Flexible working hours on the production line: Audi’s pilot project
An innovative working time model that allows shift workers to work part-time in production: the unique Audi project promotes a modern and innovative working culture.
The shift work that characterises industrial production is certainly not know for its flexibility. Schedules are usually rigid and it is very difficult to make changes. This is why people who change to part-time work because of personal circumstances are often required to change departments. Audi has started a pilot project as part of its transformation and it has pioneering potential in car production.
Innovation in the paint shop
In the paint shop in Ingolstadt, even shift workers can work part-time, thanks to an innovative working model that was developed by Audi employees of all levels and age groups together with the Works Council and the Institute for Social Science Research (ISF, Institut für sozialwissenschaftliche Forschung) in Munich. All this took place within the framework of the Practical Workplace Workshop: More Flexible on Shift Duty, an initiative supported by the German Ministry of Labour and Social Affairs.
Working flexibility in practice
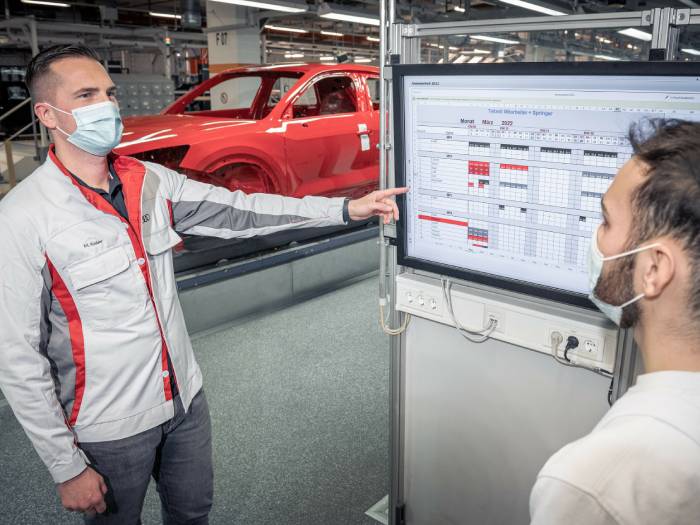
In practice, it works very simply: trained floaters fill in the gaps in time due to the absence of part-time workers. Those floaters come from other areas of the paint shop: they are trainees, employees with limitations or office staff.
For example, a mother who has just returned from maternity leave may need a change from her usual schedule. Then a qualified colleague takes over, allowing her to have flexible working hours.
Quality of work
As far as experts are currently aware, Audi is the first employer in Germany to develop such a solution, which allows employees to help shape the future of their work. "This initiative shows that the best ideas come from the company itself and also confirms that we put people, with their individual needs and skills, at the centre. We are promoting a modern teamwork culture for all our employees," explains Sabine Maassen, Audi Board Member for Human Resources.
Team spirit
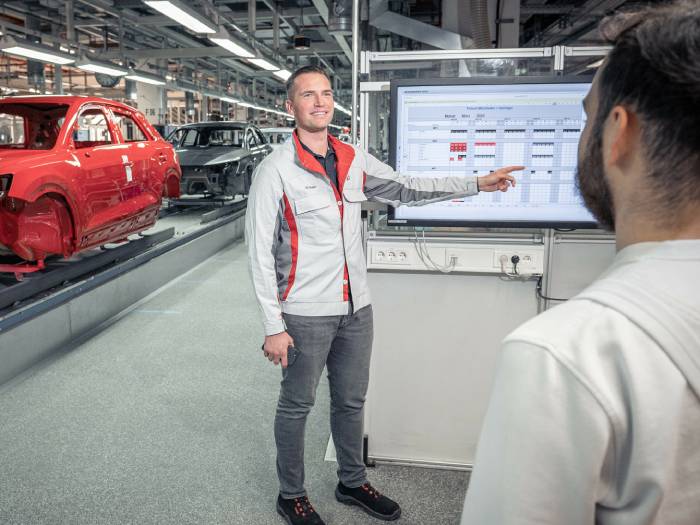
Achim Heinfling, plant manager at Audi’s Ingolstadt site, agrees: "Flexible working hours are very difficult to implement in car production, because it is highly efficient and adheres to timescales timed to the second. So I'm all the more excited about this unique pilot project, which was born out of creativity and a practical team spirit. We are now testing how far we can extend it to other manufacturing areas as well".
Collaboration and training
"The work in the Practical Laboratory brings together the experience and knowledge of all the people at the plant - the employees, who are directly involved, the Works Council and the management - to develop shared solutions that are acceptable to everyone," emphasises Peter Mosch, Chairman of the Audi General Works Council. "In other words, we work together across the board on equal terms, to go beyond formal hierarchies. Our experience shows that these methods are also highly valuable in other areas at Audi and for other companies. Of course, we need a modern collaboration and training culture that is oriented to sharing and participation".
Expanding innovation
At present, sixteen employees are benefiting from the pilot project for flexible shift work and thirty are part of the group. Audi intends to extend this working model to other areas of production as well, since the process of making work flexible is well underway, both in the offices and, indeed, in the production departments.
Source: AUDI AG
VGI | Responsible OU: VP | Creation date: article date | Class 9.1