Low-CO2 emission aluminium for Audi e-tron GT wheels
Thanks to an innovative oxygen-releasing smelting technology, the Audi e-tron GT’s 20-inch alloy wheels are made from low-CO2 emission aluminium. This increases sustainability in the supply chain and, as a result, reduces the entire car’s carbon footprint.
Decarbonising the production phase has to encompass a reduction of CO2 emissions in the supply chain. That’s why Audi AG has launched a pilot project involving the alloy wheels on the new Audi e-tron GT, the 100% electric, high-performance gran turismo.
The wheels are made with low-CO2 emission aluminium supplied by Alcoa, which has invented an innovative smelting process that emits oxygen instead of carbon dioxide. The ELYSIS joint venture is now developing this process further.
The inert anode
The ELYSIS smelting technology causes no direct CO2 emissions – a big step forward compared to the traditional, highly energy-intensive process used to make aluminium.
The technology behind the process is a so-called inert anode. Insoluble in the electrolyte, it replaces the carbon anodes that are generally used during electrolysis – the process that makes primary aluminium.
The low-CO2 emission aluminium made by ELYSIS is then supplied by Alcoa to RONAL GROUP, which manufactures the 20-inch alloy wheels that are available as an optional for the Audi e-tron GT.
Light and aerodynamic
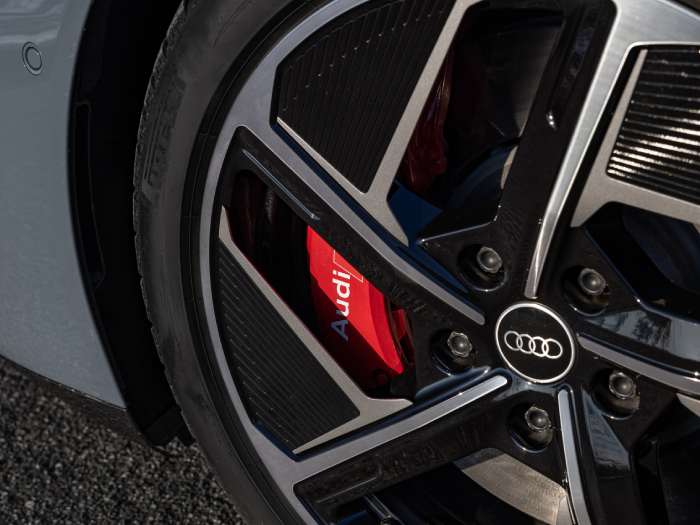
The wheels are produced using flow-forming technology for weight optimisation; the propeller-shaped design of the rim improves the aerodynamic properties while driving. The mounted blades, which largely cover the wheels, are just two to three millimetres thick and thus help to ensure aerodynamic efficiency.
This is not just a trivial detail: the Audi e-tron GT was designed specifically for sportiness and efficiency, and is able to attain an aerodynamic drag coefficient of 0.24. This excellent figure helps give the car a range of 488 or 472 kilometers (according to the WLTP).
Carbon neutral production
The e-tron GT is the first Audi electric car to be built in the Böllinger Höfe at the Neckarsulm site in Germany. Since 2020 the site has only been supplied with energy from renewable sources. A biogas-operated combined heat and power plant supplies the heat required for production.
In addition, Audi uses carbon credits from certified climate protection projects to offset the CO2 emissions that cannot currently be avoided. Similarly, the RONAL GROUP uses eco-electricity to produce the alloy rims; it too also offsets unavoidable emissions.
Aluminium Stewardship Initiative
Audi, Alcoa and RONAL GROUP are members of the Aluminium Stewardship Initiative (ASI). At the beginning of the year, Audi was the first car manufacturer to receive the “Chain of Custody” certificate from the ASI, which certifies that the company works with aluminium in a sustainable way, taking into account social and ecological aspects, as well as business ethics.
By 2018, Audi had already initiated its “CO2 program in the supply chain” with the aim of successively decarbonising its whole supply chain. The program looks to reduce carbon dioxide emissions in the upstream manufacturing processes for each vehicle produced by focusing on components and raw materials.
Aluminium
“Aluminium is the focus of our CO2 program because producing this material requires a high energy input. The aluminium has already caused major carbon dioxide emissions in upstream processes before it even arrives at Audi. We are therefore actively searching for innovative processes that help reduce CO2 emissions as early as possible in the supply chain. The process created by ELYSIS is promising because it already has an impact on the raw material processing phase. These kinds of innovations allow us to increase sustainability in the supply chain and ensure that our models arrive at the customers with a smaller carbon footprint,” says Marco Philippi, Head of Procurement Strategy.
Source: AUDI AG