Supermarket 2.0: an innovation leap in logistics
Logistics employees used to have to cover large distances to pick components. Now, with the new system developed by Audi, the parts required for production come directly to the employees.
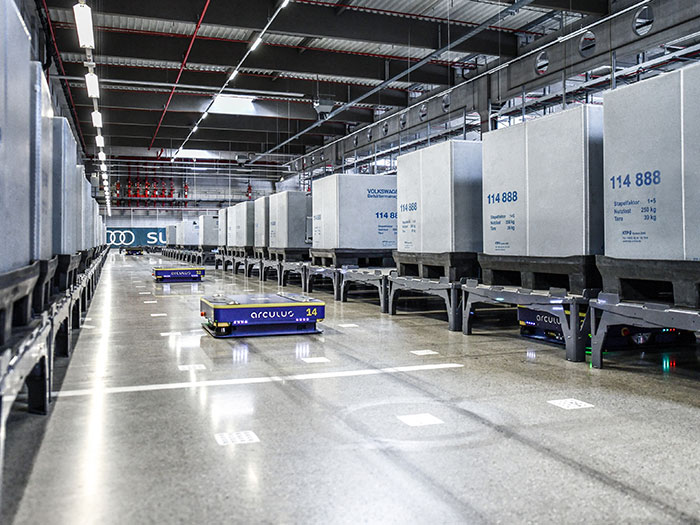
Audi plants have been using automated guided vehicles (AGVs) for many years, particularly in logistics areas where employees pre-pick components in the correct sequence – commonly known as “supermarkets.”
These are the areas where Audi is introducing Supermarket 2.0, a new approach that reverses the basic sequencing principle: here goods come directly to the employee rather than the other way around. This is all made possible thanks to innovative control software developed by Audi experts together with Ingolstadt-based start-up arculus.
From person-to-goods...
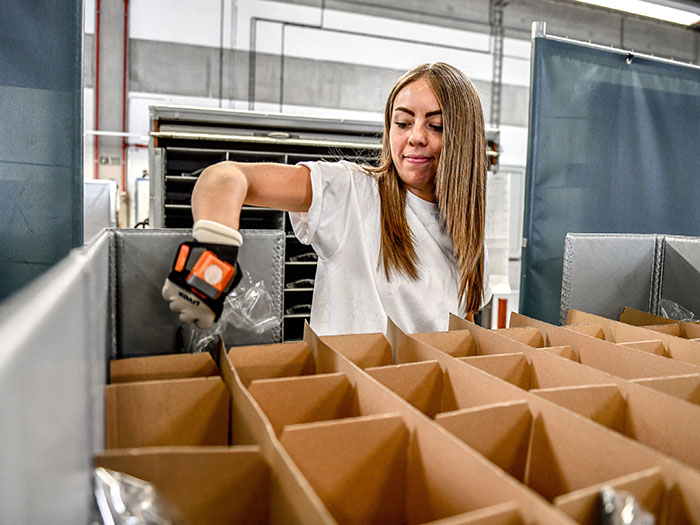
Under the person-to-goods principle, employees used to have to move around continually and cover large distances when picking components. Supermarket 2.0 makes the goods-to-person principle possible on a large scale for the first time, bringing with it clear benefits.
The AGVs roll under the containers with the necessary components and transport them to a fixed pick station in the correct sequence. At each station, a logistics employee prepares the components required on the production line.
The Audi Fleet Manager functions as the central control software. As the racks take up less space, this system will reduce storage space by around 25 percent in the future, as well as saving time.
...to goods-to-person
“Supermarket 2.0 and Audi Fleet Manager mark an important milestone on the path to smart logistics of the future”, says Peter Kössler, Board Member for Production and Logistics at Audi.
The wide variety of parts and the need for correct sequencing make automobile production challenging for the centralized control of automated guided vehicles. Developed in-house, Supermarket 2.0 is already being used at the Ingolstadt plant. The software currently controls eight automated guided vehicles simultaneously, with this figure set to rise to 32 by the end of the year.
China
In Foshan, China, Audi experts and employees from FAW-Volkswagen Automotive Company Ltd. have planned and set up a similar Supermarket 2.0 in parallel. The system went live in early 2020 in the FAW-VW plant which manufactures the Audi A3, Audi Q2L and Audi Q2L e-tron for the Chinese market as well as various other Volkswagen Group vehicles.
The solution was based on an AGV system from a local manufacturer and was customized to the specific requirements of Supermarket 2.0 and automobile production. “Worldwide, the Audi experts benefit hugely from the experience their colleagues in Ingolstadt acquired with their pioneering work,” says Dieter Braun, Head of Supply Chain at Audi.
Innovation and safety
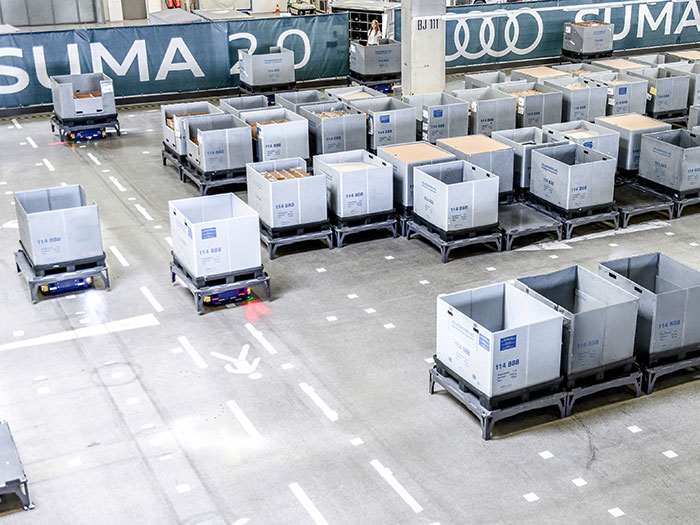
In 2015, Audi became the world’s first automobile manufacturer to test the goods-to-person principle on a small scale, with AGVs helping employees to familiarize themselves with the “supermarket of the future.” The automated guided vehicles used today in the Supermarket 2.0 can transport material weighing up to a ton and move at a speed of 1.5 m/second, guaranteeing employee safety at all times.
Supermarket 2.0 is an innovative solution which will be rolled out to more Audi locations and to other Volkswagen Group brands. Audi Fleet Manager will also offer another benefit in the future: allowing AGVs built by different manufacturers, and with their own control software, to communicate with each other.
Previously, given that they could not interact with each other, AGVs from different brands needed separate drive routes to prevent collisions.
That means all automated guided vehicles will be able to operate simultaneously in the same area, each using their own particular strengths and complementing each other.
Supermarket 2.0 will provide a basis for implementing similar systems elsewhere: Audi experts will test and implement the solution developed with the German Association of the Automotive Industry (VDA), and also look at upstream and downstream processes.
Source: AUDI AG