The factories of the future: e-mobility and digitization
Electric mobility and digitization are two key factors for the evolution of production plants. How will factories change over the next years? What benefits will customers have? Martin Goede, Head of Technology Planning and Development for the Volkswagen brand, gives us some answers.
In the past, the primary goal was optimisation. So we have automated many processes, improved the availability of facilities and boosted productivity over the last decade. One good example of this approach is the system to manufacture cars like the Golf on the basis of the Modular Transverse Toolkit. Significant improvements, but many are not visible. A layperson would hardly notice them. However things will be different in the future because factories are about to undergo dramatic, and noticeable, changes.
The reasons behind the changes
“There are two important reasons for this”, explains Martin Goede, Head of Technology Planning and Development for the Volkswagen brand. “The first is that the fundamental architecture of our products is changing. You see it in areas like the I.D. family, which is built on the basis of the Modular Electric Drive Matrix. In addition, vehicle electronics will become significantly more complex as a result of new assistant systems, new safety systems, autonomous driving functions and infotainment. We will include certain functions in vehicles by default, but we will activate them only on demand, that is, if the customer wants to use them. The second key reason for the change: production itself is becoming increasingly digital”.
With regard to the factories of the future, Goede has a highly detailed scenario in mind: “In ten years’ time, production plants will be heavily automated and highly networked. We will see growing numbers of robots working with humans without any protective fencing. Smart tools like smart glasses and smart watches will become normal parts of the workforce. Components made by 3D printers will be delivered directly to the production line. We will also visualise more and more processes on monitors so that employees can see at a glance whether the production operation is running smoothly”.
The “thrust” of e-mobility
Electric mobility will play a key role in this transformation. “By 2025, the brands of the Volkswagen Group will have introduced 80 new electric models as part of Roadmap E. This will be a tremendous opportunity as well as a huge job for production”, Goede continues. “We will set up new supply chains. Our work with high voltage batteries will also create new requirements. At the same time, our production lines will shorten because the drive train for electric vehicles is much less complicated than the one used in the internal combustion engine”.
Advantages for employees and customers
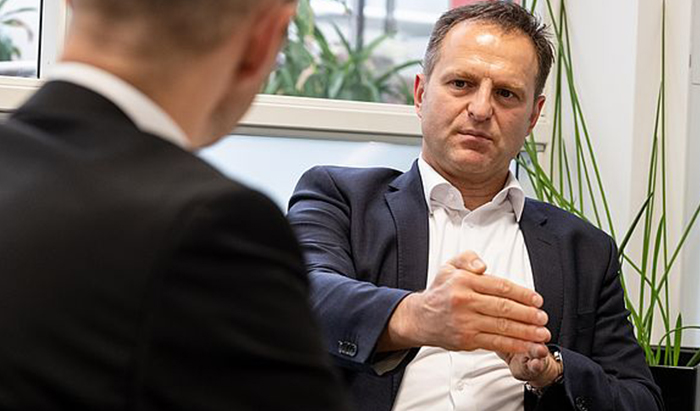
This evolution of the production processes will provide benefits both to workers and customers. “People will keep on being responsible and in charge of the situation. Machines and automated processes will boost efficiency and simplify worker’s lives. Many robots will take over the physically demanding jobs. This change will be particularly important because the average age of the workforce is increasing. What employees need is the willingness to use the new technical solutions”.
Digitization will have great impact, particularly for production times, as Goede confirms. “We will be able to use our data to better anticipate the type of cars that our customers will order, and thereby lower our production times. Our long-range goal: a new car should be ready one week after it was ordered. Another benefit is increased transparency: our customers will be able to digitally track their car as it is made. And they will also be able to change the configuration of the vehicle between order and production. For example, the colour of the car: suppose you change your mind after placing the order. As long as the car has not been manufactured yet, it will be possible to change it. You can’t do things like that today”.
Source: TOGETHER.net – Volkswagen AG