IoT, automatic robots and virtual reality: ŠKODA's latest innovations
As well as being about to become CO2-neutral, the ŠKODA plant in Vrchlabí is a real hotbed of innovation. Here an automatic system for the ordering and supply of components for production has been introduced and virtual reality is used to simulate the installation of new workstations.
The ŠKODA plant at Vrchlabí, which specialises in the production of DSG gearboxes, is increasingly becoming a reference structure for the principles of Industry 4.0. In 2012, the site was modernised and converted into a component plant within just 18 months and, in 2015, was named ‘Factory of the Year’ for its rapid transformation. The factory’s expansion goes hand in hand with a commitment to meeting significant sustainability targets. The Vrchlabí plant is set to become completely CO2-neutral by the end of the year, thanks mainly to a strategy of switching to renewable energies in order to reduce emissions.
Today, the facility plays a key role in both component production and technological development – it is one of the most modern sites within Volkswagen Group. Of its recent innovations, two in particular stand out: an automated ordering system for parts required for CNC processing lines and the installation of a new robot station for production, which made use of a ‘digital twin.’
Automated ordering and supply
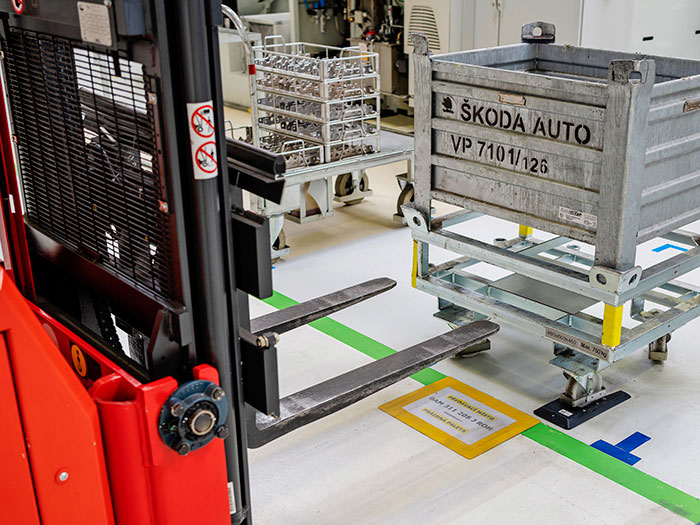
New parts for the CNC processing lines are ordered automatically before being transported to the right place by autonomous robots guided by Internet of Things (IoT) sensor technology. By combining the automated ordering and supply of components using robots, ŠKODA is pressing ahead with the digitalisation of production.
“By taking this new automation step, Vrchlabí is continuing to strengthen its position as one of the most state-of-the-art production facilities in the industry”, says Christian Bleiel, Head of Component Production at ŠKODA. “The collaboration between man and machine is a concept that we are consistently pursuing, and will further increase productivity”.
Greater productivity and safety
The process, that means parts can be automatically supplied to the CNC processing lines, is simple. In the warehouse, logistics employees place the required components on a load carrier. An automatic robot then picks up the carrier and transports it to the correct position on one of the CNC lines. On its return journey, the robot takes an empty load carrier with it and automatically returns it to the parts warehouse.
Due to the use of IoT technologies, the process allows for an automated, continuous supply of parts to where they are needed. This boosts manufacturing productivity while increasing safety for logistics employees, who are no longer required to enter production areas. Thanks to this system, the CNC machines can be supplied with more than 50,000 parts per day. And the costs of this automated process are expected to be covered in less than three years.
The new robots
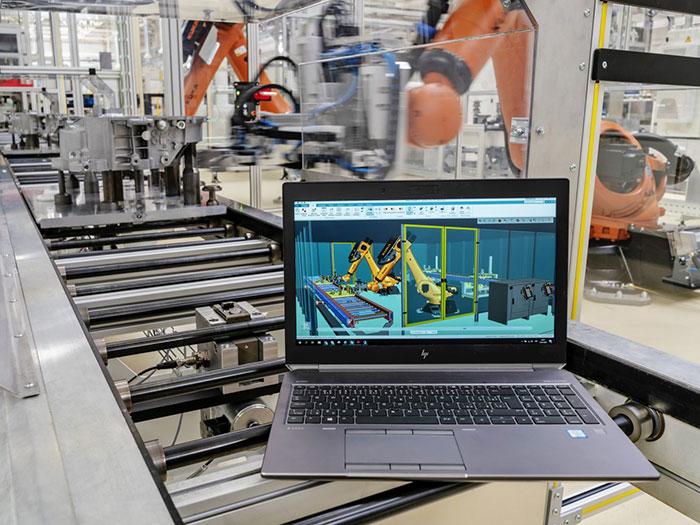
Adding a new robot station to a production line requires in-depth planning – especially if regular operations are expected to continue at the same time. To do this, ŠKODA made use of a ‘digital twin’ to install a new station without any repercussions on production.
Simulations of the equipment and factory were used to run through all processes and scenarios in advance. This meant the project was operational three weeks sooner than if the system had been installed using conventional methods.
The simulation
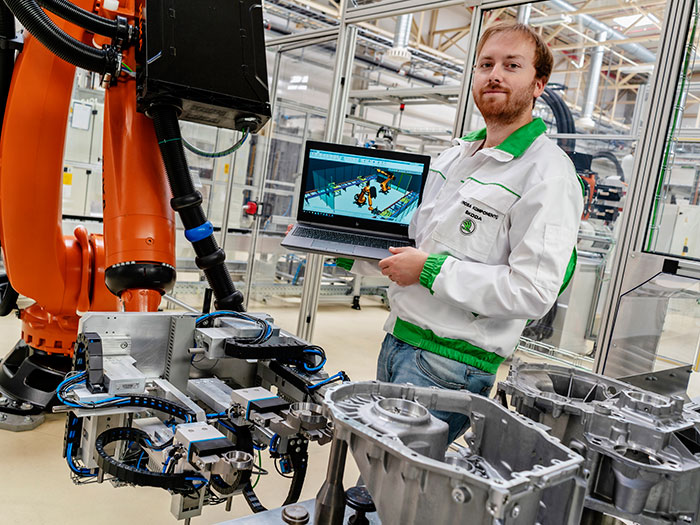
“Without Industry 4.0 technologies, we would not have been able to work in this way. Due to a lack of space, it would not have been possible to set up the new unit next to the existing stations and test-run operations alongside regular production. The use of a ‘digital twin’, however, allowed us to create an extremely detailed virtual image of the plant, simulate processes and procedures, and thus seamlessly add to the production line”, explains Bleiel.
A 3D model of the robot station was used to create the ‘digital twin’, cloning its arms, sensor logic and safety components. This allowed all mechanical and kinematic processes to be realistically simulated. Meanwhile, the software ensured smooth communication between all hardware components and the program-based control sequences on the production line.
Less than 30 seconds
After developing and testing the control electronics and determining the space required for the new robot station (saving approximately 40 square metres thanks to optimising the requirements in advance), the technicians were able to prevent any chance of the robot arms colliding and calculate the ideal cycle time. At the newly set-up robot workstation each DSG gearbox is provided twice with four bearing components in less than 30 seconds.
To guarantee the incredibly high level of precision required for the transmission’s rotating parts to function optimally, this production step is entirely automated. By using the digital twin, the robots’ control programs were also developed before the physical robots and their peripherals were even in the factory.
Source: ŠKODA