Good for the Environment – and for the Balance Sheet
The Volkswagen brand is preparing for the challenges of the next few years: new forms of mobility, electric cars, increasingly digitalized and connected models and a more sustainable production.
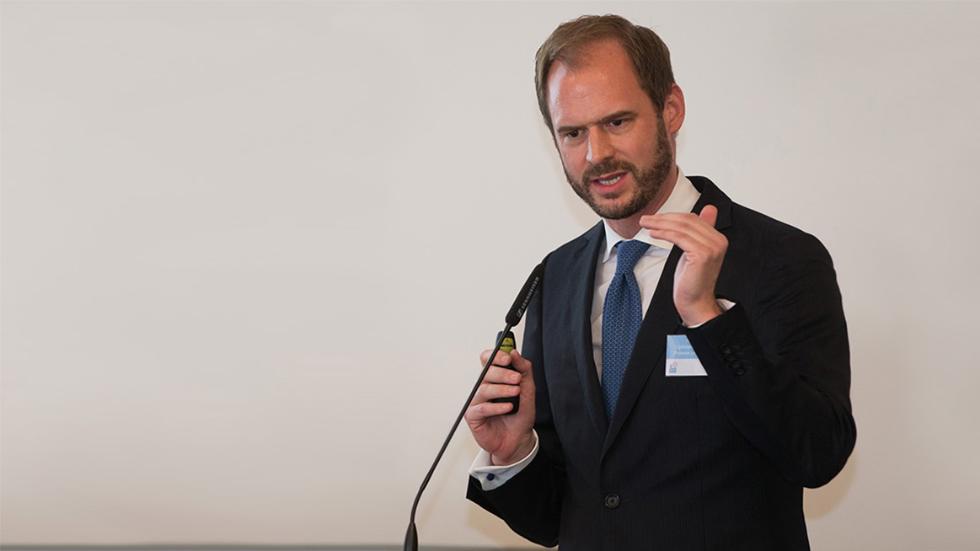
Volkswagen is in a process of transformation. And to master the challenges of the immediate future small changes will not be enough. “The transformation of the Volkswagen brand will be more far-reaching than ever before”, says Peter Bosch, Head of Strategy, Processes and Structures in Production and Logistics. The transformation will be especially conspicuous in this area.
Behind the scenes
To identify the changes, you need to visit the plants. We take a look behind the scenes at Wolfsburg, the Group’s most traditional plant. Here, at Europe’s largest car factory with about 61,000 employees, up to 3,600 Golf, Tiguan and Touran vehicles roll off the production lines every day. Thousands of components which are delivered to other plants within the Group are also manufactured here. Like all other Volkswagen locations, Wolfsburg also needs to improve productivity still further. This is a key element in the “pact for the future” and the TRANSFORM.FACTORY+ program, which Volkswagen has adopted to master the major challenges of the future.
Leadership in the production of electric cars
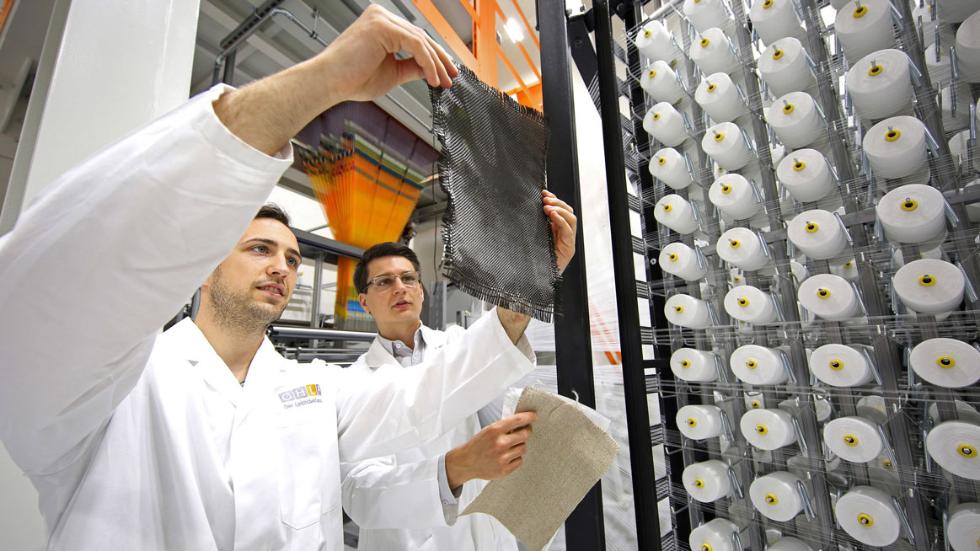
In vehicle production, the ambitious target which has been set is that the Volkswagen brand should have the world’s best electric car factories in a few years’ time. To date, manufacturers from Japan and the USA have been in the lead in this area. By 2025 at the latest, Volkswagen plans to have overtaken them. And by 2030 the brand intends to achieve another major goal: making production fully digitally networked throughout the world.
