SEAT’s innovative test centre for the engines of the future
Located in the Technical Centre, SEAT’s new facilities carry out tests on all engine types using nine test benches and a climatic chamber capable of simulating extreme driving conditions, in temperatures ranging from -40 to +65 degrees.
As part of its constant commitment to innovation and electrification, SEAT has created the most advanced powertrain test centre in southern Europe. SEAT has invested more than 30 million euros in the project and the facilities are equipped with nine multi-energy test benches, which enable different types of tests to be carried out on internal combustion, electric, hybrid and CNG engines. The aim is to ensure they meet the quality, emissions, durability and performance requirements hroughout their entire life cycle.
The Powertrain Development Centre
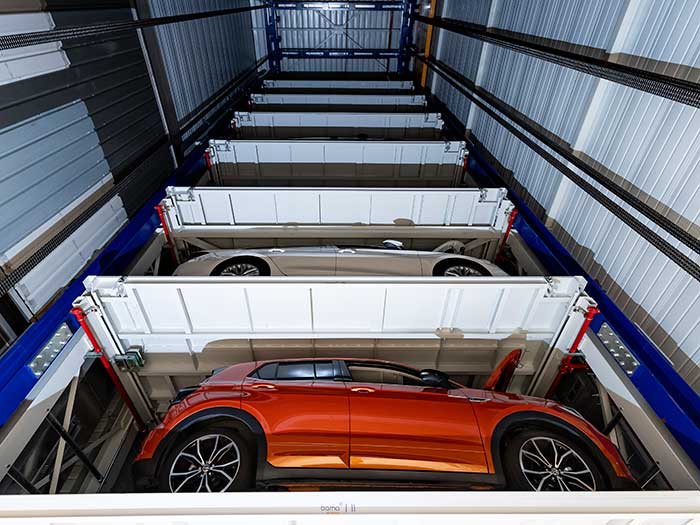
The project to develop the Powertrain Development Centre, located within the Technical Centre, began five years ago. The centre has the capacity to carry out 14,300 engine tests per year, from an early stage of development to the tests required for their approval. 200 people work in the Centre in 3 daily shifts, 24 hours a day, 6 days a week, carrying out tests on engines for different brand of the Volkswagen Group.
The facilities include a climatic chamber capable of simulating extreme driving conditions at temperatures between -40 and +65 degrees, and up to an altitude of 5,000 metres. In addition, an automated tower with a capacity for 27 vehicles keeps them at a stable temperature of 23 degrees to ensure that they are in optimum condition for testing.
The test benches
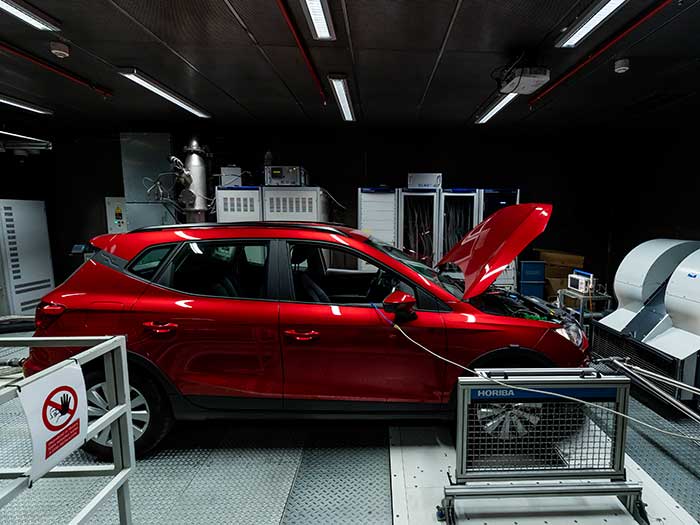
“This is one of the most advanced vehicle development facilities in Europe. The new facilities and the high technical competence of the teams enable new engines to be tested and calibrated to ensure optimal performance for SEAT and CUPRA, as well as the different brands of the Volkswagen Group, with a special focus on hybrid and electric engines,” explains Dr Werner Tietz, SEAT Vice-president for R&D.
The Powertrain Development Centre is equipped with nine test benches, on which the engines are tested and calibrated according to the type of vehicle they will be mounted on. During the development phase, aspects such as fuel injection, intake or power are adjusted, and extreme driving simulations are carried out to observe the response of the engines in extraordinary situations.
Emissions monitoring
The Powertrain Development Centre has an emissions laboratory that performs more than 80 different types of tests on each vehicle, in accordance with the approval requirements for the various global regulations. It also features PEMS devices – these are portable emissions measurement systems capable of monitoring vehicle running data, which are used to perform the RDE (real driving emissions) tests currently required for the homologation processes.
The centre’s durability test bench, meanwhile, sees prototypes and vehicles running up to 200,000 km without any breaks, while engine performance is analysed at all times. A system has been installed that recovers the energy generated by the rollers and returns it in the form of electricity for later consumption.
The climatic chamber
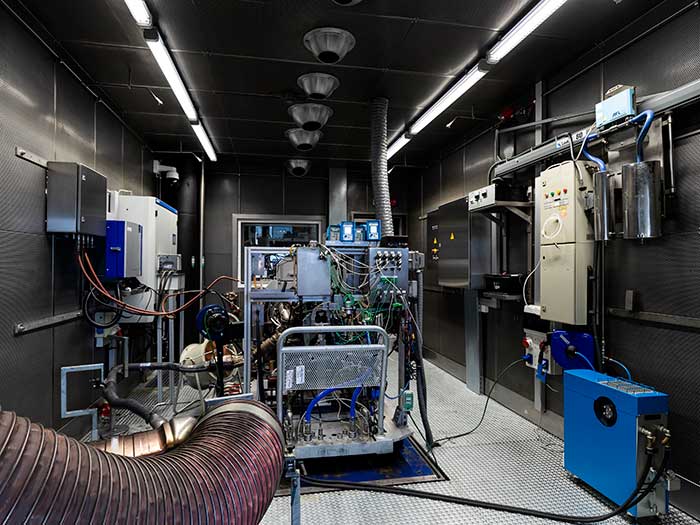
One of the most unique facilities in the test centre is the climatic chamber, where extreme temperatures and atmospheric pressures are simulated, moving from the conditions of the Caucasus Mountains to those of California’s Death Valley in a matter of hours.
In this way, the chamber makes it possible to test the performance of the engines and simulate driving, assisted by robots, in extreme conditions to guarantee the performance of the cars.
The Test Center Energy
In Martorell, SEAT has also begun to build the future Test Center Energy (TCE), its new battery lab. The centre, which requires an investment of more than 7 million Euros, will develop and test various energy systems for hybrid and electric vehicles.
The construction of the TCE is included in the 5 billion Euro investment plan announced by SEAT and is scheduled for completion in April 2021. The 1,500 square metre facility will include different test areas for validating lithium-ion cell modules and different chargers used across the entire range of electrified vehicles.
Source: SEAT S.A.