Development, production and logistics: applications of virtual reality
Saving time, simplifying processes, improving collaboration and increasing efficiency - these are some of the benefits of virtual reality, which are gaining importance at Volkswagen Group. In the Virtual Reality Center of Excellence, the Digital Customer Check and the Digital.Realities:Hub, VR technologies are at home.
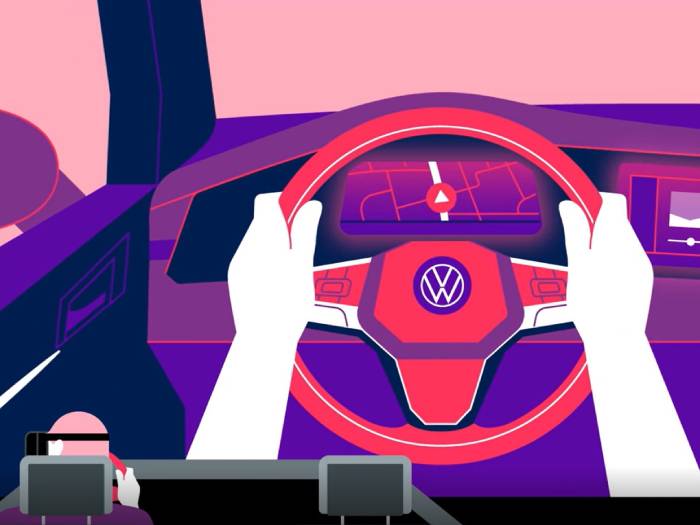
Virtual Reality (VR) is a key tool in the development of new cars, and it is already useful in the early stages. Volkswagen's Virtual Reality Center of Excellence is dedicated to this technology, which allows the developers, among other things, to drive a car in the virtual environment and receive the same sensations as in the real one. By simply entering the driving simulator and putting on the VR glasses, you can experience both the performance of the car and the internal functions of the vehicle, including hi-tech solutions.
The simulator reproduces a cockpit: there are no doors or a passenger seat, the dashboard has a flat surface and a mount for dummy displays. The seat, steering wheel and pedals can be configured with the same proportions as the vehicle of your choice, from city cars to light commercial vehicles. Through VR glasses, the display and all instruments can be seen virtually, while a camera system tracks hand movements and transfers them to the virtual scene.
Virtual reality in development: the simulator
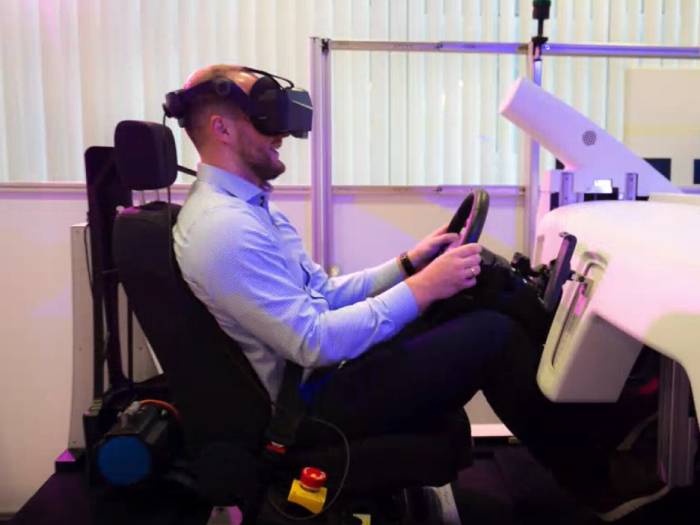
“The raw data for defining the interior comes from various technical development areas, it is formatted for our needs, visualised by a game engine and transferred to VR”, explains Florian Kerzel, Head of IT Development. Sandro Hagemann, who coordinates the development of the visualisation software, echoes him: “All the pieces fit together perfectly. In VR, we work with almost the same level of precision as in the real world”.
The driving experience is realistic, because the longitudinal and lateral accelerations are generated by an electromechanical hexapod, to which the variable cockpit is attached and which simulates the movements of the chassis in all directions. Obviously, the ergonomics can't be 100% perfect and suitable for everyone: “Users are very different, and their expectations regarding the comfort of the seats and the use of the controls change a lot. We try to achieve the optimum compromise, and the simulator is a great help in achieving this”, concludes VR system developer Bert Hartfiel.
Digital Customer Check
The Digital Customer Check (DCC), on the other hand, is a key step in which developers evaluate the interior of a new model from the perspective of future customers. “Here, we use a static seat box that, just like the driving simulator, accurately reproduces all of the interior dimensions of the new model”, says VR specialist Çağdaş Tekcan. During the DCC, virtual reality helps developers to evaluate the impression subjectively, especially colours, upholstery and optional equipment can be changed at any time. In addition, the interior of the predecessor model or another brand's model can also be displayed for reference.
Digital.Realities:Hub
These virtual tools are of great benefit to the company because, particularly in the early stage of vehicle development, they make it unnecessary to build physical prototypes; they reduce expenditure on materials and business trips, increasing sustainability; they also simplify coordination and evaluation processes.
Many other virtual tools are used in the Volkswagen Group, such as the Digital.Realities:Hub - a cloud-based platform that connects users with VR and AR applications and is made up of around 150 VR tools. They also include a large number of services and functions required for AR and VR applications, such as automated data formatting and data pipelines, resource and user management, and digital collaboration. The Digital.Realities:Hub incorporates almost all of the Volkswagen Group's brands, companies and global locations; around 3,300 virtual reality sessions are held there each year.
