From industrial PCs to cloud servers: Audi innovates production
New software-based system allows centralized control of production via servers: a solution to secure processes, speed up updates and reduce maintenance costs.
Audi is radically innovating industrial automation by using the Edge Cloud 4 Production local server solution. Work is centralized, local servers are used instead of hundreds of industrial PCs, and software plays a decisive role over hardware. Once it passed all the tests in the Audi Production Lab, this solution was implemented at the Böllinger Höfe production plant, where three local servers control the workflow. If the system proves to be reliable, this unique automation technology will be rolled out for serial production throughout the entire Volkswagen Group.
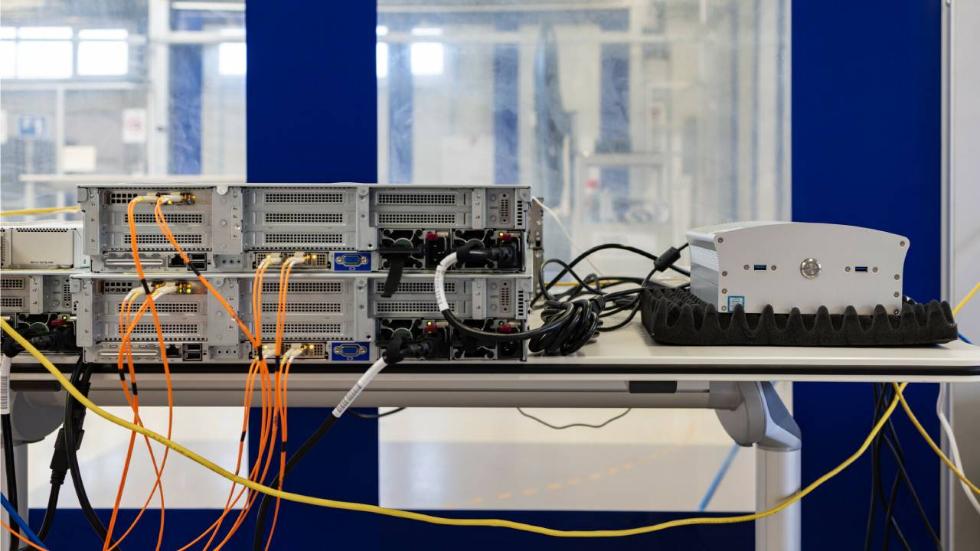
Böllinger Höfe
What is the advantage of centralization? If the plug is disconnected from a server in the Audi Production Lab in Ingolstadt, simulated production in the Böllinger Höfe still continues without interruption, because there are two other servers that continue to reliably control the 36 production cycles.
Audi wants to be the first car manufacturer in the world to use these centralized server solutions in cycle-dependent production. The Böllinger Höfe - a facility where the Audi e-tron GT quattro and R8 are produced - is located near the Neckarsulm plant and is a suitable place to test these innovations on a small scale and then transfer them to larger production departments.
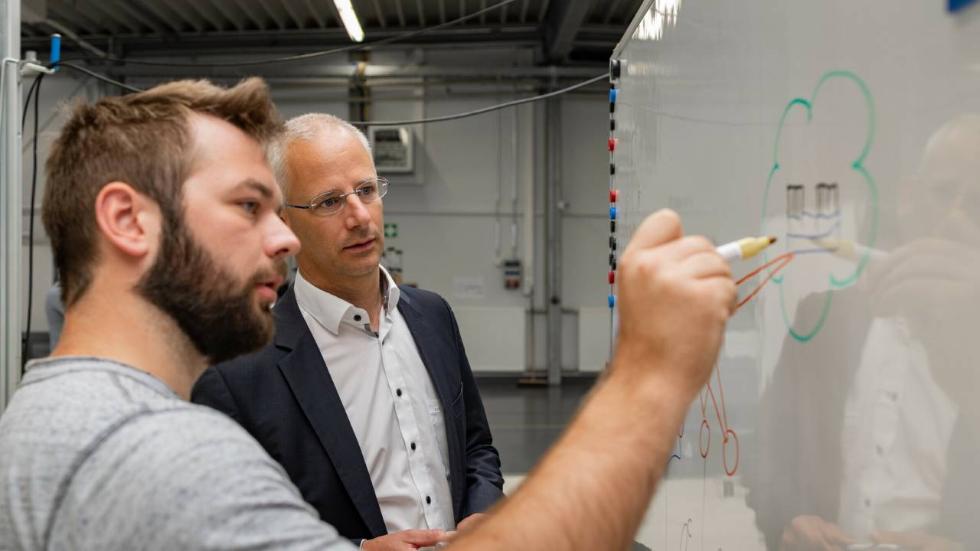
From hardware to software
With the Edge Cloud 4 Production system, a few centralized and local servers are able to perform the same tasks as many expensive industrial PCs, because peaks in demand are leveled over the total number of virtualized clients, with much more efficient use of resources. This makes production faster and simpler, particularly with regard to software rollouts, operating system changes and IT-related expenses.
