Audi starts production of electric motors for PPE platform in Györ
For 30 years, the Hungarian plant has been an excellence and is currently the world's largest engine production facility. Around 700 technicians work on the three lines for the new electric motors, in three shifts.
Audi has started production of the new generation of electric motors at its Györ plant in Hungary. The engines have been developed for the PPE (Premium Platform Electric), an innovative platform jointly developed by Audi and Porsche and dedicated to high-performance fully electric cars, whose strengths include high efficiency and a new electronic architecture that opens up new possibilities for digitalisation. The new engines will debut in the Audi Q6 e-tron, the first PPE-based model, production of which will start in Ingolstadt by the end of this year.
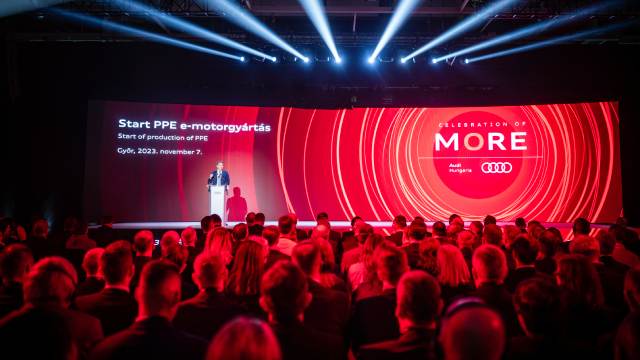
Györ's excellence
"From 2018 to date, Györ's highly skilled and specialised workers have already built more than 400,000 electric powertrains, valuable know-how that will be put to use in the next-generation electric motors for the PPE platform" explains Gernot Döllner, CEO of Audi. It will therefore be the Hungarian plant, which already produces the drive system for the Audi Q8 e-tron, that will also produce that for the new Q6 e-tron. In parallel, another production area in Györ is being set up for electric motors that will be used in vehicles based on the evolution of the Volkswagen Group's MEB platform. For PPE electric motors, Audi has installed three new lines, involving 700 employees: the one for stator production has 28 stations, while the one for transmission components has 15. The assembly of an axle requires 190 individual steps.
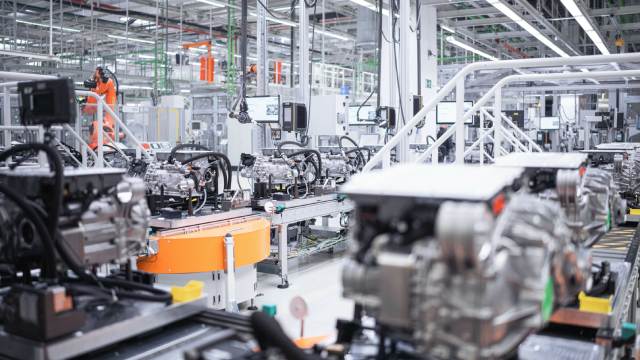
2,000 engines per day
Specialised technicians in Györ work in three shifts, producing up to 2,000 engines per day for the PPE platform. The new production lines make even better use of the vertical integration concept than their predecessors. "The start of production in Györ marks an important milestone in the ramp-up of production of the Audi Q6 e-tron" says Gerd Walker, Audi Board Member for Production and Logistics. "I know from personal experience how passionately people work in Györ and how systematically they implement the further electrification of the world's largest engine plant. This site is a pillar for Audi's global production network, also thanks to its carbon neutral certification". Walker was Managing Director for Vehicle Production at Audi Hungaria from 2012 to 2016.
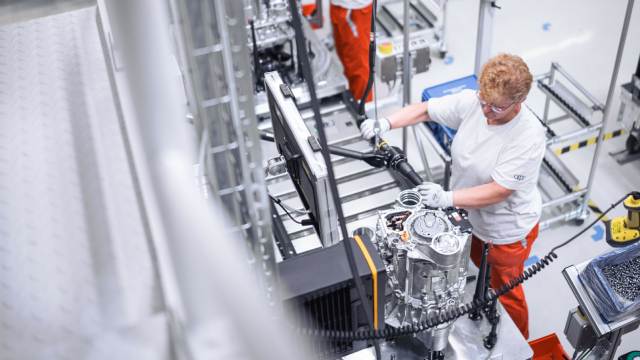
360factory
The transition to electric mobility is an opportunity for Audi Production, which is completely transforming its global production network with the 360factory programme. The plan is based on a holistic and sustainable approach, involving the digitisation and upgrading of all plants. Györ is already carbon neutral since 2020 also thanks to Europe's largest roof-mounted photovoltaic system and the extensive use of geothermal energy. In addition, the logistics company DB Cargo is responsible for ensuring that the transport of PPE electric motors from Györ to Ingolstadt is carbon neutral.
Audi Hungaria
The Györ plant employs around 12,000 people and has a 30-year success story, during which it has invested around EUR 12 billion and become a leading player in Hungarian industry. The new CUPRA Terramar will also be built in Györ, increasing synergies with the rest of the Volkswagen Group's production network. The site is also involved in the production of aluminium body components, in particular hatches, doors and halls, for Audi, Bentley and Lamborghini.
Source: AUDI AG
VGI | Responsible OU: VP | Creation date: article date | Class 9.1