SEAT, 3D printing for fast and flexible processes
No moulds, no design limitations, and 10 times faster than the standard method: 3D printing has infinite applications and the automotive industry has been among the first to embrace it to save time and gain flexibility throughout all stages of a vehicle’s development and production.
“If you can imagine it, we can make it.” This is the motto of the SEAT 3D printing lab, where its 9 3D printers work for all divisions of the Spanish brand, from design and production to logistics, producing all kinds of elements.
The 3D printing lab is located in the heart of the SEAT plant in Martorell, within the recently transformed Prototype Development Center (PDC). All pre-production processes and activities have been brought together in a new 3,000 m² building, which employs the most cutting-edge technologies such as virtual reality, as well as 3D printing.
The Prototype Development Center
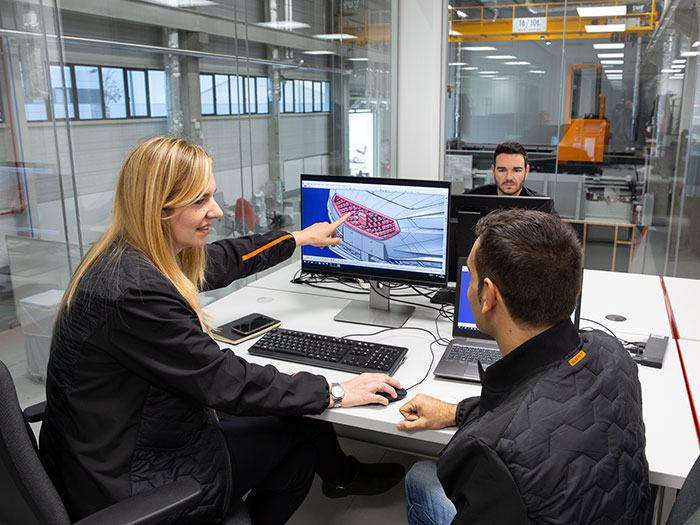
The new building also includes the Design for Manufacturing room, where different areas of the company, such as R&D, quality, processes and manufacturing work together with the more than 250 professionals of the PDC to analyse and improve products in their early stages of conceptualisation.
This helps reduce the launch times of future cars and boosts the efficiency of resource management. “We’ve been working with virtual reality and 3D printing for more than 13 years. With these new facilities and the unification of the PDC, we intend to invest more than ever in the development of digital and electronic solutions adapted to the car of tomorrow”, says Anabel Andión, head of SEAT’s PDC.
The virtual becomes reality
Since its inauguration in 2007, the PDC has become the link between the R&D and production departments – a place where the virtual becomes reality. In that time, it has developed a total of 13 concept cars and worked with 5,235 pre-series models, 2,472 test prototypes, and 224 technical models.
Thanks to its latest transformation, part of the 5-billion-euro investment plan recently announced by SEAT, the PDC now has modern facilities in the centre of the Martorell plant. One of the project’s highlights is the brand new 3D printing lab.
Speed and versatility
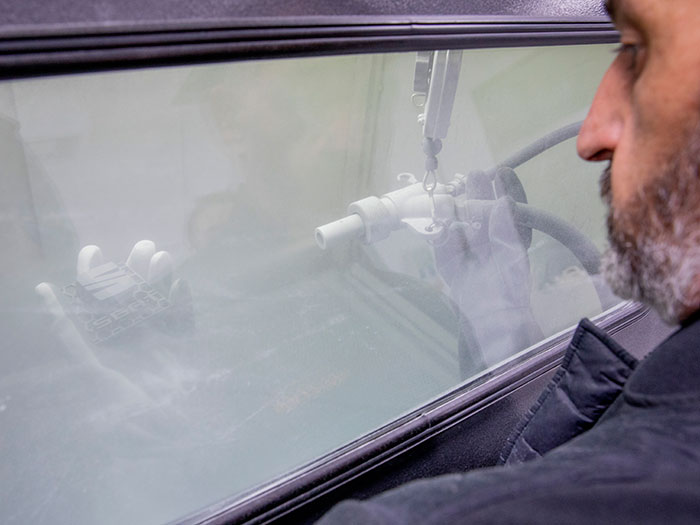
“We can apply infinite geometries and carry out any type of high-precision design, however complicated it may seem. And all in times that are impossible to achieve with the normal process”, explains Norbert Martín, head of the 3D Printing LAB at SEAT. Speed and versatility are the main advantages of this technology, which does not require the use of moulds to make components.
Taking the real-life example of a mirror: firstly, a mould would have to be made, which can take weeks and, if you wanted to vary it in the slightest, you would have to make another mould. With 3D printing, however, this preliminary phase disappears. The technicians receive a file with the design and send it to be printed as if it were a document. In 15 hours the part is ready.
Prototypes and tools
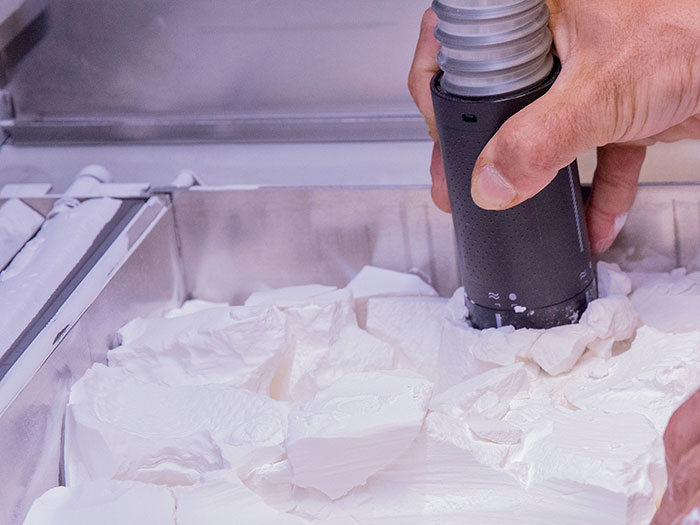
80% of the parts that are printed in the lab are prototypes for vehicle development, but custom tools and utensils for the assembly line, custom logos for motor show vehicles, and even facemask strap extenders and door pulls to assist in the prevention of coronavirus are made here. “Thanks to this technology we supply tailor-made tools that are lightweight and ready for use,” says Martín.
There are several kinds of 3D printers: multijet fusion, sintering, laser, filament fusion, and UV light curing. Depending on what needs to be printed it is more appropriate to use a certain kind of technology, as each printer makes the parts using a specific material.
Customisation
In addition to the exact shape, a specific weight can be achieved, as well as heat resistance of up to 100° C. “An example of the technology we use for creating tools is the continuous filament fabrication printer (CFF). Here we use not only plastic, but also carbon fibre to reinforce it and provide a much lighter and stronger tool,” adds Martín.
The next frontier? Customer-centric applications with customised parts, special series or hard-to-find spare parts. “If, for example, you need a part from one of our historic models no longer in production, we can print it,” says Martín .
Source: SEAT S.A.