Safety and precision: how lithium-ion batteries are assembled
A series of processes that must be managed with great care and in total safety, dedicated facilities and specific measures: here’s how batteries are assembled in ŠKODA’s Mladá Boleslav plant.
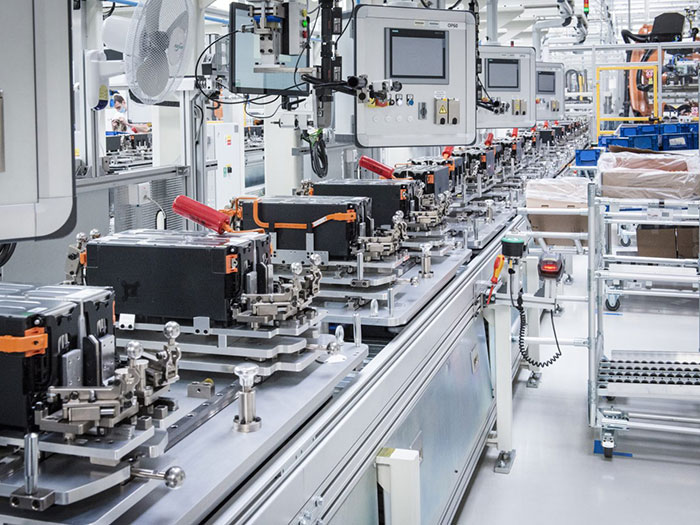
An external aluminium case, modules with lithium-ion cells, and the electronic control unit – these are the three main components of a battery, alongside a complex cooling system. But what steps are required to get to the finished product? Let’s find it out together.
In the Mladá Boleslav plant, the team responsible for assembling the lithium-ion batteries for ŠKODA plug-in hybrid models and other Volkswagen Group cars can count on a state-of-the-art and highly automated production line with a capacity of 180,000 batteries per year.
The line comprises three main branches. In the first branch, the modules containing the lithium-ion cells, which come from an external supplier, are assembled in groups of four; in the second, they are inserted into the case that houses them and then sealed, and in the third, the electronics are assembled.
The importance of safety
In the first area, the cell modules proceed along the line in two parallel streams: one for the left and one for the right part of the battery. Each module comes from the supplier charged to 20% capacity, so safety precautions are necessary right from the start.
The first step is to fit the module with special heat-conducting foil that helps improve the cooling of the entire battery set. A cooler is inserted between the modules – once connected, coolant liquid flows through the cooler.
Special protection
The low-voltage electronics – or the control module, known as the e-box – are made on a separate part of the line with enhanced protection against any excess voltage from static.
Individual components on the line are specially protected and everyone in the workplace wears special clothing. “Flooring, clothing and shoes must be ESD-certified and must be regularly tested to check that they shield against static electricity”, explains Otakar Mašek, a battery assembly specialist.
Robots and aluminium
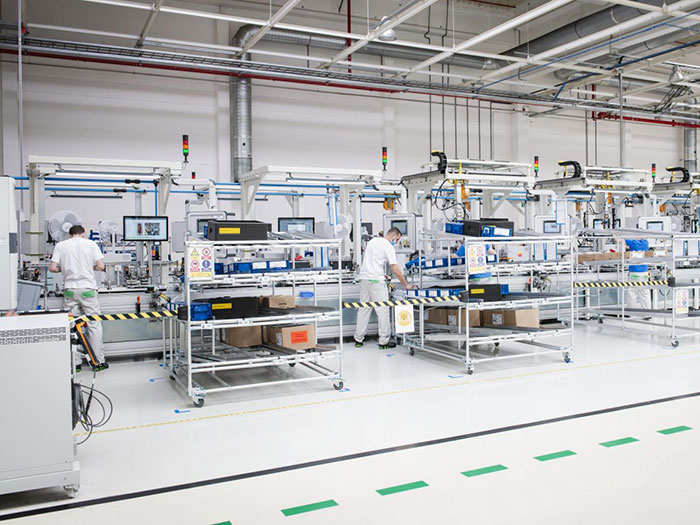
Along the line, in the area where the aluminium casing that houses the modules is formed, most of the handling work is done by robots. However, at some stations there is a manual backup in case the robot is unable to complete the job.
The massive aluminium case is produced by an external supplier. On the line it is fitted with all the necessary components: connectors, seals, stops, and screw bushes, as well as an external heat shield that protects the entire battery from the exhaust heat that runs beneath it.
Screws and scales
When the case is fully assembled, it is the turn of a special assistant to do its bit: a robot that uses a vacuum cleaner to make sure that the case is free from any impurities that might cause problems during operation.
The case is now ready for what is known as the “marriage”. While in automobile manufacture this has traditionally meant the stage when the body is joined to the chassis and engine, here it means inserting the battery modules into the case. This operation is done by a robot, while another robot positions and tightens the screws to join the case and modules together.
Next comes the cooling circuit, the low-voltage cabling, the filler material, and support braces. “The screws for attaching braces are on a special trolley with scales, which can tell whether the worker used the right number of screws,” says Otakar Mašek.
Felt-tip pens and precision
After all the connectors have been attached inside the battery, the employee at the next station uses a felt-tip pen to make a dot on each point of the connection to show that a visual check has been performed. “This requirement forces each employee to actually look at the connection, fully concentrating their attention levels”, Mašek says.
All that’s left to do after that is to connect the module to the control unit, and the battery is then ready to be sealed. The lid on the case is secured with a double seal: rubber and a special glue. Finally, the lid is screwed on by a robot.
The final tests
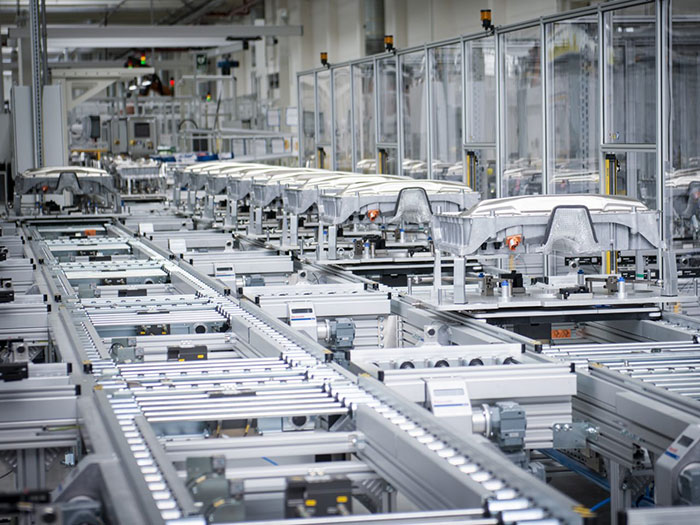
Assembly is followed by a series of tests. The first is the seal test, which involves checking the cooling circuit and the battery as a whole. From time to time, a different-looking battery appears. This is a specimen unit, able to simulate seal defects, that verifies that the seal testing apparatus is working properly.
The electric tests come next: high-voltage and low-voltage parts are checked, and tests are carried out to make sure the insulation works properly. Once the lithium battery has been through all the tests, it is charged to around 37% capacity and given a warning label and its own type label for identification purposes (printed and affixed automatically) together with other details.
The finished battery is then dispatched to the warehouse, ready to become the beating heart of one of the Group’s models.
Source: ŠKODA