AI learns to see at the Volkswagen Smart.Production:Lab
Thanks to image recognition, artificial intelligence can automate checking processes in logistics, making them more efficient: here is how Industrial Computer Vision is being developed at the Smart.Production:Lab.
The blue boxes are positioned. A small camera records the contents – all ready for the test. Seconds later, a green check appears on the monitor indicating that they have been filled exactly as they should be. What might seem unspectacular is actually the result of highly sophisticated technology: artificial intelligence.
At the Smart.Production:Lab in Wolfsburg, a group of IT specialists are focusing their efforts on artificial intelligence, training it to carry out tasks independently. An example of this is using the technology to check whether component delivery boxes for production are packed correctly – in the laboratory or in genuine logistics scenarios.
Training AI
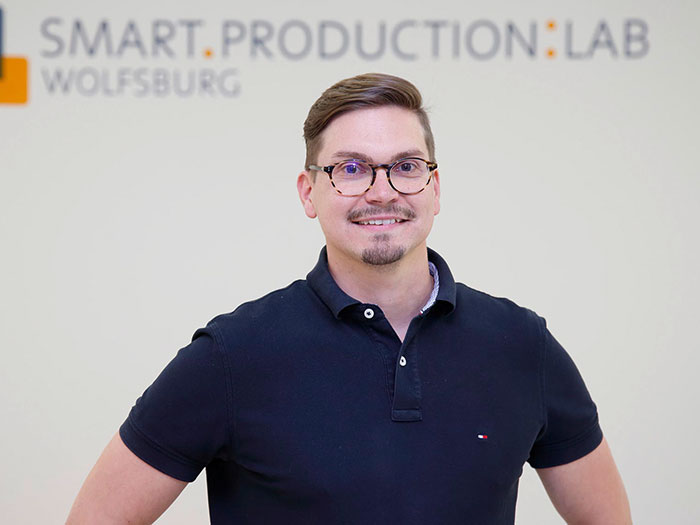
Industrial Computer Vision is the name of the system that has been developed in collaboration with other labs and the Volkswagen’s Software Development Center in Dresden. The basic idea begins with people training artificial intelligence so that it can evaluate optical data and detect errors extremely reliably and very quickly – in just fractions of a second.
“The user interface is so simple that anyone can operate it and train the AI independently. You don’t have to be a computer scientist,” says Nicolas Hummel, one of the Smart.Production:Lab specialists. By applying this technology, Volkswagen Group expects to generate savings in the double-digit million-euro range over the next few years, especially in production and logistics.
Maximum customisation
Industrial Computer Vision offers a toolbox for the implementation of artificial intelligence use cases. All you need is a person who prepares enough training material – in this case, photos with correctly and incorrectly packed boxes – and marks it accordingly.
“The artificial intelligence then learns independently to distinguish faultless from faulty results,” says Hummel. A few days of training are usually enough to make a neural network ready for use.
Joined-up working
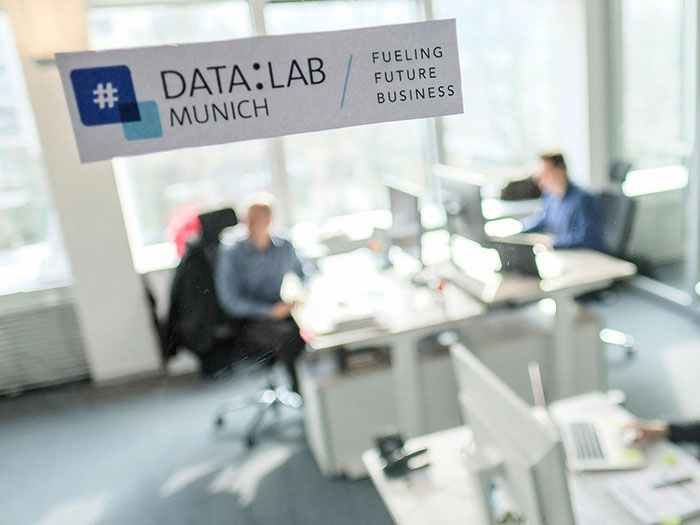
The experts at the Wolfsburg Smart.Production:Lab work in collaboration with other competence centers in the Volkswagen Group. Computer Vision is a good example: while the software is written in Wolfsburg, the Data:Lab in Munich is concerned with improving neural networks and the Software Development Center in Dresden tests the system in practice and provides feedback.
And in a logistics hall in Wolfsburg the automatic container control system is already in use – a successful outcome for the technology. Naturally, people in the images are automatically pixelated to comply with data protection regulations, a solution that will be standard in all Computer Vision applications.
The versatility of AI
Another possible application of Industrial Computer Vision is currently being tested at Porsche in Leipzig. Here, artificial intelligence checks labels that are attached to every single car. The labels contain vehicle information such as instructions for airbags, and are written in various languages according to the market where the car will be sold. AI checks the images in real time and provides feedback as to whether everything is in order.
From next year, the application will be used at other locations via the Industrial Cloud, which links Volkswagen Group’s plants together. Meanwhile in the Smart.Production:Lab, work continues on extending the benefits of the application to the entire company. “Our aim is an online offering from which each department can download the appropriate applications as if they were in a library,” adds Hummel’s colleague, Reda Jaber. A pilot test is already underway.
Freedom and independence
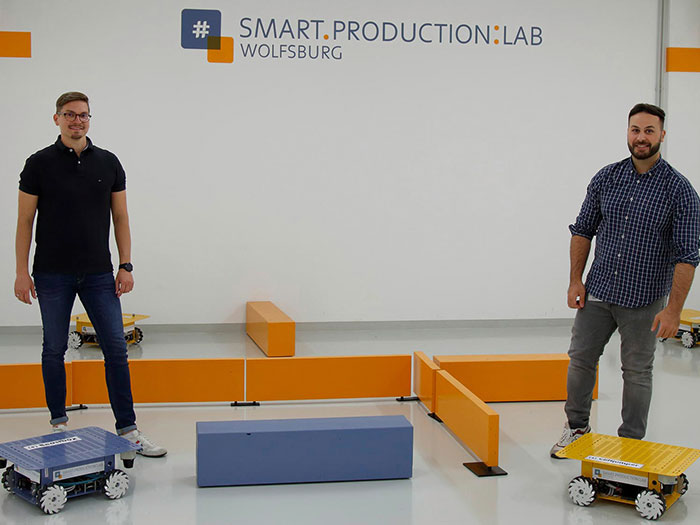
The experts at the Smart.Production:Lab have also been working on driverless transport systems, data analysis, robotics and the Internet of Things (IoT). “What I like best is the freedom to try out new technology: anyone can contribute ideas, and all employees are heard,” says Jaber.
Flat hierarchies allow the individual teams to organize themselves independently and also have a say in selecting the most appropriate projects – as was the case for Computer Vision.
Source: Volkswagen Newsroom