Volkswagen, natural polymers for a sustainable future
Volkswagen is working on new, sustainable materials for the cars of the future. Biological polymers made from cellulose and fungi, for example, could replace leather.
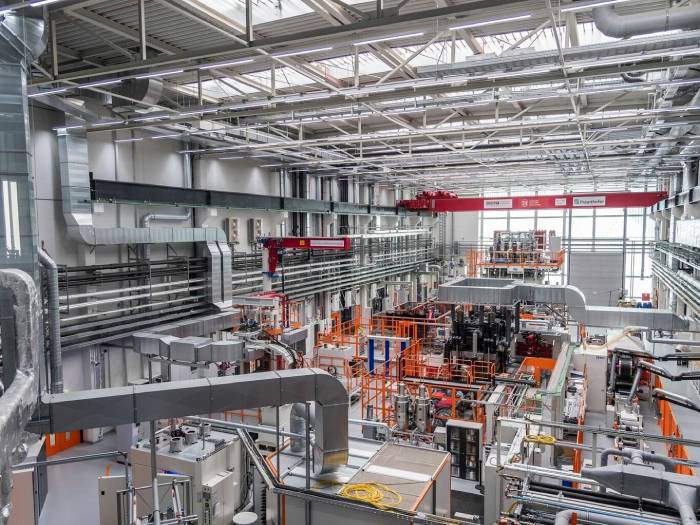
The Open Hybrid LabFactory (OHLF) in Wolfsburg is a special place: at the heart of the research campus is the technical centre, a hall several stories high with industrial robots, injection moulding machines, casting and compression systems. It is here that research is carried out into the materials for the cars of the future, in wire cages and glass cubicles to make textiles, metals, plastics and composite materials even lighter and more sustainable, but at the same time as reliable as the materials of today.
Public-Private Collaboration
The Open Hybrid LabFactory is representative of the public-private partnership model: it involves both companies and higher education institutions. The main members of this campus are the city of Wolfsburg, the Automotive Research Center Niedersachsen, the Fraunhofer Society and the Technical University of Braunschweig, not to mention the involvement of many suppliers alongside the Volkswagen Group, particularly those involved in metal and plastic processing. The transformation of mobility is also changing the work at the campus, with the focus shifting from lightweight construction to the circular economy.
“We want to design processes, materials and components to improve the circular economy. So we are developing new plastics from recycled materials; we also want to automate dismantling processes to make it economical to separate materials into single types; and we are choosing natural materials in organic cycles”, explains Marko Gernuks, who represents Volkswagen on the OHLF Board of Management.
Replacing leather
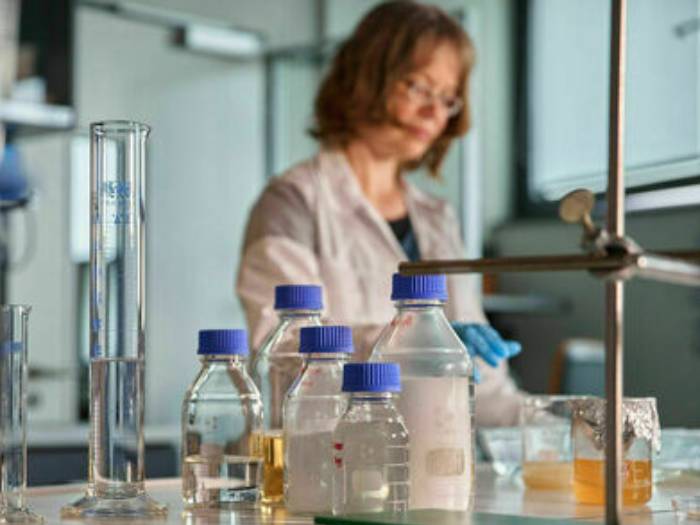
Martina Gottschling of Volkswagen Group Innovation is working on materials research to replace leather: Volkswagen has made the decision to no longer use animal-derived products for the all-electric ID. family. This decision will soon be extended to other models and will also help in terms of climate protection, given that the carbon footprint of leather is relatively high compared to other materials.
According to Volkswagen researchers, biomaterials have huge potential, even beyond industrial crops such as rapeseed and coniferous wood, and can be produced in the laboratory. Pure cellulose, for example, in its natural state is found in plant cell walls, but can be created in the laboratory using bacteria.
Natural polymers
Natural polymers have many useful properties, for example they are highly stable and consistent. In addition, in pure, non-hybrid form, they are suitable for the recycling process and can be composted after use. Within the Open Hybrid LabFactory, pure cellulose can be cultivated in the desired forms and is an easy scalable process that can be adapted to vertical farming systems. Moreover, as a completely organic substance, pure cellulose is perfect for the biological circular economy. “In six to eight years it could be ready for its first use in cars”, estimates Gottschling.