"This is a revolution: we used to have to buy hardware to introduce new functions, now we only have to buy applications in the form of software and it's a big step towards IT-based production", explains Gerd Walker, Member of the Board of Management of Audi AG for Production and Logistics.
From industrial PCs to servers
The key advantage of Edge Cloud 4 Production is that it can replace a large number of industrial PCs along with their input and output devices, and as a result, there is no longer a need to deal with their individual maintenance. It also improves process safety, since in case of disruptions the load can be shifted to other servers, while a broken industrial PC would have to be replaced, a time-consuming operation.
Employees' work also becomes easier, because it will be possible to use terminal devices (thin clients) with power-over-Ethernet technology, which means they are powered via Ethernet cables and can take advantage of the computing power of local servers. They are also equipped with USB ports for output devices. In this way, it will be sufficient for employees to look at a monitor to see what needs to be mounted onto which vehicle, without having to rely on an oversized PC with large processing and storage capacities. "Software-based infrastructures have proven themselves in data processing centers. We are convinced that they will also work well in production" says Henning Löser, Head of Audi Production Lab.
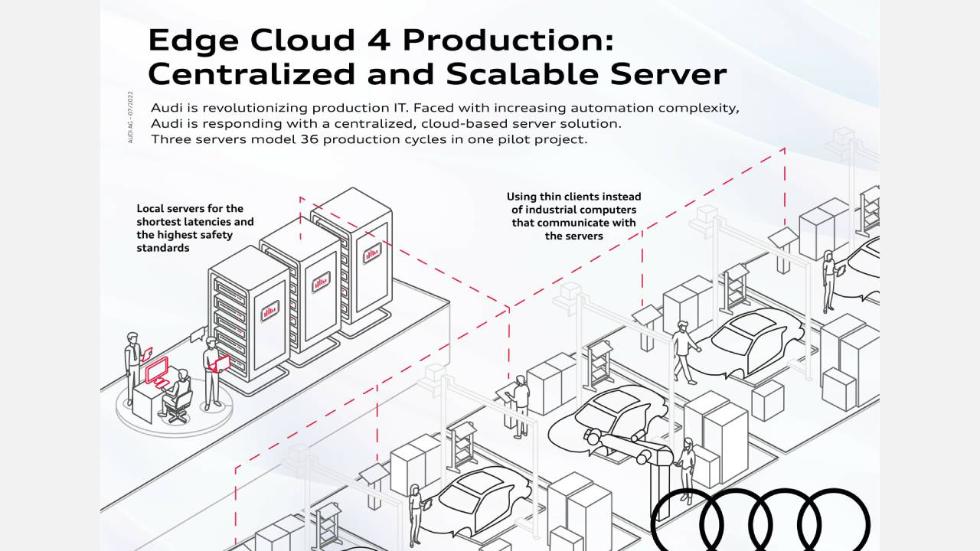
Hyper-converged infrastructure
Edge Cloud 4 Production is based on a so-called hyper-converged infrastructure (HCI). It is a software-defined system that combines all the elements of a small data processing center: storage, computing, networking and management. Software defines features such as web servers, databases and management systems, while the cloud can be quickly scaled to fit different production requirements and local servers allow very low latencies.
However, the system cannot be connected to the public cloud due to stringent production security requirements. "These are the reasons why we install the servers near us and why the solution is called Edge Cloud: because it is close to our production environment," adds Löser.
Maintenance and security
Edge Cloud 4 Production makes maintenance easier and increases IT security. With industrial PCs, the patch cycles (the intervals between necessary updates) are usually longer, and updates can only be installed during pauses in production. With the cloud-based infrastructure, on the other hand, updates can be rolled out in minutes via the central servers and in all virtual clients at the same time. "In the future, the need for additional functionality will get increasingly elaborate and expensive," says Christoph Hagmüller, Head of IT Services at Audi Neckarsulm.
This way, however, the cost of upgrading an operating system can be reduced by a third. "In addition, with the server solution, we are no longer dependent on production downtime. We have enormous flexibility to ensure that our software and operating systems are always completely up to date", Hagmüller concludes.
From fiber optics to 5G
Both data processing centers at the Neckarsulm plant are slated for series production and are connected via a fiber optic cable to the Böllinger Höfe, while 5G will come into play later. Thus far, a separate computer has been installed on all AGVs - automated guided vehicles - that obviously needs to be updated individually and still has limitations in acquiring new features. "For that we need a fast, high-availability network. In our test environment in the P-Lab, we have taken another step forward regarding 5G", Löser concludes.
Source: AUDI AG
VGI | Responsible OU: VP | Creation date: article date | Class 9.1