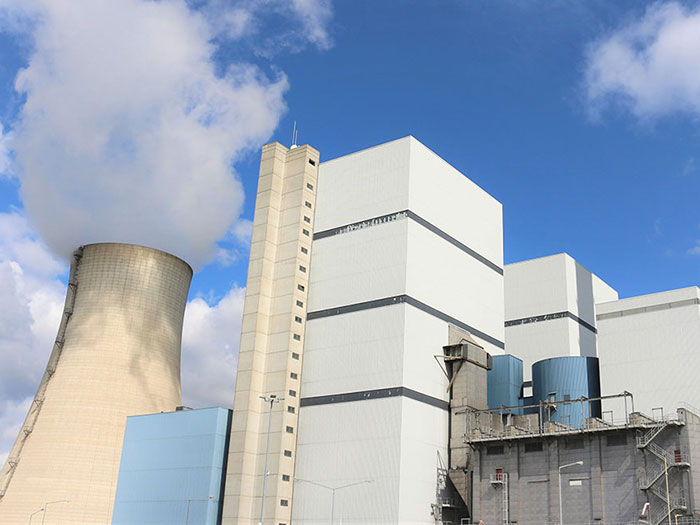
All measures follow a three-level hierarchy, corresponding to three keywords: reduce, convert and compensate. First and foremost are actions to avoid or reduce CO₂ emissions during production. In the second phase, the energy supply in the entire value chain is converted to less CO₂-intensive or renewable energy. Finally, unavoidable CO₂ emissions across the Group are offset through climate protection projects that meet the highest international standards.
Volkswagen Group’s focus is on switching to electric mobility as the best and most efficient way of creating climate-friendly mobility. Another key element is the complete analysis and recording of CO₂ emissions at all stages within the automotive value chain. This means recording the entire life cycle of a vehicle – from the extraction of the necessary raw materials, through to the production-and-use, right up to the recycling stage.
ID.3 production in Zwickau
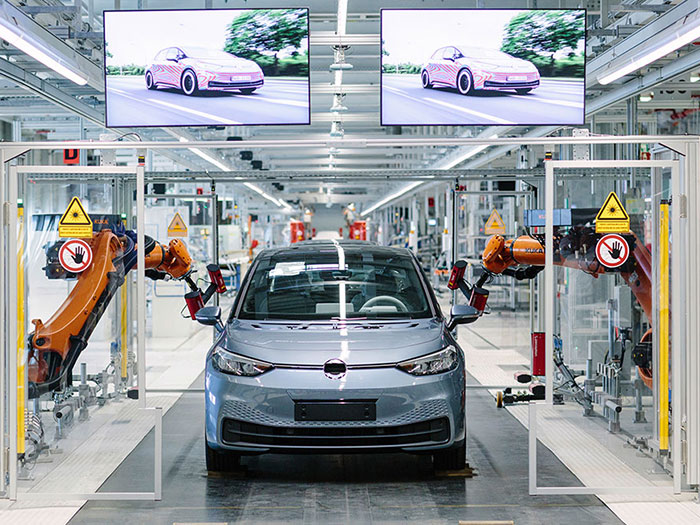
The ID.31 has been rolling off the production line at the Volkswagen Zwickau plant, in Germany, since November 4, 2019. The facility will be converted into the largest, most efficient and environmentally friendly electric car production plant in Europe. A key focus will be on reducing CO₂ emissions. One way this will be achieved is through consuming green electricity from renewable sources supplied by Volkswagen Kraftwerk GmbH. Thanks to pure natural electricity from hydroelectric power plants, wind farms and solar parks, CO2 emissions can be reduced by 106,000 tons per year.
In addition, the Zwickau location relies on energy efficiency measures for new buildings in order to minimise the consumption of electricity, water and heat. This reduces the plant’s electricity consumption by 20 percent. Another energy efficiency measure is thermal post-combustion in the paint shop, which uses less gas. In addition, there are frequency-controlled fans and pumps as well as the use of energy-optimised compressed air systems.
Farewell to coal
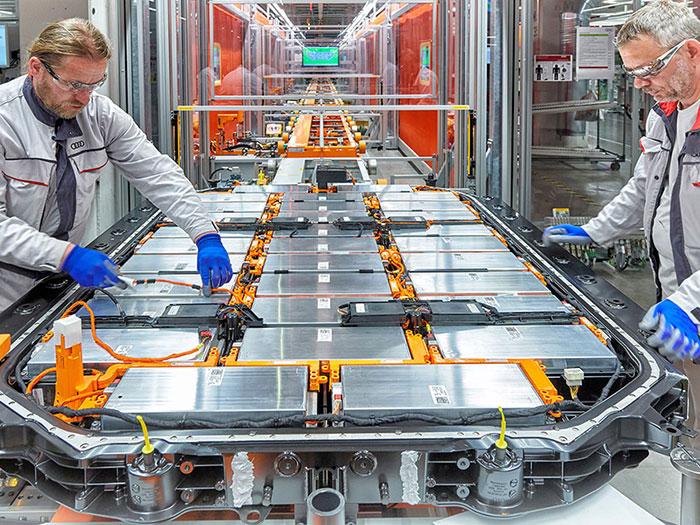
In Wolfsburg, coal will soon be a thing of the past. At a cost of around 400 million euros, the two power stations will be completely converted from coal to natural gas. With a 33 percent increase in energy efficiency, the CO₂ emissions of the two power plants will be reduced by around 1.5 million tons per year. This corresponds to the annual CO₂ emissions of currently approx. 870,000 vehicles and is a decrease of almost 60 percent compared to the previous emissions of the power plants.