Virtual reality in production: 3P workshops
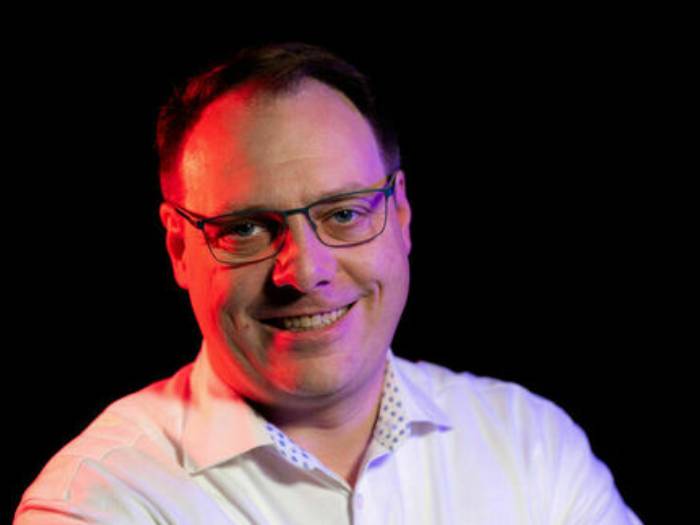
The 3P workshops concern the production preparation process and are held when an assembly line needs to be set up or modified. Those in charge of plant planning, logistics, assembly, pilot production centre and quality control identify how to set up each cycle down to the last detail, taking into account the positions of each tool, the routes taken by the workers and the feasibility of the movements. In the past, plywood and cardboard were used to simulate the production line, taking old, dismantled prototypes as a reference.
“But prototypes are very expensive, which is why we moved the workshop to the world of virtual reality: virtual meetings, virtual cycles and virtual cars. The data basis is a digital image of the production facilities, onto which digital images of the assembly cycles are inserted using a games engine, then visualised using 3D glasses”, explains Dennis Abmeier, Business Partner Manager Digital Realities Group IT.
The use of avatars in VR
“People who attend these workshops meet in the plant training centres and in rooms with similar facilities. They wear controllers and data gloves, while the tracking system in the room transfers their movements to the simulation, where they act as avatars, also configuring their own sizes. In this way, it is possible to understand how the specialised technicians will move in the production line space. Finally, each participant has a display on their wrist, which shows the steps of the process and records the time taken by each step” Abmeier concludes.
The e-tron GT was the first Audi model not to have a physical prototype in the 3P workshops; after the pilot project, the VR technology moved on - to the Audi plant in Mexico and Volkswagen Commercial Vehicles in Hanover. Software and methodologies are constantly being improved and can also be used in the pressing plant, car body, logistics and paint shop, anywhere in the world.
Virtual reality in logistics
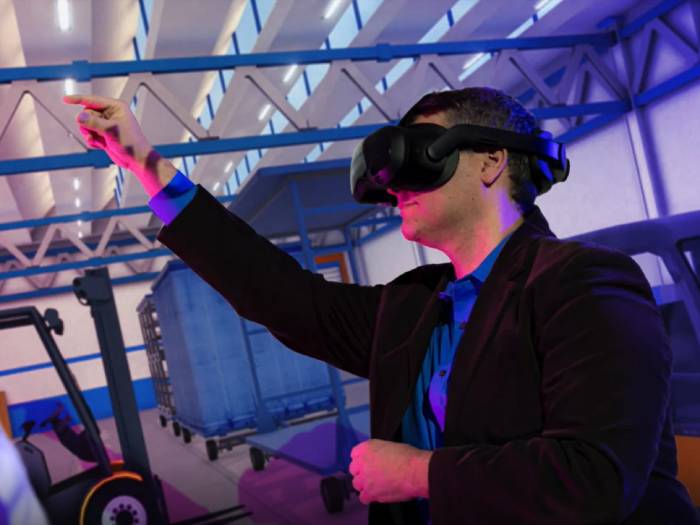
Volkswagen is increasingly using virtual reality to introduce new logistics processes: static representations and texts describing processes are being replaced by VR applications. VR workshops, for example, are about modifying the workflows for a new IT system and its software used in logistics. Each change brings with it many new functionalities and procedures, such as the appearance of labels to be scanned or the handling of inventory errors.
Thus, in these workshops with planners and IT specialists, logistics experts can define processes in advance and share their knowledge. “Previously, colleagues spent hours seating around a table, producing lots of texts and diagrams. With these VR tools, however, processes can be represented in such a way that anyone can run through them virtually and understand them straight away” says Malte Hedemann, Lead Group Collaboration:Hub.
Abstract reality
These simulations used by Hedemann and his colleagues map an abstract reality. In this way, they enable employees who navigate it with glasses and gloves to learn about and test digital systems and tools.
“Within the simulation, both the analysis of vulnerabilities and change management are very fast and targeted. Furthermore, VR applications can be used at every stage of the project, from planning to adaptation, from employee training to routine operations” concludes Hedemann. The VR applications are still in the final testing phase and are expected to be introduced in the Emden plant first and then in other plants in rapid succession, after which the technology will also be rolled out to plants outside Europe.
Source: Volkswagen - Shaping Mobility Hub
VGI | Responsible OU: VP | Creation date: article date | Class 9.1