Electric cars: the secrets behind their batteries
Zero-emissions mobility requires a completely different technical approach. At the heart of the technology there is no longer an engine but rather a battery pack, which determines key parameters such as range, driveability and comfort.
Battery technology has evolved significantly over the years: from initial lead-acid cells, through the intermediate solution of nickel metal hydride (NiMH) batteries used for initial hybrid models, up to the current lithium-ion batteries which were widely used in electronic devices such as smartphones, tablets and PCs before débuting in the automotive world.
Lithium batteries
The ideal requirements of a battery are well known: good range, low cost, long lifetime, the ability to use it on a daily basis, and minimal recharging times. To meet these requirements, the Volkswagen Group uses lithium-ion technology and has developed a specific modular platform for full-electric vehicles, the MEB, which is at the centre of the “Electric for all” project. The first model built on the MEB base will be the Volkswagen ID.
In this case the battery is embedded in the vehicle floor, taking up less space and significantly lowering the centre of gravity, allowing for optimised weight distribution – characteristics which translate into a dynamic and balanced drive and a high level of on-board comfort.
How they are made
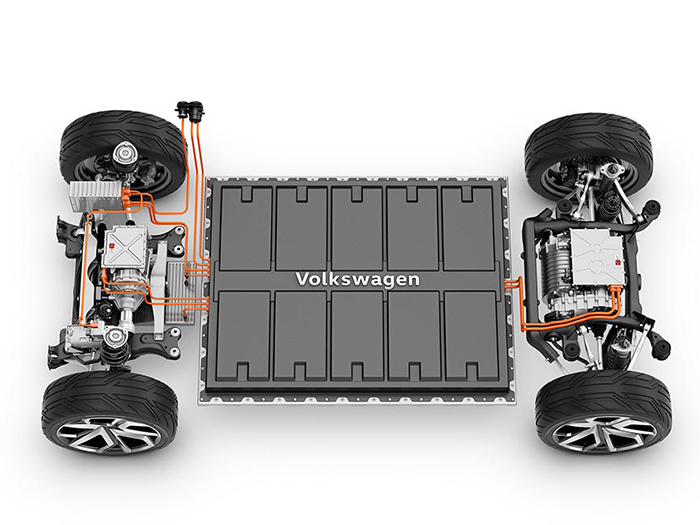
Each battery is composed of smaller connected cells, arranged in a way that looks somewhat like a bar of chocolate. Both cells with a “pouch” or “prismatic” structure can be used. The two main characteristics of the cells are their energy content and energy density, in other words the ratio between the power and size.
The structure, for MEB batteries, is relatively simple: the lower level, that closest to the road, is composed of an aluminium housing which protects the batteries and guarantees their safety even in the event of an accident. Here we also find the cooling system – which keeps the lithium within the optimum temperature band, between 25 and 45° C – and the components for both high voltage connection (for propulsion) and low-voltage connection (for auxiliary services). The cell modules are inserted into the housing; these are divided longitudinally by the various control and monitoring units of the cells themselves. The modules are networked via dedicated connectors. The housing is then fitted with a lid which can be removed if maintenance is required.
How they work
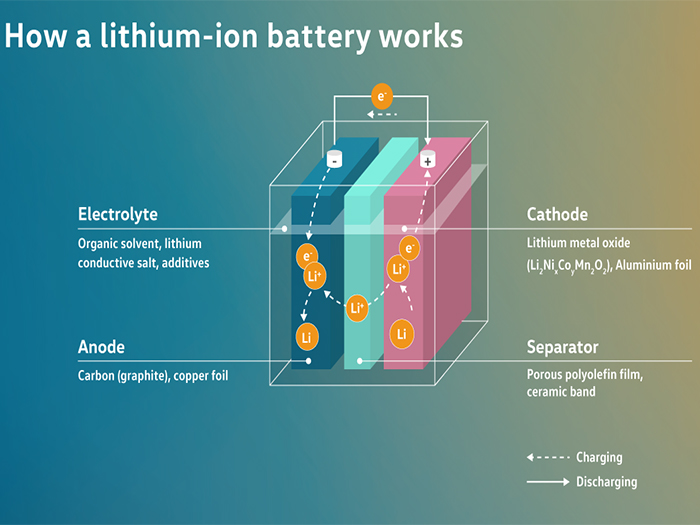
A lithium-ion battery cell consists of an anode (carbon, copper foil), a separator (porous polyolefin foil, ceramic-coated), a cathode (lithium metal oxide, aluminium foil) and an electrolyte (organic solvents, lithium conducting salt, additives). During charging, the lithium ions migrate from the cathode to the anode and are stored there. The electrical energy - fed in from the power grid - is converted into chemical energy. For this purpose, the electrons flow through the circuit, while the lithium ions flow through the separator. During the discharge process, the lithium ions migrate back to the cathode. The chemical energy is then converted back into electrical energy. In this case, the electrons flow through the circuit and the lithium ions flow through the separator in the opposite direction.
Range and speed of charging
As previously mentioned, the MEB system is modular: it is a solution which allows a high level of flexibility in terms of power, and therefore range. The ID. family, for example, can be configured with different capacities for ranges between 330 and more than 550 kilometres according to the WLTP standard. Another important parameter is that of charging power: the battery in the ID. can absorb up to 125 kW, meaning that when fast charging infrastructure is present, charging times will be significantly shorter and the number of charging stops reduced.
The future is “solid”
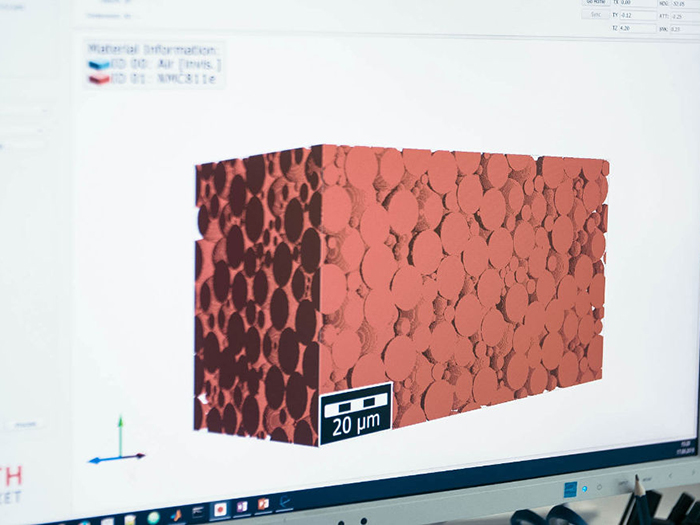
The next step in the evolution of batteries will be the switch to solid state models, which are currently in development and will reach production in future ranges. The main characteristic of these batteries is being based on solid electrolytes (inorganic crystalline and polycrystalline solids, polymers, composites and other materials) which will offer higher energy densities and therefore higher total capacities, as well as being able to work at higher temperatures. These advances will make it possible to reduce charging times and also increase the quantity of energy stored, with consequent range increases.