The modernisation will reduce the CO2 emissions of the German production sites (Brunswick, Emden, Hanover, Kassel, Salzgitter, Wolfsburg) by around 50 percent and for Volkswagen Group’s production sites worldwide by around 15 percent. Water consumption and waste generation will also be drastically reduced – by an average of around 50 percent. By 2025, the CO2 emissions of all plants are to be reduced by half compared with 2010. Audi’s production facilities in Brussels, for example, are already completely CO2-neutral.
Sustainable plants
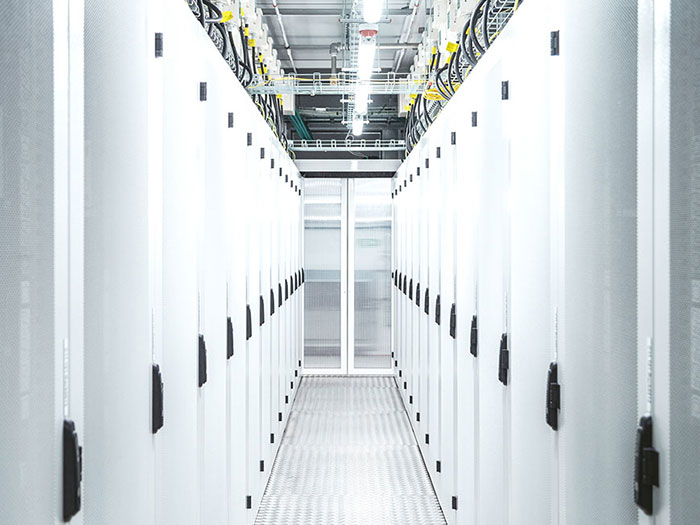
Another practical example is the production of lithium-ion batteries for electric cars - a very energy intensive process. As part of its decarbonisation programme, Volkswagen Group has therefore agreed with the supplier LG Chem that only certified green electricity will be used in battery production at its site in Poland. This significantly reduces CO₂ emissions in battery production to almost zero, and for the entire production process by up to 80 percent.
Meanwhile in Norway, the Volkswagen Group has built, in just six months, a new, climate-neutral data centre in Rjukan, near Oslo, which operates 100 percent on hydroelectric power. The Volkswagen and Audi brands will use the data centre for high-performance servers to develop their most innovative projects. These halls are supplied with up to 2,750 kilowatts of power, which can save more than 5,800 tons of CO₂ per year compared to a conventionally operated data centre. The Group also operates a climate-neutral data centre in Iceland which saves around 6,200 tons of CO₂ annually.
Offsetting CO₂ emissions
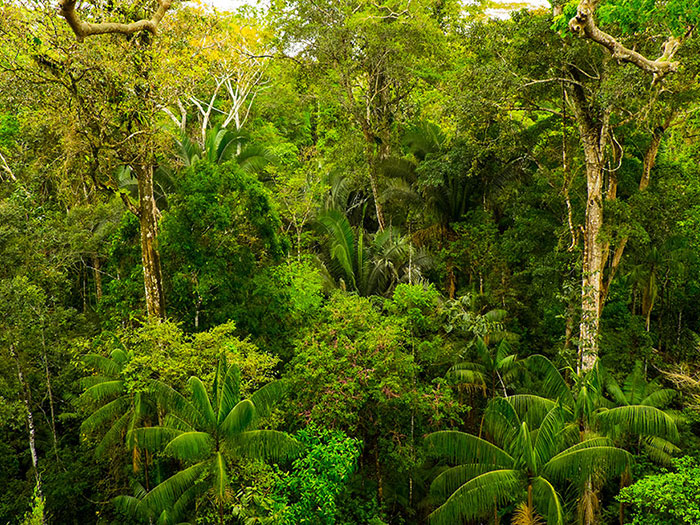
As mentioned, Volkswagen Group wants to reduce CO₂ emissions uniformly and over the entire life cycle of every vehicle. But not all CO₂ emissions can be avoided in advance. For this reason, Volkswagen Group is offsetting the currently unavoidable CO₂ emissions from the production phases of the ID.3 so that the vehicle can be handed over to customers in a balance sheet CO₂-neutral manner.
The Katingan Mentaya project is the world’s largest forestry protection project. The project is located in central Kalimantan on the island of Borneo and protects a 149,800-hectare forest on carbon-rich peat soils against deforestation, converting it into economically useful plantation areas. These areas extract CO₂ from the atmosphere, bind the carbon they contain and produce oxygen. Above all, the peat sponge, which is widespread in this region, retains an above-average amount of carbon.
How CO₂ credits work
Organizations and companies such as the Volkswagen Group acquire credits, so-called Verified Carbon Units (VCU). Each VCU represents one ton of CO₂, which does not escape into the atmosphere thanks to avoidable deforestation. With around 7.5 million VCUs awarded annually, the Katingan Mentaya project is the largest of its kind. In total, the project has already committed a greenhouse gas equivalent of over 30 million tons.
The project works closely with surrounding village communities to improve their living conditions and contribute to local sustainable development – including the provision of microfinance credits, support in the areas of education and health and direct employment in the forest fire response teams. The project also protects a habitat of high conservation value and a vibrant mix of species.
1 The vehicle is not yet offered for sale
Source: Volkswagen AG