Batteries for the electric cars: how are they produced?
Batteries are at the heart of electric cars, and their performance and cost are key elements in rolling out e-mobility on a large scale. In the next few years, this sector is likely to see more technological innovation than any other. As such, Volkswagen Group has defined a clear strategy in this area with the activities of the Salzgitter Centre of Excellence at its centre.
Where lithium-ion batteries come from
A pilot line for the production of small batches of battery cells is up and running in Salzgitter. Volkswagen Group will carefully study the delicate assembly process in order to acquire - in a fairly short timeframe - the know-how required for mass production.
Making lithium batteries for cars is an extremely complex process. The easiest way to understand the overall process is to divide it in three main stages: the electrode production, the cell assembly and the final cell conditioning. All three stages can be subdivided into smaller stages.
The origin of electrodes
Everything starts with raw materials in powder mixed with water or solvents to produce anode and cathode formulations. In a technically very demanding procedure, the materials are combined to produce a homogenous paste (slurry). Precise dosing and extreme cleanliness are essential.
In Salzgitter, carbon (graphite), binders and lead additives are used as the most important ingredients for the anode and lithium metal oxide, binders and lead additives are used for the cathode.
Aluminium and copper
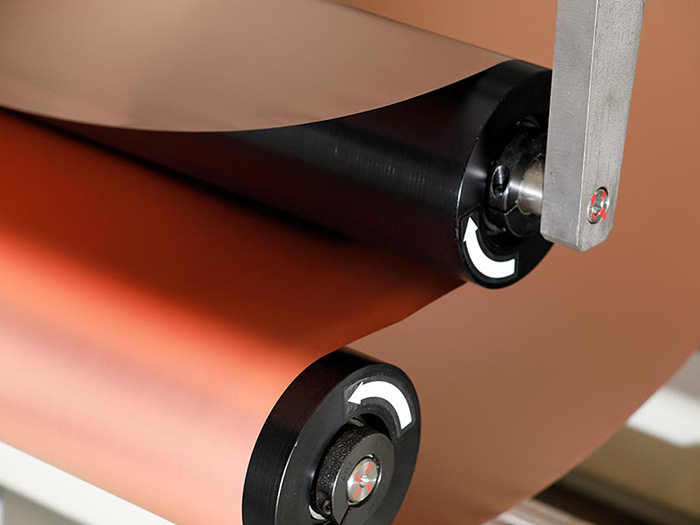
The second step is coating. The paste is transported in atmospherically sealed storage tanks, which ensure the homogeneous distribution of the paste. During coating, the various slurries are applied to carrier foils, the anode to a copper foil and the cathode to an aluminium foil.
The pilot line is equipped with coating technology that enables simultaneous double-sided coating. The drying of the paste on the metal strips takes place in a floating drying process – i.e. the coated strip has no contact with machine parts and “floats” through the line.
Strips and mills
At this point the coated thin film is compressed (roll pressing) in a rolling mill – referred to as a calendar in technical terminology - using a maximum pressure of 200t. The result is impressive: the thickness deviates by a maximum of 4µm from the target value – this corresponds to about one 25th of a human hair. The finished electrode strip (also called “mother roll”) is then removed from the calendar for further processing with special lifting devices and is ready for the subsequent processes. In some cases, it may be necessary to divide the mother roll lengthwise (slitting). This very delicate stage is decisive in determining the quality of the resulting battery cell.
Cell assembly
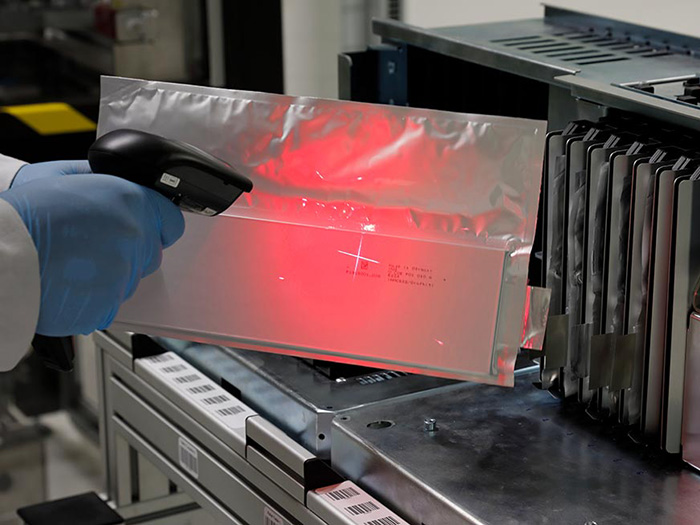
The assembly type and sequence depend on the cell to be produced. The Salzgitter Centre of Excellence distinguishes between seven main steps.
After the sheets have been cut by lasers, they are dried in vacuum drying ovens and processed in special drying rooms where the humidity is 350 times lower than in ambient air. The sheets are then removed, aligned and placed on top of each other with a precision of +/- 0.3mm - all within one second. The process is automated and the sheets are stacked in a repetitive cycle of anode, separator, cathode, separator, anode, etc. The result is a “cell stack”. Stack drying then takes place at a constant temperature while the air is dried and pressurised using inert gases such as nitrogen, helium, neon, argon, krypton and xenon. An alternating cycle of vacuum and gassing accelerates the drying process. After drying, the plus and minus poles of the battery cell are welded. These metal sheets, known as “tabs”, are welded on the pilot line using a laser process.
The electrodes
Next, the stack of electrodes is inserted into the housing - created in a thermoforming line and consisting of a vapour-tight film of several layers. Once inserted, it is sealed with a heat-sealing process. During filling and sealing, the cells - which can have three possible designs - are filled with electrolyte. This is a very delicate stage as the electrolyte must penetrate through the edges of the stack and then spread inwards.
One of the most common cell designs is known as a “pouch” cell, and is used in smartphone batteries. The cells are then inserted into a larger container, made with laminated aluminium foil in a similar shape to coffee bean packaging.
Final cell conditioning
The final cell conditioning is divided into several stages. Firstly, the cells are degassed before being sealed due to gas formation occurring in the cell during the electrochemically formation process. The gas escapes into a dead space inside the pouch cell (also called gas pocket) where it collects and is removed before the cell is given its final shape. The sealing process has two aims: protecting against water entering from the outside and electrolyte leakage from the inside. The quality of the seal determines the life span of the cell. The penultimate step can take up to three weeks. It aims to identify cell-internal short circuits by regular measurements of the open circuit voltage of the cell. The EOL Inspection (End of Line) is the final stage and includes the evaluation of the cell according to its most important electrochemical properties, allowing conclusions to be drawn about its electrical storage capacity, internal resistances and losses.
Source: Volkswagen AG