Redesigning the production process to drive further growth
At the same time, the production of current models is to continue. In order to master this double challenge, fundamental changes in production are planned. The Volkswagen brand intends to save more than €1 billion per year in vehicle assembly alone and productivity is to increase by 25 percent by 2020 compared with 2015. At the same time, production is to become more sustainable, not only in economic but also in environmental and social terms.
Environmental protection has the same priority as quality, efficiency and innovative power
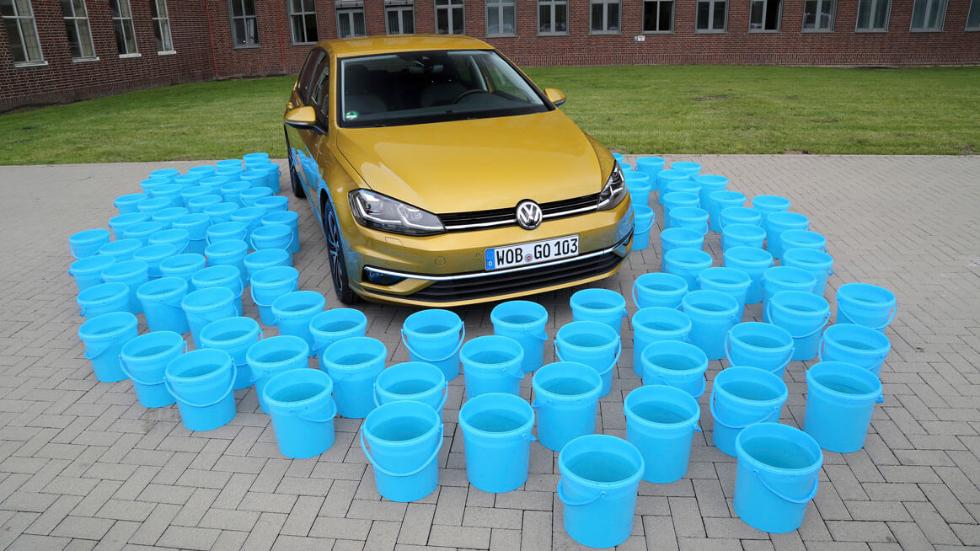
In 2015, the brand already reached the goal it had set itself of making the production of cars and components 25 percent more environmentally compatible than in 2010. And thanks to targeted investments in environmental technologies it has been able to save more than €130 million every year since 2010. Now it has staked out even more ambitious targets: by 2025, energy consumption, CO2 emissions, water consumption, waste production and solvent emissions per vehicle are to be 45 percent lower than the figures for 2010.
The program that is to achieve these objectives is called Think Blue. Factory, an extension of the Think Blue philosophy applied specifically to the entire production process with the aim of making it sustainable in every aspect. After all, concludes Peter Bosch, “the investments in environmental technologies conserve valuable resources and also pay their way directly”.
Source: Volkswagen AG
e-Golf: Consumption Electric power in kWh/100km: 12.7 (Combined) CO2 emissions, g/km: 0 (combined) Efficiency Class: A+. Passat GTE - Fuel consumption in l/100 km: combined 1.8 – 1.7; power consumption in kWh/100 km: combined 13.1 -12.5; CO2 emissions combined in g/km: 40-38; efficiency class: A+.