Cellulose and fungi
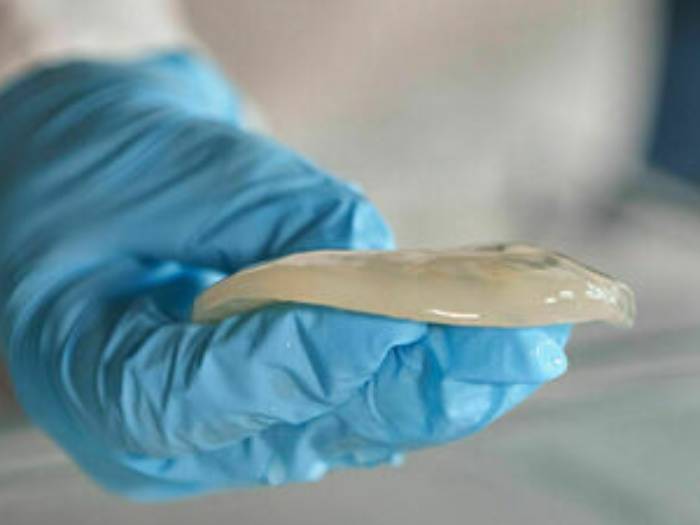
Cellulose is an important raw material in materials research. Specifically, researchers at the Open Hybrid LabFactory are experimenting with a method in which bacteria are fed in a sugar solution, generating cellulose in pure form. Once the growth process has ended, i.e. when the piece of cellulose reaches the desired size, the researchers 'wash' it to remove the bacteria and then dry it through several steps. It is then post-processed and dried, ending with the insertion of an organic plasticiser to generate the desired smoothness of the material.
The Volkswagen Group is also involved - together with businesses in the fashion industry, waste management and tanneries - in another research project for sustainable materials that investigates the potential of natural polymers based on fungal mycelium, the vegetative apparatus of fungi.
Stringent requirements
In the automotive industry, developing an innovative material requires a long testing cycle, and the Volkswagen Group has very high standards in terms of sustainability of components. To be approved for series production, a new material has to pass through forty different tests, which simulate every aspect of the stresses to which it is subjected.
In the case of seats, for example, the covers are tested for mechanical stress, ageing due to heat and UV radiation, and soiling tendency.
Absolute quality
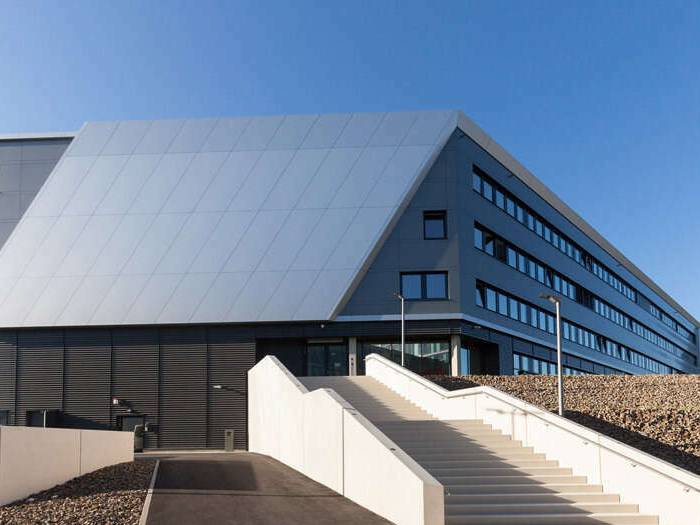
Another important test is the abrasion resistance one, which is carried out using a special device: the material to be tested is pulled and stressed by a circling stamp, while "bullets" are pressed randomly from below. This creates high, localised stresses that are repeated several thousand times a day. At the end of the process, the number of imperfections - the parts where wear is visible - indicates the quality of the material.
In a further test, the tear resistance of the new leather substitute material is compared with that of the real leather and imitation leather currently used. At the end of the tests, the new materials have to prove that they are not inferior in any way to conventional materials.
Quality experience
New materials must not only be sustainable and technologically advanced, but also convey the feeling of high quality that customers expect from a Volkswagen. “Every fabric that we use in the interior must be an experience for customers, throughout the entire service life of the car”, concludes Gottschling.
Source: Volkswagen - Shaping Mobility Hub
VGI | Responsible OU: VP | Creation date: article date | Class 9.1