Specific tests for increasingly complex cars' electronics
Cars' electronic equipment is becoming increasingly complex. To ensure that all systems work properly, specific tests are carried out at ŠKODA in special test stands.
In recent years, the number of control units, sensors and electronic devices in vehicles has increased significantly. Since 2005 there has been an increase from an average of 20 control units to an average of 80 or more, but the specific number depends on the configuration of the car. Currently, the ŠKODA ENYAQ iV and ŠKODA ENYAQ COUPÉ iV are the brand's vehicles with the largest number of electronic devices, control units and sensors.
There are so many possible combinations of control units that it is not possible to test them in conventional prototypes. In addition, before these begin testing, developers must ensure that the basic functions controlled by the electronics, including the brakes, will work. That is why the ŠKODA Technical Development Department, in cooperation with Digiteq Automotive, uses special test stands.
Two types of tests
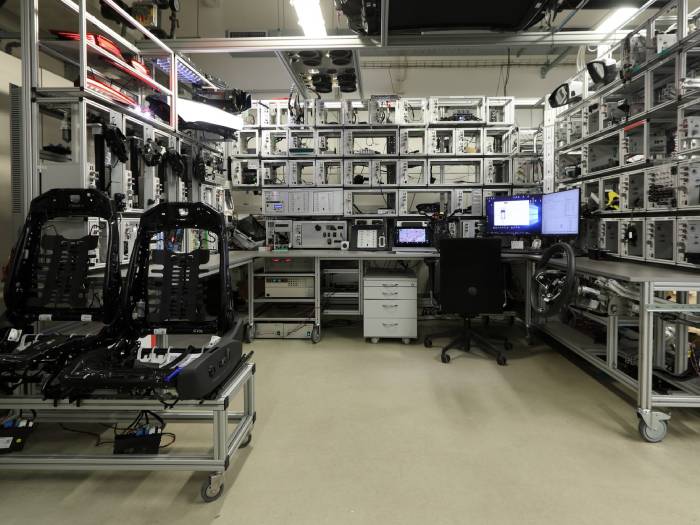
These stands are called HiL (Hardware-in-the-Loop) and breadboard. The former is used to test the functionality created by the control units while the latter focuses on testing the functionality of data communication among control units. The test conditions may appear to be essentially the same, since in these workstations all the (low-voltage) electronics of the car are mounted in frames. The control units are connected by special wiring to "probes" that monitor communications and important data but can also send their own signals that either simulate certain commands and functions or, conversely, deliberately create errors.
"We test not only whether the control units communicate with each other as they should, but also how they will behave in case of unexpected situations, failure or malfunction" explains Lukáš Zavadil of the Midsize/MEB Test Management and Integration Tests department.
The testing phase
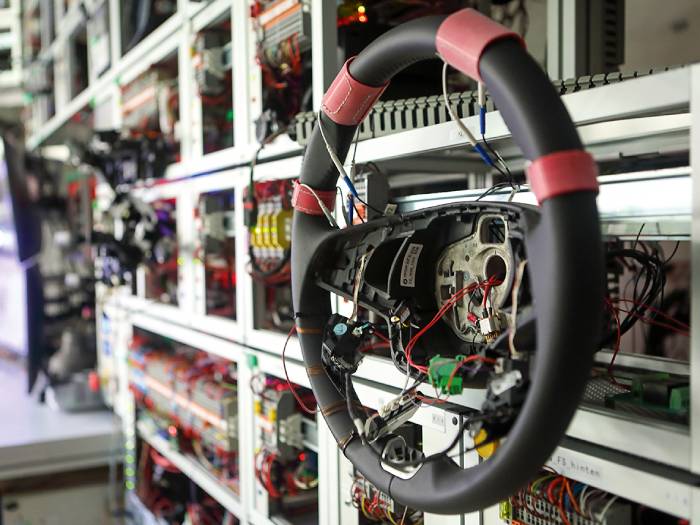
The testing of a car that is still in development starts even before prototypes are built and gradually increases in intensity and scope. "We start with basic tests in the area of the power unit, and as the development of the car progresses, we gradually add tests of comfort functions and assistance systems up to complete tests. Before building the first pre-production cars, we test the complete functionality of the car", Zavadil continues.
Currently, testing continues until the car is launched on the market. "This is because the integration of online services also needs to be verified. And the software for remote control of the car's functions, via a smartphone or a web portal, is often developed continuously until sales begin", further explains Zavadil.
Continuous development
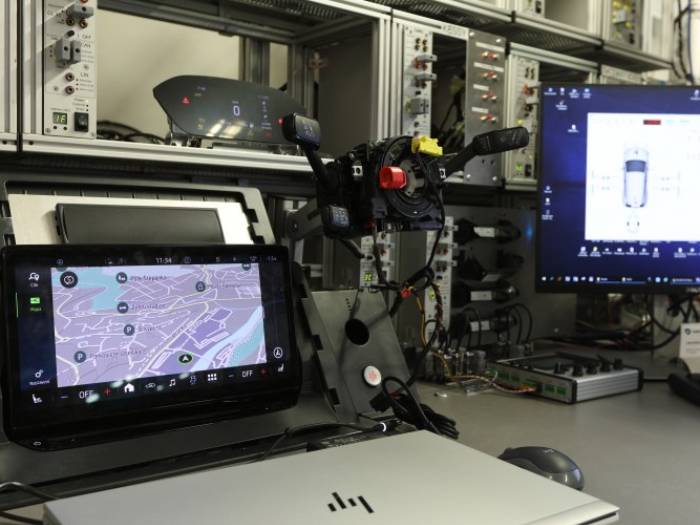
The testing program of a car under development takes about two years. Thousands of tests, automated but also manual, are completed during this time. "We have robots that press buttons and simulate some commands, but we still want to maintain human interaction. We also collaborate with Digiteq Automotive on these activities", Zavadil adds.
During the testing process, the controllers' software is gradually improved and hundreds of configurations are tested. To keep on schedule, one HiL and two breadboards are used for each project; the breadboards become three for an electric car like the ENYAQ iV.
Nothing is left to chance
"We also test seemingly obvious things like the functionality of the warning flashers, which, today, interact with six to eight control units. These have to agree with each other in every situation where the warning flashers are required to be activated", says Zavadil.
Normally it is the driver who activates them, but in other cases they are activated automatically, for example in the case of panic braking or automatic emergency stops. "As for the headlights, we are testing the integration of several basic functions, for example, that they do not turn on when not needed", Zavadil concludes.
Source: ŠKODA
VGI | Responsible OU: VP | Creation date: article date | Class 9.1