How to become carbon neutral? The example of the Å KODA plant in VrchlabÃ
In Vrchlabí, CO2 emissions have been reduced from 45,000 to 3,000 tonnes per year, the latter are offset through specific projects. This was achieved mainly through the switch to renewable energy, and the other ŠKODA production plants are also preparing to become carbon neutral. Let's see how.
As part of the Volkswagen Group's roadmap for sustainability and decarbonisation, a few months ago ŠKODA announced its intention to make all its plants in the Czech Republic carbon neutral. The Vrchlabí plant was the first to achieve this goal, at the end of 2020. It was a complex process, involving all areas of the plant, with a focus on switching to electricity from renewable sources.
"In 2020, over 90% of the electricity used at Vrchlabí came from renewable sources. If we had used conventional energy sources, we would have emitted 45,000 tonnes of CO2, whereas this way we have reduced it to less than 3,000 tonnes" calculates Pavel Grmela, project coordinator of the Ecology and Occupational Protection section.
Being carbon neutral and saving energy
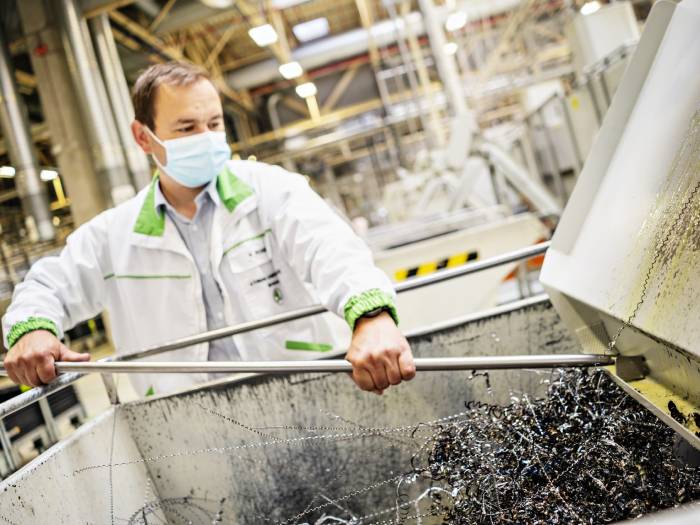
Declaring carbon neutrality is, of course, a matter of complete transparency, which is why ŠKODA demands the necessary certificates of origin for the electricity it buys, so it can be certain that it comes from renewable sources. In any case, the first step to becoming carbon neutral is to save energy and, to this end, around twenty different energy-saving measures have been implemented in 2020. These include the introduction of a particularly efficient energy management system, the optimisation of temperature control systems - ventilation and air conditioning - the closing of unused heating circuits and the replacement or intelligent regulation of lighting.
In 2020 alone, careful management of energy consumption led to savings of more than 2,000 MWh of heat energy and almost 1,500 MWh of electricity, the equivalent of the annual consumption of around 1,000 households. "The cleanest energy is the one that doesn't have to be generated" explains Grmela.
Offsetting emissions
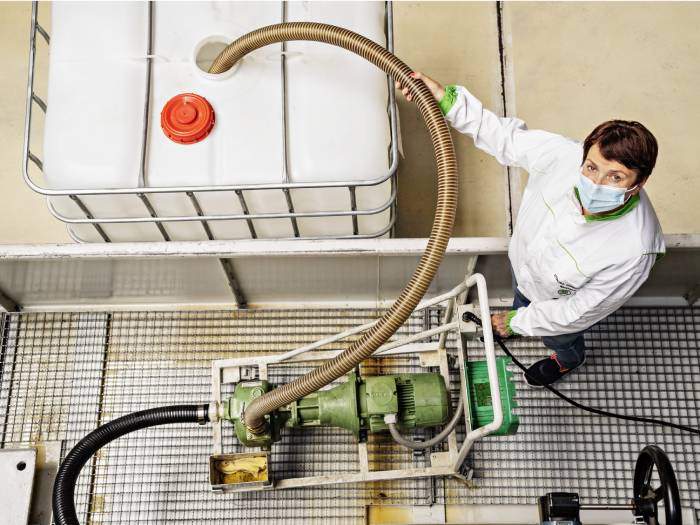
To address the currently unavoidable CO2 emissions, ŠKODA has purchased offset credits. "In 2020 we offset combustion of natural gas, which was no longer necessary in 2021 because we switched to bio-methane. We are now working on emissions from coolants and company cars. We will continue to study and adopt new measures," adds Grmela, who goes on to explain how part of the offsetting for the Vrchlabí plant comes from the purchase of credits from two wind farm projects in Asia.
Local projects
"Other activities include cooperation with the Krkonoše National Park, planting programmes - for example, 40,000 trees were planted in the vicinity of the plant in 2020 - and biodiversity protection projects" says Jiří Svatý, Technical Services Coordinator at the Vrchlabí plant.
Activities which, since they are not certified, do not contribute to improving the CO2 balance, but demonstrate ŠKODA's attention to these issues. The goal of making all plants carbon neutral by 2030 is realistic.
Biomethane and biomass
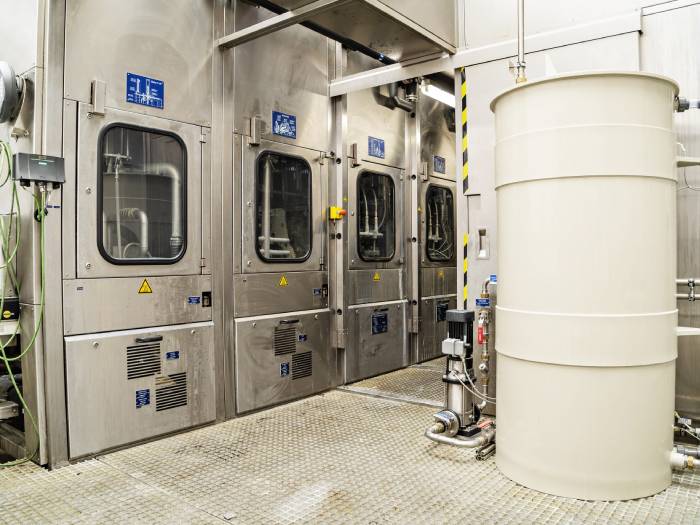
The switch from natural gas to bio-methane is an important issue, as it will bring emissions from everything that runs on gas, such as the cogeneration units in Vrchlabí and Kvasiny, to zero. In Mladá Boleslav, on the other hand, the exclusive use of biomass - which today is burnt together with brown coal - will be implemented by the end of 2025. "With this development we will move closer to neutrality in terms of energy generation for the entire company," concludes Pavel Grmela.
The Vrchlabí plant
The Vrchlabí site has been in operation since 1946 and in 2012 it was converted into a state-of-the-art components production plant. Today, around 1,000 employees produce every day around 2,300 DQ 200 dual-clutch direct-shift automatic transmissions (DSG): 38% are used in ŠKODA vehicles, 62% by other Volkswagen Group brands. Total production exceeded three million units already in 2019.
The plant uses the principles of Industry 4.0: for example, a very delicate process such as inserting the gear-shift pistons is handled with the help of a robot. There is also a robot that delivers components and takes empty packaging back to the warehouse, and another capable of autonomous transport. Among the innovative solutions implemented are a so-called 'digital twin' of the production line, which is useful for its optimisation, and other artificial intelligence systems.
Source: ŠKODA
VGI | Responsible OU: VP | Creation date: article date | Class 9.1